Ewolucja Lean – od narzędzi do kultury w Philips w Kętrzynie
Philips Lighting, jest światowym liderem w zakresie produktów oświetleniowych, systemów i usług. Nasze zrozumienie tego, jak oświetlenie wpływa pozytywnie na ludzi, w połączeniu z naszym technologicznym know-how pozwala nam dostarczać cyfrowe innowacje oświetleniowe. To otwiera nowe korzyści biznesowe, dostarcza bogatych doświadczeń użytkownikom i przyczynia się do poprawy ich życia. Sprzedajemy więcej produktów i systemów oświetlenia energooszczędnego niż jakakolwiek inna firma. Jesteśmy liderem w branży połączonych systemów i usług oświetleniowych. Poprzez światło kształtujemy i kreujemy przestrzeń wokół nas: domy, budynki i przestrzenie miejskie.
W Polsce Philips Lighting prowadzi działalność produkcyjną w zakładach produkcyjnych: w Pile, Kętrzynie i Pabianicach. Zakład Philips w Bielsku-Białej jest dostawcą komponentu: trzonków do żarówek, do innych fabryk. W sumie spółka zatrudnia w Polsce ponad 4600 osób, co sprawia, że znajduje się w gronie siedemdziesięciu największych polskich pracodawców. Wg rankingu Randstad spółka znajduje się również w pierwszej dwudziestce najwyżej ocenianych pracodawców. Otrzymała również wyróżnienie Great Place to Work. Spółka jest również 9. największym polskim eksporterem.
Oddział Philips Kętrzyn
Obecnie zakład produkcyjny Philips w Kętrzynie zatrudnia ponad 700 osób. Od kilku lat rośnie aktywność jako czołowego producenta w koncernie. Zakład rozwija i produkuje profesjonalne rozwiązania oświetleniowe do zastosowań wnętrzowych i zewnętrznych. Fabryka wytwarza m.in. oświetlenie uliczne, rozwiązania oświetleniowe dla biur, szkół i szpitali, ale również sklepów, budynków przemysłowych, stacji benzynowych, a nawet stadionów. W ramach kętrzyńskiego zakładu Philips Lighting działa również Centrum Badawczo-Rozwojowe. Jest ono jednym z czterech tego typu ośrodków Philips Lighting na świecie, przy czym jest jedynym, które opracowuje rozwiązania oświetleniowe zarówno do zastosowań wnętrzowych, jak i zewnętrznych.
Dział badawczo-rozwojowy pracuje nad rozwiązaniami najnowszej generacji, w większości z obszaru LED, czyli najbardziej energooszczędnej technologii oświetleniowej na świecie, pozwalającej ograniczyć zużycie energii od 50 do 80 proc. W Centrum Badawczo-Rozwojowym zatrudnienie znajduje obecnie ponad 50 osób. Innowacyjne rozwiązania opracowane w Centrum Badawczo-Rozwojowym są następnie wdrażane do produkcji m.in. w fabryce Philips Lighting w Kętrzynie. Wyprodukowane innowacyjne technologie coraz częściej znajdują swoje zastosowanie w Polsce. W największej polskiej gminie Przytyk oświetlonej w 100 proc. technologią LED, zastosowano ponad 1000 opraw Philips LED ClearWay (Rys. 1), generujących białe światło, które zostały zaprojektowane i wyprodukowane w fabryce oświetleniowej Philips Lighting w Kętrzynie. Po modernizacji oświetlenia w gminie Przytyk udało się zmniejszyć zużycie energii o ok. 60 procent.
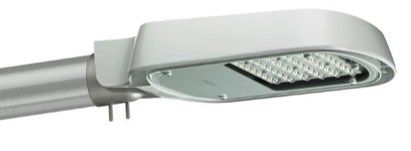
Rysunek 1 Oprawa zewnętrzna Clearway produkowana w Philips w Kętrzynie
Philips w Kętrzynie rozpoczął swoją przygodę z Lean w połowie 2007 roku. Rozpoczynając od wdrożenia narzędzi Lean w wybranej rodzinie produktu, w obszarze produkcyjnym. W odstępach półrocznych wprowadzano narzędzia w kolejnych rodzinach, aż do 2009 roku. Lata 2009-2010 to czas intensywnego rozwoju fabryki (oddana do użytku rozbudowana o 11 tysięcy m2 hala produkcyjna) związanego z transferem produkcji i projektowania opraw oświetleniowych z innych zakładów.
Decyzją kierownictwa, w lutym 2009 r, uruchomiono 5 równoległych projektów transformacji Lean w zakładzie produkcji opraw oświetleniowych. W 2011 roku pod hasłem „Dążenie do doskonałości” wprowadzano i usprawniano rozwiązania wypracowane do tej pory: kolejki FIFO, heijunki, strategie dostarczania komponentów. Kolejne dwa lata to okres stabilizowania i usprawniania wdrażanych narzędzi oraz powolna ekspansja na pozostałe obszary w przepływie strumienia wartości, czyli w obszarze magazynu i dystrybucji. W 2013 roku organizacja musiała odpowiedzieć sobie na pytanie „Czy jesteśmy gotowi na strukturalne wdrożenie programu Lean?” (Rys. 2). Odpowiedź twierdząca była deklaracją przystąpienia do wdrażania Lean wg przyjętego w Philips modelu. Proces wdrażania Lean w tym modelu jest podzielony na 5 faz (Rys. 3).
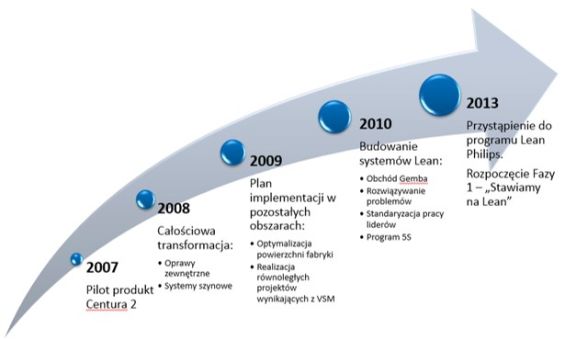
Rysunek 2. Podróż Lean – od narzędzi do systemu
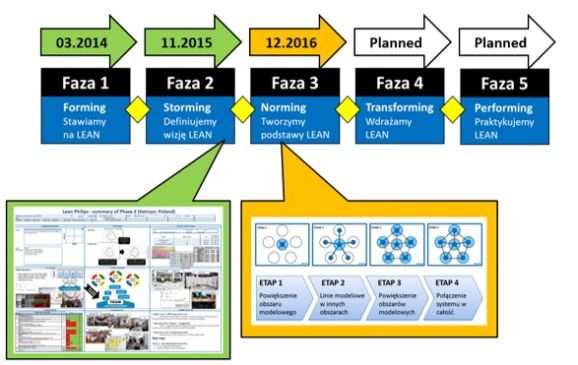
Rysunek 3. Model wdrożenia Lean w 5 fazach
Problemy to możliwości. Czy je rozwiązaliśmy i przekuliśmy w sukces?
W pierwszej fazie zdiagnozowano kluczowe parametry do osiągnięcia sukcesu w fazie 5. Faza 1 to również odpowiedź na pytanie, czy organizacja jest gotowa do rozpoczęcia programu według metodologii 5 faz.
Zarząd przeszedł 2-tygodniowe warsztaty Lean z przejściem krzywej zmiany. Zdefiniowano obszar pilotowy, który będzie naszym „modelem doskonałości” – wybór padł na przepływ jednej rodziny produktów. Mowa tu o przepływie End2End – od magazynu komponentów, poprzez produkcję, aż do magazynu wysyłek, nie zapominając oczywiście o działach wspierających jak: logistyka, inżynieria procesu, zakupy, jakość, dział konstrukcyjny, utrzymanie ruchu oraz HR.
Zadaniem zarządu było również opracowanie strategii i misji firmy. To co było w niej kluczowe, to oparcie strategii firmy o kulturę Lean. Wiedzieliśmy, że aby budować kulturę Lean, to filozofia Lean musi być wbudowana w strategię firmy, za której realizację odpowiada kierownictwo (Rys. 4).
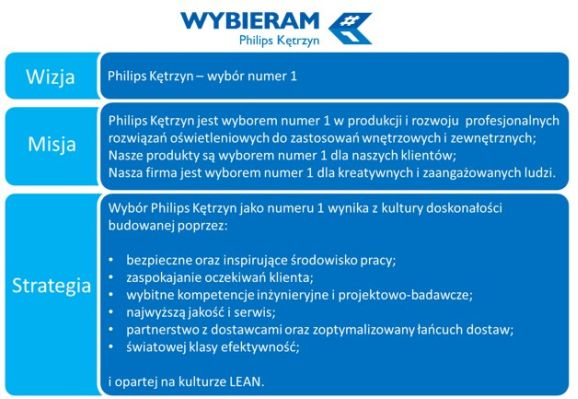
Rysunek 4. Misja, wizja i strategia Philips Kętrzyn oparta na kulturze Lean
W marcu 2014 r organizacja przeszła audyt wewnętrzny z wynikiem pozytywnym, co oznaczało przejście z Fazy 1 do Fazy 2 (Rys. 5). Pierwszy sukces za nami! Plan jak zrealizować Fazę 2 mieliśmy.
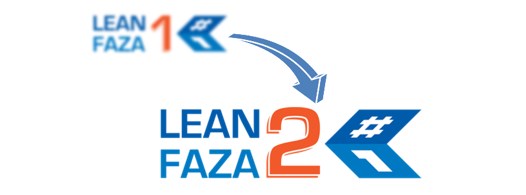
Rysunek 5. Wizualizacja przejścia między Fazami Lean
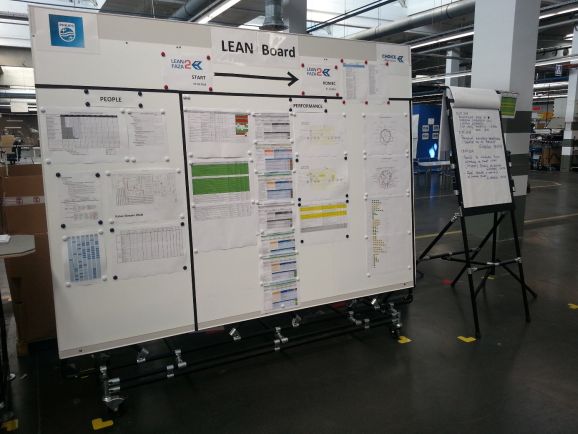
Rysunek 6. Tablica Lean w Fazie 2
Zmiana kultury Lean była monitorowana na przeglądach programu Lean z udziałem kierownictwa i właścicieli projektów związanych z Lean. Tablica przeglądów (Rys. 6) została zaplanowana w duchu PDCA oraz ciągłego doskonalenia w trzech kategoriach:
- Bezpieczeństwo i Wizja
- Kultura (m.in. 6S, Gemba Walk, Rozwiązywanie problemów, TPM AM, system sugestii)
- Wyniki – Realizacja i przegląd projektów usprawniających wynikających z mapy strumienia wartości stanu przyszłego.
Przeglądy w takiej formule trwały przez kilka miesięcy, a wszyscy uczestnicy mieli poczucie traconego czasu i trwania w impasie. Projekty były opóźnione, uczestnicy nie brali udziału w przeglądach tłumacząc się innymi priorytetami lub brali udział biernie jako słuchacze. Za kilka miesięcy miał odbyć się audyt wewnętrzny, którego wizja potęgowała poczucie, że coś tu jest nie tak.
Jak oceniali to podejście transformacji kultury Lean członkowie linii modelowej oraz uczestnicy przeglądów i właściciele projektów?
- Zadania i projekty Lean były dodatkiem do wykonywanych obowiązków. Nie miały nadanego priorytetu oraz przyznanych zasobów.
- Prowadzone projekty nie obejmowały usprawnienia w całym strumieniu przepływu wartości.
- Zadania były podzielone pomiędzy działy, więc były realizowane silosowo bez wiedzy i zrozumienia całości transformacji (Rys. 7).
- Przeglądy były reaktywne, sprawozdawcze. A czas analizy problemów (o ile zostały zgłoszone) oraz podejmowania decyzji był kilkutygodniowy.
Pracownicy linii modelowej nie wiedzieli, co omawia się podczas przeglądów, a obecność kierownictwa na przeglądzie odbierano jako formę kontroli. Wdrażano narzędzia i systemy bez angażowania ich użytkowników i nie wyjaśniano, jaki jest ich cel.
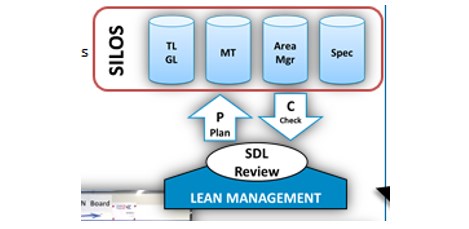
Rysunek 7. Model silosowy we wdrażaniu kultury Lean
Audyt wewnętrzny Fazy 2 Lean był przysłowiową kropką nad „i”. Kierownictwo otrzymało szczegółowy raport o lukach we wdrażaniu blisko 80 % narzędzi Lean oraz braku podejścia do wdrażania kultury Lean. To był andon dla całej organizacji. Efektem był STOP i zorganizowanie warsztatu Kaizen (Kaizen Event) z udziałem kierownictwa. Zdefiniowano szczegółowo problem, przyczyny i przeciwdziałanie.
Planuj powoli, działaj szybko
Pierwszy Kaizen Event był kołem zamachowym pozostałych warsztatów usprawniających.
Kluczowe zmiany, jakie wprowadzono:
- Strukturalne wydzielenie linii modelowej od pozostałej części fabryki. Powstało nowe centrum produkcyjne z zespołem, który jest zaangażowany i świadomy zmiany.
- Przydzielenie zasobów do prowadzenia projektów w postaci zespołu wsparcia, który razem, z udziałem członków linii modelowej analizował, planował i realizował projekty oraz zadania (rys. 8) poprzez m.in. Kaizen Event, coaching, commcell [regularne spotkania zespołu przy tablicy o stałym layoucie, w kwestiach People (Ludzi), Performance (Wyniki), Continuous Improvement (Ciągłe doskonalenie)].
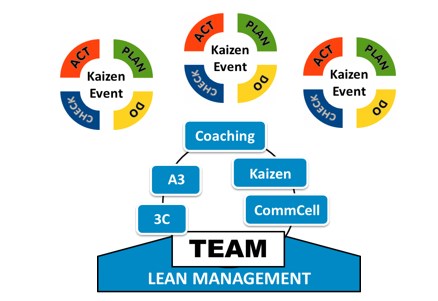
Rysunek 8. Model zespołowego wdrażania kultury Lean
Początek pracy zespołu wsparcia wymagał określenia modelu pracy. Formą, która się sprawdziła to wspólna, z udziałem wszystkich członków zespołu wsparcia, analiza kryteriów Lean wymaganych w Fazie 2.
Wspólnie określono harmonogram prac nad poszczególnymi narzędziami, biorąc pod uwagę ich wzajemne powiazania i wpływ. W poprzednim modelu wdrożenia nie miało to miejsca. Po raz kolejny metoda post-it okazała się najbardziej elastyczną i wydajną metodą w planowaniu i przeglądach realizacji postępów we wdrażaniu Lean (Rys. 9).
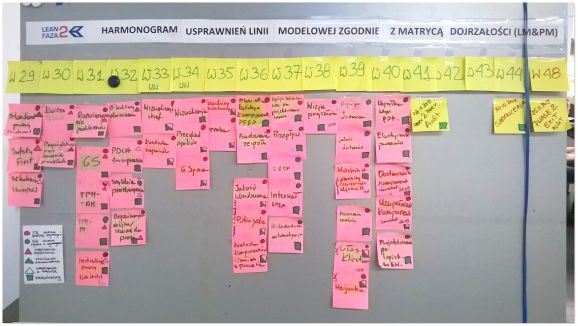
Rysunek 9. Harmonogram usprawnień linii modelowej
Wdrożenie narzędzi Lean było realizowane w formie Kaizen Event (Rys. 10), poprzedzonych analizą problemu, zastosowaniem A3. Zaangażowany był każdy szczebel organizacji, od operatorów zaczynając, poprzez specjalistów, ich przełożonych, kończąc na głównym kierownictwie. To istotny element wprowadzania i utrzymania kultury Lean. Wszyscy byli zaangażowani. Mieli jasną wizję i cel krótkoterminowy. Działanie poprzez kaizen to sposób codziennej pracy. To planowanie, projektowanie, prowadzenie spotkań, rozwiązywanie problemów i usprawnienia procesów. To praca sama w sobie.
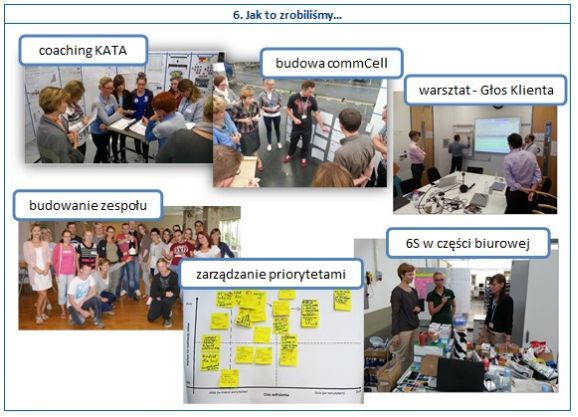
Rysunek 10. Kaizen Eventy w nowym modelu Fazy 2 Lean
Lider jest nauczycielem
Zmiana kultury to zmiana, której wszyscy się boją i zaprzeczają, że jest potrzebna. Dlatego tę zmianę zaczęliśmy od kierownictwa, które dając przykład swoim zachowaniem zachęca to podobnego postępowania. Sama zmiana jest również bardzo istotna. W naszym przypadku okazało się, że operatorzy z linii modelowej nie chcą być Lean, ponieważ to oznacza odmienność. Wolą pozostać w niedotkniętym jeszcze zmianą obszarze fabryki. Dopiero praca nad postawami w zespole pozwoliła uwolnić w pełni drzemiący potencjał zespołu.
Gdy zespół wspierający przeniósł swoje biuro na Gembę i pracował na Gembie, w połączeniu z klarowną komunikacją do zespołu operatorów, pojawił się efekt synergii. Podczas Kaizen Event zespołu wspierającego i operatorów wyznaczono role, oczekiwania i zadania dla każdego członka zespołu. Został stworzony jeden zespół, który wiedział, jakie ma zadanie do wykonania.
Kierownictwo ma bardzo istotny wpływ na przejście przez transformację. Pojawianie się na linii modelowej i coaching liderów i operatorów to tylko początek. W naszym przypadku efektem było pełne zaangażowanie kierownictw, włącznie z pracą członków zarządu na linii modelowej jako operatorów. Pozwoliło to na poznanie problemów dnia codziennego każdego operatora. Wreszcie obie strony mogły się zrozumieć i zmierzać ku prawdziwej północy.
Mały krok linii modelowej, duży krok dla organizacji
Etap budowania linii modelowej i wypracowania rozwiązań został bardzo dobrze oceniony przez zewnętrznych audytorów. Co istotne, członkowie zespołu modelowego są przekonani do filozofii Lean.
Automatycznie rodzi się pytanie, jak dążymy do prawdziwej północy w kolejnych krokach, jakie mamy plany?
Dokładnie takie pytanie zadał sobie zespół zarządzający na początku tego roku. Jak dążyć do ciągłej doskonałości, by nie zgubić rozpędu.
Odpowiedź przyszła na kolejnym Kaizen Event, gdzie razem z zespołem linii modelowej i zespołem zarządzającym zbudowaliśmy model przejścia przez trzecią fazę Lean w modelu 5-fazowym (patrz: Rys. 3).
Uzgodniono założenia, które muszą być spełnione, aby iść dalej, między innymi:
- Zespół linii modelowej, tzw. agenci zmiany, pozostaje razem.
- Przed transformacją całego zakładu powiększamy obszar modelowy na więcej niż 2 linie montażowe (plus wiele innych zmiennych, np.: zwiększenie ilości rodzin produktów, rotacja pracowników, pracownicy tymczasowi, procesy współdzielone) (Rys. 11). Uwiarygadniamy obszar modelowy, eksperymentując ze standardami na większej ilości zmiennych.
Plany na najbliższy okres pokazuje rys. 11.
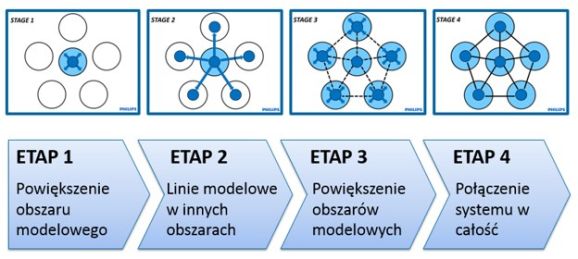
Rysunek 11. Etapy wdrażania kultury Lean w całej organizacji
Obecny rok, 2016, jest rokiem wiedzy o Lean w organizacji. Wszyscy pracownicy będą certyfikowani na poziomie minimum podstawowym (Rys. 12).
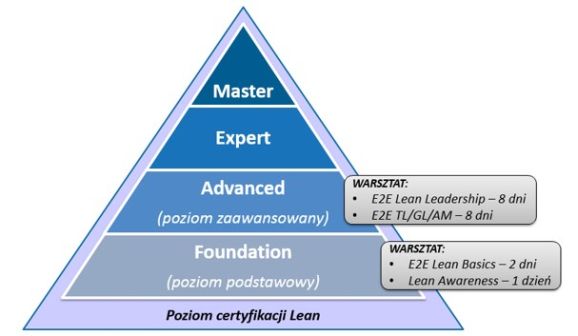
Rysunek 12. Poziomy certyfikacji Lean
Budując świadomość w poszczególnych etapach, chcemy zaangażować wszystkich pracowników w ciągle doskonalenie. Zgłaszanie sugestii i realizacja codziennych kaizenów, udział w Kaizen Event, prowadzenie projektów Green Belt i projektów usprawniających z wykorzystaniem DMAIC, A3 to aktywny udział w doskonaleniu. Drobne inicjatywy inicjują projekty i działania usprawniające i sprawiają, że problemy są podejmowane (Rys. 13).
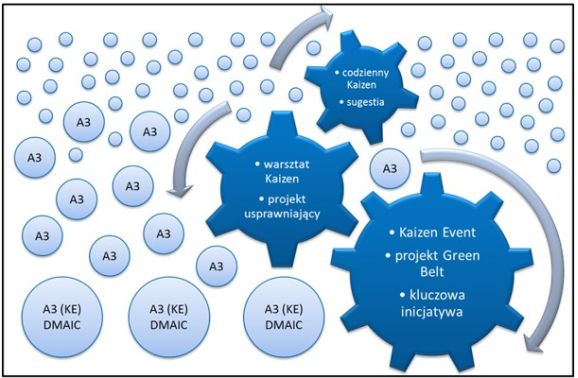
Rysunek 13. Model poziomów usprawnień w organizacji
Efekty zmiany kulturowej są widoczne we wskaźnikach biznesowych w tabeli na Rys. 14.
Iwona Trumińska – Kierownik Centrum Produkcji, Philips Lighting Poland – Oddział w Kętrzynie
Grzegorz Kozłowski – Koordynator Lean, Philips Lighting Poland – Oddział w Kętrzynie
Dariusz Kret – Operator produkcji, Philips Lighting Poland – Oddział w Kętrzynie
Artykuł stanowi przedruk publikacji zamieszczonej w materiałach konferencyjnych XVI Konferencji Lean Management, która odbyła się we Wrocławiu w dniach 7-9 czerwca 2016 roku. Konferencja, która organizowana jest corocznie przez Lean Enterprise Institute Polska, przeznaczona jest dla sektorów produkcyjnego i usługowego. Zapraszamy do odwiedzenia obszernego serwisu internetowego poświęconego Konferencji pod adresem www.leankonf.pl.
Artykuł został opublikowany dzięki uprzejmości i za zgodą firmy Philips Lighting Poland – Oddział w Kętrzynie.