Skutki finansowe działań doskonalących realizowanych w oparciu o Lean Manufacturing
Wiele firm usiłujących wdrażać programy usprawnień napotyka problemy związane ze stosowanymi systemami pomiaru efektywności. W szczególności dotyczy to sprawozdań finansowych, które motywują często pracowników do działań sprzecznych z założeniami strategii firmy. Klasycznym przykładem jest przedsiębiorstwo produkcyjne wdrążające elementy Lean Manufacturing, w którym skuteczność działań oceniana jest przy użyciu tradycyjnych metod rachunku kosztów
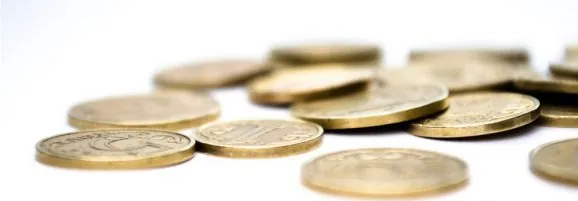
Wiele firm usiłujących wdrażać programy usprawnień napotyka problemy związane ze stosowanymi systemami pomiaru efektywności. W szczególności dotyczy to sprawozdań finansowych, które motywują często pracowników do działań sprzecznych z założeniami strategii firmy. Klasycznym przykładem jest przedsiębiorstwo produkcyjne wdrążające elementy Lean Manufacturing, w którym skuteczność działań oceniana jest przy użyciu tradycyjnych metod rachunku kosztów (np. analizy odchyleń z wykorzystaniem rachunku kosztów standardowych). System stosowanych miar często „ciągnie” pracowników w przeciwnym kierunku niż założenia przyjęte w programie doskonalenia. Zwykle zwycięża „kierunek finansowy” natomiast realna szansa na poprawę skuteczności funkcjonowania systemu produkcyjnego zostaje bezpowrotnie utracona1.
Redukcja zapasów a wynik finansowy przedsiębiorstwa
Stosowane procedury kalkulacyjne i sprawozdawcze w większości przedsiębiorstw sprawiają, że eliminowanie zapasów zwiększa koszty produkcji prowadząc do spadku generowanych zysków. Wynika to z faktu, iż firmy kalkulują na ogół koszty produkcji w sposób zaprezentowany w tabeli 12.
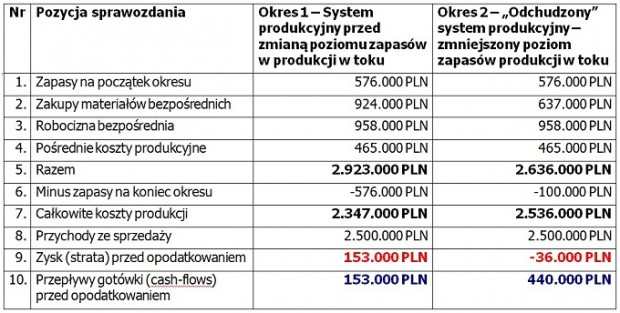
W zilustrowanym przykładzie przyjęto, że zarząd firmy zmniejszył poziom zapasów produkcji w toku z 576.000 PLN do 100.000 PLN, pozostawiając wszystkie pozostałe pozycje kosztowe na niezmienionym poziomie (za wyjątkiem zakupu materiałów bezpośrednich z poz. 2). W wyniku podjętych działań raportowany w pierwszym okresie sprawozdawczym zysk w wysokości 153.000 zł, w drugim okresie okazał się stratą w wysokości 36.000 zł (chociaż przepływy gotówkowe z poz. 10 znacznie się zwiększyły). W pierwszym okresie zapasy produkcji w toku i wyrobów zakończonych lecz nie sprzedanych zostały aktywowane w bilansie przedsiębiorstwa. Dzięki temu przychodom ze sprzedaży przeciwstawiono tylko tę cześć kosztów produkcji, która odnosi się do wyrobów sprzedanych (wyroby gotowe oraz w toku produkcji zostały potraktowane nie jako koszty lecz jako aktywa, czyli majątek firmy). W efekcie raportowany zysk był znacznie wyższy niż w okresie drugim, w którym poniesione koszty przyczyniły się prawie w całości do wyprodukowania wyrobów sprzedanych. Jak podkreślają Womack i Jones, zjawisko to może być wielce niekorzystne dla spółek giełdowych, o ile zarząd nie zdoła wcześniej wytłumaczyć zaistniałej sytuacji akcjonariuszom. Alternatywą jest radykalne zmniejszenie zatrudnienia i redukcja kosztów bezpośredniej robocizny oraz pośrednich kosztów produkcji mająca na celu odbudowanie krótkoterminowych zysków. Może to jednak stanowić przeszkodę, czy wręcz całkowicie uniemożliwić wdrożenie programu szczupłej produkcji, gdyż zdesperowani pracownicy mogą odmówić współpracy przy dalszym wdrażaniu programu4.
Finansowe skutki eliminacji marnotrawstwa
Problem uwolnionych zasobów przedstawiony zostanie na przykładzie projektu doskonalenia operacyjnego realizowanego w gnieździe obróbki mechanicznej hipotetycznego przedsiębiorstwa produkcyjnego. Całkowite koszty pracy gniazda określono na poziomie 20.000 zł w skali miesiąca, przy czym było ono w stanie wytworzyć w przeciągu tego okresu 4.000 sztuk wyrobów. Niewielkie inwestycje tj. zakup regałów i dodatkowych narzędzi w połączeniu ze zmianą organizacji pracy umożliwiły podniesienie wydajności pracy (znacząca ilość czasu potrzebna dotychczas na niewydajne i nie przynoszące wartości dodanej prace została zredukowana lub całkowicie wyeliminowana). W wyniku podjętych inicjatyw rzeczywista zdolność produkcyjna wzrosła do poziomu 5.000 sztuk miesięcznie. Zmalał również koszt wyprodukowania jednej sztuki z 5 do 4 zł/szt. Koszty działalności pozostały jednak niezmienione. Przyjmując, że w kolejnym okresie liczba zamówień spada do 3.000 sztuk, zaś całkowity koszt ich realizacji wynosi nadal 20.000 zł, koszt realizacji rzeczywiście otrzymanych zamówień wyniesie 12.000 zł (4 zł*3000 szt.), natomiast koszt niewykorzystanej zdolności produkcyjnej 8.000 zł5.
Wynika z tego, że jeśli menadżerowie nie zdołają zagospodarować osiągniętej redukcji w popycie na zasoby, działania doskonalące przyczynią się do wzrostu ich podaży, natomiast w żadnym razie nie doprowadzą do wzrostu zysków6.
Tak więc w przypadku inicjatyw mających na celu poprawę efektywności działań, owocującą redukcją wydatków, kadra kierownicza staje przed wyzwaniem wyeliminowania lub przemieszczenia dodatkowej niewykorzystanej zdolności produkcyjnej. Powyższy przykład pokazuje, że reorganizacja w miejscu gdzie ilość posiadanych zasobów przekracza już poziom potrzebny do wykonania przewidywanej ilości zadań, spowoduje powstanie jeszcze większej nadwyżki zdolności produkcyjnej7. Na rysunku 1 pokazano schematycznie zmianę w zapotrzebowaniu na zasoby produkcyjne powstałą w wyniku działań opisanych w przykładzie.
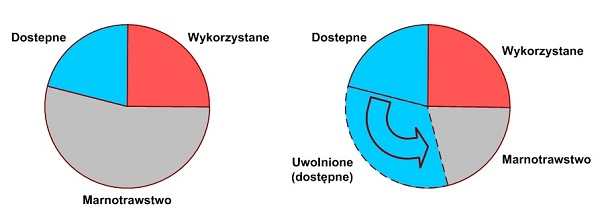
Z przedstawionego rysunku wynika, że sumaryczna podaż zasobów nie uległa zmianie, zmienił się natomiast sposób ich wykorzystania. Część zasobów stanowiąca w fazie początkowej marnotrawstwo, została przekształcona w zasoby dostępne. Innymi słowy zasoby te zostały „uwolnione”. Mimo to, przedsiębiorstwo nadal ponosi takie same koszty ich utrzymania, tak więc system księgowy traktuje je jako niezbędne do wytworzenia wyrobów sprzedanych w danym okresie. Jednak w rzeczywistości zasoby te nie są już potrzebne – aby zredukować koszty powinny zostać wyeliminowane lub wykorzystane w innych obszarach produkcyjnych przedsiębiorstwa.
Tradycyjne systemy pomiaru efektywności a potrzeby decyzyjne inżynierów
Praktyka stosowania tradycyjnych systemów rachunkowości dowodzi, że wykorzystują one nazbyt uproszczone procedury kalkulacji prowadzące do informacji zbyt opóźnionych, zbyt zagregowanych i zniekształconych 9. Szereg sprawozdań w systemie rachunkowości nie wspiera kierowników operacyjnych w działaniach nakierowanych na wzrost produktywności czy redukcję kosztów. Często sprawozdania te prowadzą wręcz do spadku produktywności, gdyż wymagają od menadżerów poświęcenia czasu na zrozumienie i wyjaśnienie raportowanych odchyleń, które mają niewiele wspólnego z rzeczywistością ekonomiczną i technologiczną. Nie będąc w stanie dostarczyć na czas wystarczająco precyzyjnych informacji na temat wykonywanych procesów, systemy rachunkowości odwracają uwagę od czynników mających największy wpływ na efektywność wytwarzania. Zarządzający, którzy polegają wyłącznie na okresowych sprawozdaniach finansowych, stają się szybko odizolowani od rzeczywistych, kreujących wartość procesów i działań10. Ponadto wiele działań w przedsiębiorstwie produkcyjnym stanowi marnotrawstwo powodowane dążeniem kierownictwa i pracowników firmy do spełnienia celów ustanowionych przez systemy rachunkowości. Typowym działaniem jest zwiększone tempo produkcji wyrobów na koniec okresu sprawozdawczego. W konsekwencji obniża się jakość, następuje zakłócenie przepływu wyrobów przez system produkcyjny, tracone są zasoby niezbędne do szybkiego wysłania wyrobów do klienta, zaś stworzona sztucznie iluzja produktywności przykrywa źle działający proces, który powinien zostać usprawniony11.
Kaplan i Norton podkreślają, iż wiele nowych programów, inicjatyw i zmian w procesie zarządzania firmą jest wdrażanych w środowisku, w którym zarządzanie opiera się na sprawozdaniach finansowych, które mają swoje korzenie w modelu księgowości rozwiniętym całe wieki temu dla potrzeb rejestrowania transakcji rynkowych dokonywanych przez niezależne podmioty 12. Johnson stwierdza wręcz, że począwszy od lat 50. dwudziestego wieku, kierownictwo i personel operacyjny wielu firm zatracił prawidłowy obraz pracowników, klientów i procesów, w wyniku skupienia całej uwagi na liczbach raportowanych w sprawozdaniach księgowych. Rozpoczął się pościg za „pseudo-imperatywami konkurencyjności” narzuconymi przez system informacji oparty na zasadach rachunkowości. Nie jest zatem przesadą twierdzenie, że w wyniku podobnych działań menadżerowie w przedsiębiorstwach zostali „odseparowani” od rzeczywistości produkcyjnej13.
dr inż. Tomasz Sobczyk, LEI Polska
Bądź na bieżąco i zyskaj darmową wiedzę w naszym newsletterze!
Nowości ze świata Lean, wydarzenia, oferty specjalne – dołącz, aby być na bieżąco!