Bellamy na ścieżce doskonałości: wdrożenie Lean Management w nowej fabryce u producenta wyjątkowych mebli
Bellamy to producent mebli, głównie dziecięcych i młodzieżowych, unikatowych, bo „rosnących wraz z dziećmi”. Firmą zarządza małżeństwo – Rita i Jakub Suchoccy. Marka jest obecna na rynku od ponad piętnastu lat, zdobyła kilka znaczących nagród, w tym prestiżową nagrodę Red Dot za wyjątkowy design.
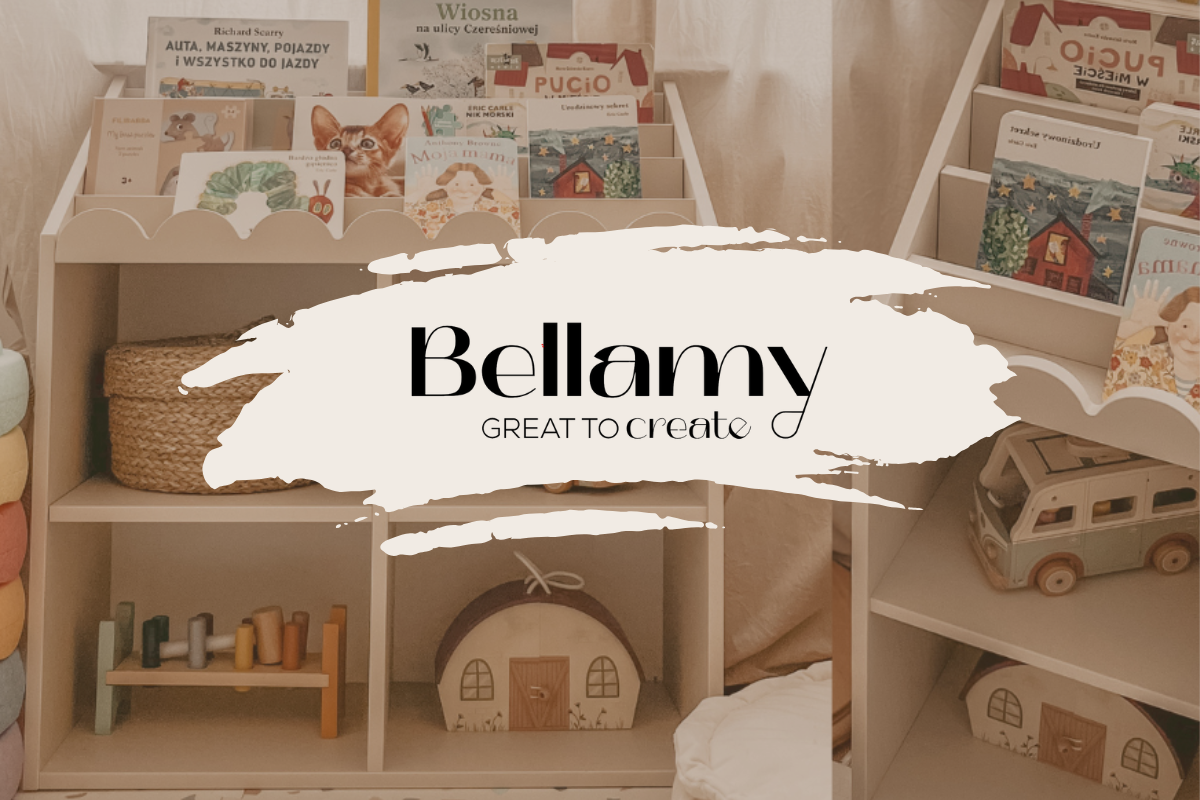
Bellamy to producent mebli, głównie dziecięcych i młodzieżowych, unikatowych, bo „rosnących wraz z dziećmi”. Firmą zarządza małżeństwo – Rita i Jakub Suchoccy. Marka jest obecna na rynku od ponad piętnastu lat, zdobyła kilka znaczących nagród, w tym prestiżową nagrodę Red Dot za wyjątkowy design.
Mimo sukcesów firma borykała się z pewnymi problemami w dziedzinie jakości i terminowości realizacji zamówień. Skłoniło to właścicieli do poszukiwania możliwości usprawnień. Zdecydowali się na wdrożenie narzędzi z zakresu Lean Management. Jako, że temat nie jest od razu intuicyjny, do współpracy zaproszono profesjonalnego konsultanta z Lean Enterprise Institute Polska. Działania te przyniosły pozytywne efekty i wyznaczyły kierunek dalszego doskonalenia.
Na początku firma koncentrowała się na projektowaniu i wprowadzaniu mebli na rynek przy jednoczesnym outsourcingu produkcyjnym. Po kilku latach zauważyła jednak wśród dostawców problemy z wdrażaniem ambitnego designu. Bellamy kładzie bowiem nacisk na dwa kluczowe aspekty: unikatowe wzornictwo (dość wspomnieć współpracę ze studentami Akademii Sztuk Pięknych) oraz wyjątkową funkcjonalność mebli. Pojawiały się trudności w przełożeniu innowacyjnych projektów na system produkcyjny. Fabryki, które uwielbiają produkować meble składające się z prostych prostokątów miewały kłopot z metodami produkcji i też znalezieniem odpowiednich materiałów. Te problemy prowadziły do wysokich wycen nowych produktów I długiego czasu na wdrażanie. Aby pokonać te przeszkody i skrócić czas dostarczenia produktów na rynek, firma zdecydowała się otworzyć własny zakład produkcyjny – będący częścią łańcucha dostaw.
Własny zakład produkcyjny dał firmie większą niezależność, ale jednocześnie sprawił, że pojawiły się kolejne wyzwania i konieczne do rozwiązania problemy.
Własny zakład produkcyjny – nowe problemy do rozwiązania
Zasadniczym problem, z którym zmagała się firma, były opóźnienia w dostawach do klientów końcowych. Wpływały one negatywnie na postrzeganie marki Bellamy, co odzwierciedlało się w opiniach klientów w Google. Obecnie opinie te są częściej bardzo dobre niż wcześniej. Wcześniejsze recenzje – mniej pochlebne – były w dużej mierze spowodowane właśnie opóźnieniami w dostawach.
Dążenie do szybkiego dostarczenia produktów – tuż po rozpoczęciu produkcji – doprowadziło do problemów z jakością. Skutkowało to zwrotami produktów w celu naprawy błędów, co znowu wywoływało dalsze opóźnienia. Reklamacje i problemy nie były systematycznie analizowane, a dane ich dotyczące nie były gromadzone w sposób metodyczny.
Proces doskonalenia produkcji utrudniał także brak standardów. Gdy ktoś był nieobecny, inni pracownicy mieli problem z jego zastąpieniem.
Przed rozpoczęciem współpracy z Lean Enterprise Institute Polska firma zmagała się z chaosem, także w zarzadzaniu, bałaganem na produkcji, nadmiarem zapasów, niską wydajnością, niedostateczną jakością i opóźnieniami, przez co zakład nie przynosił zysków.
Wsparcie profesjonalisty i wdrożenie narzędzi Lean Management
W obliczu tych problemów zarząd szukał profesjonalnego wsparcia. Przedstawiciele Bellamy najpierw wzięli udział w kilku szkoleniach otwartych prowadzonych przez Lean Enterprise Institute Polska w różnych organizacjach. Kolejnym krokiem był projekt zamknięty i współpraca z konsultantem LEI Polska Maurycym Szkolnickim. Na decyzję o profesjonalnym wdrożeniu Lean w zakładzie wpłynęło m.in. wcześniejsze doświadczenie właściciela z różnymi systemami produkcyjnymi, w tym Lean Management.
Rozumiał on, że firmy stosujące metody Lean są lepiej zorganizowane, bardziej uporządkowane i przyjazne pracownikom.
Projekt rozpoczęto od szkolenia całej ówczesnej załogi z podstaw Lean. Fabrykę zamknięto na 2 dni, a jej pracownicy wraz z właścicielami poznawali ogólne zasady filozofii Lean podczas wykładów i gier symulacyjnych prowadzonych w Centrum Kultury Foresterium przy uroczych ruinach klasztoru w Zagórzu. Po pierwszym dniu warsztatów, późnym popołudniem, jeden z właścicieli – Jakub Suchocki wraz z konsultantem – Maurycym Szkolnickim odwiedzili pustą fabrykę i zaplanowali wizję jej rozwoju w duchu Lean.
Pierwszym etapem było wdrożenie 5S. Jak mówią sami pracownicy – usprawniło to każde stanowisko w zakładzie. Wszystko znajduje się na swoim miejscu, co eliminuje potrzebę szukania narzędzi. A dzięki temu mocno skróciły się czasy wykonywania operacji i przezbrojeń maszyn, a także czas likwidowania ewentualnych awarii. Przy okazji 5S wdrożono również system zgłoszeń awarii i usterek jako wstęp do dalszych działań TPM.
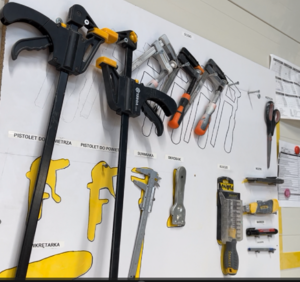
Po przekonaniu pracowników, że Lean to nie tylko piękna teoria, nadszedł czas na reorganizację przepływu materiałów i informacji. W tym celu użyto mapowania strumienia wartości. W firmie przeprowadzono klasyczne mapowanie, które poprzedzono szkoleniem z narzędzia dla całej załogi. Samą mapę stanu obecnego i mapę stanu przyszłego wraz z zaplanowaniem działań usprawniających wykonano z udziałem kierownictwa i specjalistów. Mapowanie pozwoliło wyznaczyć kierunki zmian. W rezultacie opracowano konkretne przewodniki produkcyjne i nowe marszruty. Zmniejszono wielkość partii produkcyjnych, co pozwala elastycznie reagować na zapotrzebowanie klientów.
Kolejnym etapem było wdrożenie narzędzi zarządzania Hoshin Kanri i spotkań operacyjnych. Spotkania operacyjne pomagają w codziennej organizacji pracy, co doceniają wszyscy pracownicy. „Pozwalają nam one rozpatrywać problemy z działu sprzedaży w większym gronie, poszukiwać rozwiązań i proponować je klientom końcowym” – tłumaczy Małgorzata Kuzicka-Mogilany, Kierowniczka Działu Sprzedaży. „Ułatwiają kierownikom komunikację z pracownikami w danym dziale. Mamy dobrą orientację na temat wydarzeń z poprzedniego dnia, a ludzie zaczęli zgłaszać więcej problemów” – dodaje Bernadetta Matyja, Brygadzistka w Dziale Pakowania.
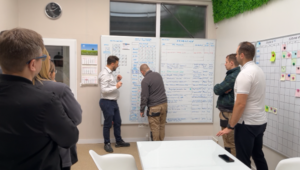
Wdrożono także metody rozwiązywania problemów, dzięki którym kierownictwo i brygadziści są w stanie permanentnie zlikwidować przyczyny źródłowe, zamiast „gasić pożary” i pozwalać, by ta sama przyczyna wielokrotnie zakłócała działanie fabryki.
Standaryzacja pracy została wdrożona z grupą brygadzistów i inżynierów. Standardy pozwoliły lepiej obsłużyć proces rekrutacji nowych pracowników, a jednocześnie uporządkowały tzw. technologiczną wiedzą plemienną. Dzięki temu brygadziści nie muszą już poświęcać czasu na dodatkowe szkolenie pracowników, a doskonalenie jest łatwiejsze.
Trudności podczas wdrożenia Lean Management
Zasadniczą trudność stanowiło przede wszystkim znalezienie czasu na szkolenie oraz na refleksję nad organizacją pracy i wyciąganie wniosków. Okazało się również, że młodzi pracownicy (średnia wieku poniżej trzydziestu lat) często mają trudności z rzetelnym spojrzeniem na problemy. Praktyka Lean pokazuje zresztą, że to wyzwanie nie dotyczy tylko młodych osób. Dostrzeganie, identyfikowanie i definiowanie problemów to konkretne umiejętności, których opanowanie wymaga szkolenia i treningu. Niezbędne jest także zapewnienie odpowiednich warunków oraz bezpieczeństwa psychologicznego, aby pracownicy chcieli zgłaszać problemy.
Szkolenia są tu kluczowe, ponieważ pomagają zmienić podejście pracowników. Na przykład w Bellamy zorganizowano warsztaty dotyczące identyfikowania marnotrawstwa i efektywnego rozwiązywania problemów. Dzięki temu pracownicy zaczęli aktywnie zgłaszać swoje obserwacje i propozycje usprawnień. W rezultacie firma odnotowała poprawę w zakresie jakości produkcji, skrócenie czasu realizacji zamówień oraz wzrost satysfakcji klientów.
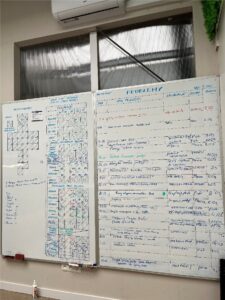
Nie sposób pominąć kosztów szkoleń i doradztwa. „My, przedsiębiorcy, mamy tendencję do tego, aby podejmowane inwestycje miały bardzo precyzyjnie określoną stopę zwrotu. W szkoleniach trudno jest ją dokładnie wyliczyć. Niektórzy, porównując wydatek na szkolenia z zakupem nowej maszyny, automatycznie wybierają zakup maszyny” – tłumaczy Jakub Suchocki. „Z własnej perspektywy zachęcam do inwestowania w szkolenia. Spojrzenie doświadczonego praktyka z zewnątrz procentuje”.
Rezultaty projektu wdrożeniowego
W wyniku wdrożenia praktyk Lean Management w firmie zaszły pozytywne zmiany:
-
- Poprawa jakości – firma zwraca większą uwagę na jakość mebli wydawanych przez każdą z fabryk współpracujących na zasadzie outsourcingu oraz własną. W przypadku mebli produkowanych we własnym zakładzie jakość każdego mebla jest kontrolowana przed pakowaniem. Meble wyprodukowane w innych zakładach podlegają kontrolom jakościowym w problematycznych obszarach charakterystycznych dla każdej fabryki, takich jak jakość lakierowania, kompletność akcesoriów i instrukcji oraz poprawność pakowania.
- Zmniejszenie zapasów i szybkie przezbrojenia – po wdrożeniu Lean zakład jest w stanie produkować w mniejszych partiach (produkcja 20 mebli w partii wobec wcześniejszych 50-100 mebli w partii). „Jesteśmy w stanie bardzo często robić przezbrojenia, począwszy od koloru płyty po rodzaj mebla, oraz bardzo szybko reagować na potrzeby klientów” – wyjaśnia Piotr Haduch, Kierownik Produkcji.
- Zmniejszenie liczby reklamacji – w wyniku wdrożenia Lean liczba reklamacji znacząco spadła. Mimo oczywistej poprawy firma nie spoczywa na laurach i wciąż traktuje ten aspekt jako obszar do dalszej poprawy.
- Poprawa produktywności – firma produkuje zdecydowanie więcej mebli niż wcześniej, a dostawy są realizowane systematycznie. Efektywność produkcji wzrosła rok do roku o ponad 30%. Wiadomo, że jest to też zasługa niskiej bazy, niemniej wzrost efektywności po wdrożeniu projektu lean dodatkowo przyśpieszył. Zaczęliśmy po prostu np. popełniać mniej błędów czy lepiej planować.
- Poprawa terminowości – wcześniej zdarzały się duże opóźnienia, co dobrze ilustruje poniższy wykres. W okresie przed kwietniem 2023 roku opóźnienia (niezrealizowane zamówienia) były znacznie większe. Jak widać, zamówień po terminie jest coraz mniej, co pozytywnie wpływa na opinie klientów.
-
- Wzrost zadowolenia klientów – jest widoczny, jeśli spojrzeć na opinie w Google. O ile w listopadzie 2023 roku średnia ocen wynosiła 3,8, o tyle aktualnie jest to 4,2.
Wnioski z wdrożenia Lean Management i współpracy z Lean Enterprise Institute Polska
Jakub Suchocki podkreśla, że kluczowe jest zbudowanie wśród pracowników potrzeby zmiany. „Zaczęliśmy wdrażać Lean dopiero po pół roku od uruchomienia fabryki całkiem świadomie, aby wcześniej pozwolić na kilka porażek i pewien bałagan, bo to rodzi potrzebę zmiany i chęć poznania metod, które pozwolą rozwiązać codzienne problemy” – wyjaśnia. Chęć zmiany w samych pracownikach powoduje ich większe zaangażowanie podczas szkoleń. Zmęczenie popełnianiem błędów i chęć ich uniknięcia w przyszłości były zaskoczeniem nawet dla właścicieli firmy.
Znaczenie profesjonalnego wsparcia
Kolejnym ważnym wnioskiem z wdrożenia Lean Management jest wartość współpracy z profesjonalną firmą doradczą. Właściciele firm często mają tendencję do brania na siebie zbyt wielu obowiązków i pełnienia zbyt wielu funkcji w organizacji. Lean Management to złożony proces wymagający długotrwałego wdrożenia. Profesjonalna firma doradcza i doświadczeni trenerzy mają odpowiednią wiedzę i sprawdzone techniki, co stanowi gwarancję udanej transformacji. Eliminuje to również nastawienie pracowników, które można by opisać jako: „szef się czegoś naoglądał i naczytał, więc trzeba ten jego pomysł po prostu przeczekać”. Dzięki wsparciu konsultanta pracownicy sami wypracowują metody, organizują swoje stanowiska pracy i czują odpowiedzialność za swoje działania.
Korzyści z wizyt referencyjnych i szkoleń otwartych
Współpraca z firmą doradczą umożliwiła także wykorzystanie dodatkowych możliwości, takich jak wizyty referencyjne i szkolenia otwarte w innych zakładach. Pracownicy wracają z tych wizyt z nowymi pomysłami i energią, co jest niezbędne, aby transformacja nie traciła swojej siły, a ludzie pozostawali zaangażowani. „Konsultant LEI Polska towarzyszy nam od samego początku i rozumie, jakie potrzeby mamy w danym momencie” – dodaje Jakub Suchocki. Konsultant LEI Polska jest zawsze dostępny i firma może liczyć na jego wiedzę i kontakty w każdej istotnej chwili.
Profesjonalizacja i wzrost produktywności
Przed rozpoczęciem współpracy z Lean Enterprise Institute Polska zakład charakteryzował się chaosem i niską wydajnością. Obecnie firma może pochwalić się profesjonalnym systemem zarządzania, uporządkowaną produkcją, rozwojem pracowników oraz wysokiej klasy kadrą kierowniczą. Od stycznia do października 2023 roku nastąpił wzrost produktywności pracownika o 70%. Dziś firma jest zdecydowanie zorientowana na klienta, opóźnienia zostały wyeliminowane, a liczba reklamacji znacząco zmniejszona.
Dla każdej firmy, która rozważa wdrożenie Lean Management, historia Bellamy może stanowić inspirację. Kluczem do sukcesu jest otwartość na zmiany, zaangażowanie pracowników oraz wsparcie profesjonalnych doradców. Dzięki tym elementom procesy produkcyjne mogą zostać zoptymalizowane, a firma może osiągnąć znaczący wzrost efektywności i jakości, co przekłada się na zadowolenie klientów i sukces na rynku.
Bądź na bieżąco i zyskaj darmową wiedzę w naszym newsletterze!
Nowości ze świata Lean, wydarzenia, oferty specjalne – dołącz, aby być na bieżąco!