Lean – wsparcie zarządzania strategicznego w Bella Sp. z o.o.
WSTĘP
TZMO S.A., właściciel firmy Bella sp. z o.o., to firma o zintegrowanej działalności produkcyjnej, serwisowej a także handlowej. Główne obszary to produkty i usługi medyczne, produkty higieniczne oraz produkty kosmetyczne. TZMO to organizacja globalna, charakteryzująca się wysoką wymianą doświadczeń z poszczególnych rynków a także obszarów funkcjonowania takich jak badania, produkcja, usługi. Działalność firmy realizowana jest przez blisko 7600 pracowników na całym świecie poprzez zorganizowaną strukturę firm i oddziałów w 56 krajach. Główne wartości firmy TZMO wyraża misja:
„Chcemy dostarczać naszym Klientom produkty najwyższej jakości, dzięki którym żyje się im łatwiej, wygodniej i bezpieczniej. Odpowiadamy nie tylko na ich aktualne potrzeby, ale także przewidujemy, czego będą potrzebowali w przyszłości i staramy się zapewnić im to już dziś”.
Bella sp. z o.o. to pierwsza firma o profilu produkcyjnym wydzielona w 1996 roku ze struktur TZMO S.A. Zatrudnia blisko 550 osób i jest odpowiedzialna za produkcję wyrobów higieny kobiecej oraz produktów inkontynentnych.
CELE TRANSFORMACJI
W 2011 roku, po 15 latach od powstania fabryki szukano odpowiedzi na pytanie czy dynamiczny rozwój Grupy TZMO skupiający się na inwestycjach zapewnił równie dynamiczny postęp w obszarach organizacyjnych, związanych z bezpieczeństwem, komfortem pracy i efektywnością procesów. W trakcie intensywnego wzrostu firmy nie zawsze udawało się zapewnić pełne wsparcie pracownikom liniowym, co doprowadziło do obniżenia morale zespołu a w konsekwencji spadku efektywności fabryki. Decyzja czy postawić nową fabrykę czy też podnieść efektywność istniejącej była genezą rozpoczęcia transformacji. Zbudowanie nowej fabryki nie było jednak „lekarstwem” na problemy, z którymi borykała się firma a jedynie ucieczką od nich. Postanowiono zmierzyć się z istniejącymi problemami w obecnej lokalizacji i dopiero wtedy relokować fabrykę.
W następstwie tej decyzji wyznaczono kluczowe cele dla całej organizacji:
- poprawienie poziomu bezpieczeństwa pracy,
- podniesienie morale pracowników,
- zwiększenie efektywności maszyn,
- doskonalenie jakości produktów,
- w konsekwencji eliminacja marnotrawstwa i poprawa wyników finansowych firmy.
Za najlepszą metodę planowanej transformacji uznano Lean Management (LM). Wybór formy wdrożenia i partnerów wspierających trwał blisko dwa lata.
STRUKTURA ORAZ NARZĘDZIA LEAN MANAGEMENT
W 2012 roku rozpoczęto realizację planu zmierzającego do realizacji celów nakreślonych po analizie stanu bieżącego. Początkiem był wybór osób kluczowych z obszarów operacyjnych firmy, entuzjastów ciągłego doskonalenia. Drugim krokiem było ich szkolenie realizowane wspólnie z LEI Polska z zakresu kultury oraz technik i narzędzi Lean Management. Szkolenia te obejmowały m.in.: symulację LM, szczupły system zarządzania, Hoshin Kanri, raport A3, 5S, SMED, TPM, narzędzia rozwiązywania problemów, standaryzacja pracy, Training Whitin Industry, planowanie przepływów.
Pierwszym elementem wdrożenia był audyt fabryki, dotyczący potencjału Lean w Bella sp. z o.o. Wynik potwierdził potrzebę wprowadzenia zmian. Kluczowa była opinia naszych Pracowników, prezentowana w trakcie audytu, wyrażona hasłem: „NIE MAMY ŻADNYCH PROBLEMÓW”.
Do największych ujawnionych audytem problemów należały: nieskuteczny system planowania produkcji, akord jako główny składnik wynagradzania, nieprzejrzysty layout fabryki, niejasny podział zakresu ról i obowiązków, brak kultury delegowania uprawnień, brak FIFO, standardy skupione wyłącznie na jakości produktów, brak poczucia właścicielstwa, brak jasnych celów na poszczególnych szczeblach organizacji – przekładających się na wyniki firmy.
Hasłem zmian rozpoczętych w 2012 roku była poprawa bezpieczeństwa pracy. Celem stała się zatem relokacja praktycznie wszystkich jednostek produkcyjnych oraz wdrażanie w nowo organizowanych obszarach metody 5S. W celu dotarcia do szerokiej grupy Pracowników przygotowano trenerów wewnętrznych – brygadzistów, którzy przy wsparciu konsultantów zewnętrznych szkolili pracowników zmianowych. Największym problemem było przełamanie barier komunikacyjnych istniejących pomiędzy zarządzającymi a pracownikami oraz przyjęcie przez brygadzistów odpowiedzialności za podlegających im pracowników, procesy i przestrzeń. Z uwagi na wielkość fabryki wdrożenie 5S zrealizowano na obszarze pilotażowym. Po okresie wdrożenia rozpoczęto audyty jednak ich wyniki nie były w żaden sposób wizualizowane, co później okazało się błędnym założeniem. Powodem takiego podejścia było „przyjazne” rozpoczęcie zmian związanych z Lean. Największe problemy polegały na tym, iż 5S wdrażane było „z góry” tj. przez brygadzistów i koordynatora Lean i po pewnym czasie spowodowało kryzys i konieczność wprowadzenia korekty. Tym razem wdrożenie przeprowadzono z pracownikami, czyli właścicielami poszczególnych odcinków pracy.
Dużym kolejnym problemem dla grupy wdrożeniowej była sytuacja, w której entuzjaści „zderzali się” z pozostałymi pracownikami, kierującymi działami wspierającymi, kompletnie wówczas nierozumiejącymi, co się dzieje w ich firmie. Kulminacyjnym punktem była próba prezentacji narzędzia 5S i omówienia filozofii Lean realizowana przez entuzjastów dla osób do tej pory nieuczestniczących w szkoleniach. Był to moment, w którym zrozumieliśmy, iż niezbędne są warsztaty szkoleniowe Symulacja Lean Manufacturing dla wszystkich kierowników (Rys. 1) oraz włączenie ich do procesu zmian w organizacji.
W tym celu jesienią 2012 roku przeprowadzony został pierwszy warsztat Hoshin Kanri, który pomimo burzliwego przebiegu pozwolił na stworzenie wspólnego rocznego planu działań dla całej organizacji. W marcu 2013 roku przeprowadzony został pierwszy miesięczny przegląd Systemu Produkcyjnego Bella.
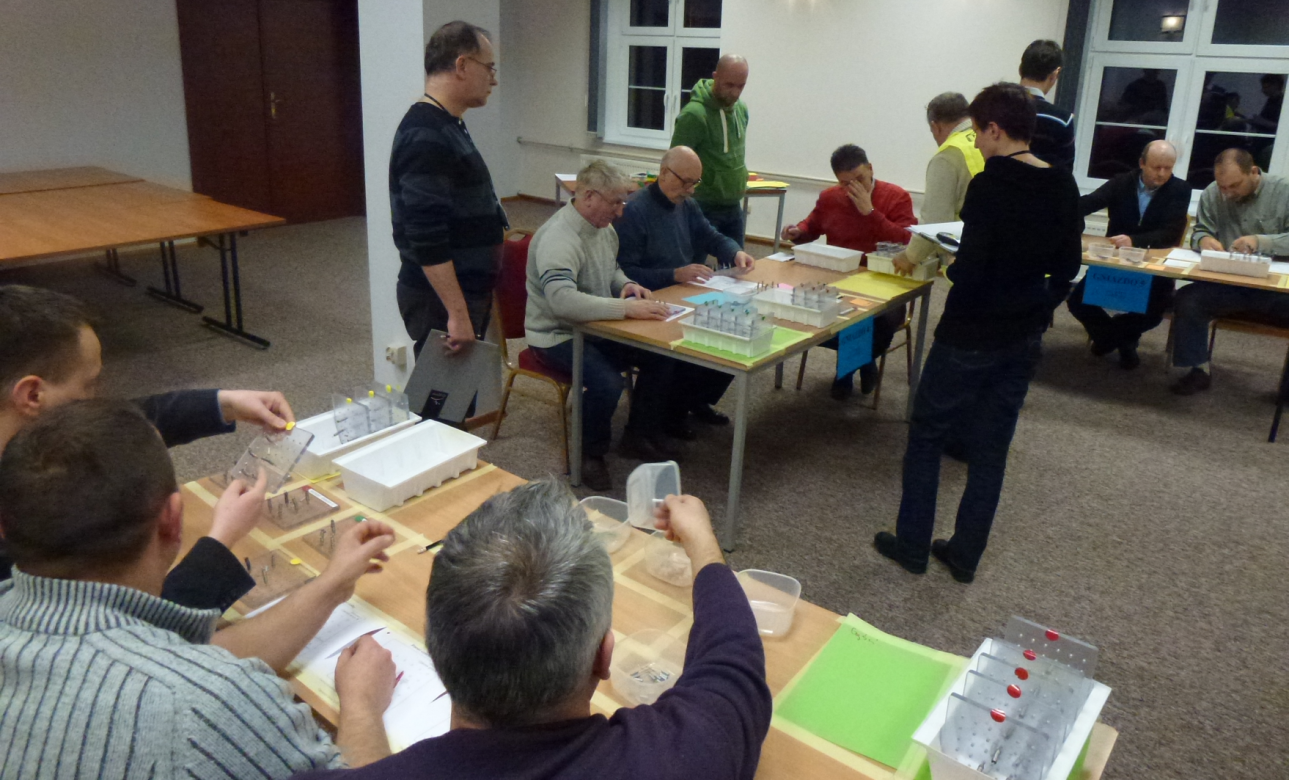
Rysunek 1. Warsztaty Szkoleniowe Symulacja Lean Manufacturing dla osób kierujących pracownikami przeprowadzona przez LEI Polska w styczniu 2013
SPB – System Produkcyjny Bella to odzwierciedlenie mechanizmów zarządczych funkcjonowania całej organizacji w podziale na cztery filary oraz cztery poziomy. Celem SPB jest wspieranie Pracowników w realizacji powierzanych im zadań oraz rozwiązywaniu napotykanych przy tym problemów. W trakcie warsztatu Hoshin Kanri narodziła się nazwa poszczególnych filarów, która pasowała do naszej branży a mianowicie KLEJ – podstawowy surowiec używany podczas produkcji wyrobów higienicznych. System produkcyjny Bella to cztery elementy i rozszerzenie słowa KLEJ, a mianowicie K-Koszty, L-Ludzie, E-Efektywność, J-Jakość.
Sterowanie wskaźnikami SPB – zmiany w zakresie otoczenia, oczekiwań klientów, właścicieli, zarządu oraz pracowników powodują, że co pół roku organizacja przeprowadza weryfikację poszczególnych celów na warsztatach Hoshin Kanri. Nie oznacza to jednak, że całkowicie zmieniane są główne kierunki działania a jedynie część zadań i metod.
SPB Poziom 1 (spotkania raz na miesiąc) – spotkania zarządu spółki z kierownikami wszystkich działów dotyczące przeglądu realizacji celów. Każda z kategorii KLEJ oraz każde z zadań w konsekwencji mierników ma Opiekuna, który prezentuje wynik miesiąca. Jednocześnie omawiane są działania korygujące, które zostały podjęte, aby określony cel został zrealizowany.
SPB Poziom 2 (spotkania raz na tydzień) – spotkania kierowników działów z brygadzistami, mistrzami, specjalistami. Podczas tych spotkań omawiane są statuty poszczególnych wskaźników monitorujących realizację zadań a także działania zmierzające do ich poprawy w przypadku odchyleń. Przykładowe wskaźniki to:
- poziom i rotacja zapasu,
- poziom odpadu na poszczególnych liniach,
- realizacja szkoleń,
- poziom absencji,
- wyniki audytów bezpieczeństwa,
- poziom realizacji planu produkcji,
- wyniki czasów przezbrojeń,
- ilość reklamacji wewnętrznych.
Przykładowe KPI są jednak różne dla poszczególnych obszarów fabryki, inaczej wyglądają w obszarze Logistyki, Techniki, Jakości czy też Produkcji.
SPB Poziom 3 (spotkania raz na 24 h) – spotkania między kierownikami działów oraz specjalistów z zakresu BHP. Wystandaryzowana agenda spotkania obejmuje 6 punktów: bezpieczeństwo pracy, realizacja planu produkcji, problemy jakościowe, problemy logistyczne, problemy techniczne, inne – np. goście, zarządzenie formalne, audyty. Celem jest prezentacja problemów nierozwiązanych a zgłoszonych przez poszczególne zmiany z minionej doby a następnie przyjęcie planu dalszych działań. Podsumowaniem spotkania Poziomu 3 jest omówienie problemów i podjętych działań w obecności zarządu spółki.
SPB Poziom 4 – spotkania między brygadzistami i mistrzami poszczególnych zmian produkcyjnych trzy razy w ciągu doby. Przebieg spotkania jest tożsamy z agendą Poziomu 3. Celem spotkań jest rozwiązanie problemów występujących na danej zmianie. W przypadku braku możliwości ich rozwiązania następuje eskalacja do Poziomu 3. Najczęściej używane narzędzia: 5WHY, Diagram Ishikawy.
SMED
Podczas prac związanych z relokacją maszyn jednocześnie ograniczono ich liczbę na skutek przesunięcia do innych spółek TZMO. Sytuacja ograniczenia ilości zasobów spowodowała, że istotne z punktu widzenia obsługi Klienta czasy przezbrojeń oraz efektywność stały się kluczowymi parametrami procesu planowania. W celu podniesienia efektywności posiadanych zasobów przygotowano pierwszy warsztat SMED (Rys. 2), na obszarze testowym, którego efekt zaskoczył wszystkich. Była to pierwsza sytuacja, w której proces zmiany formatu na maszynie pakującej zrealizowano w czasie niecałych 10 minut – czyli o 85% szybciej niż dotychczas. Efektem istotnym było wprowadzenie pierwszej wystandaryzowanej Instrukcji Przezbrojenia.
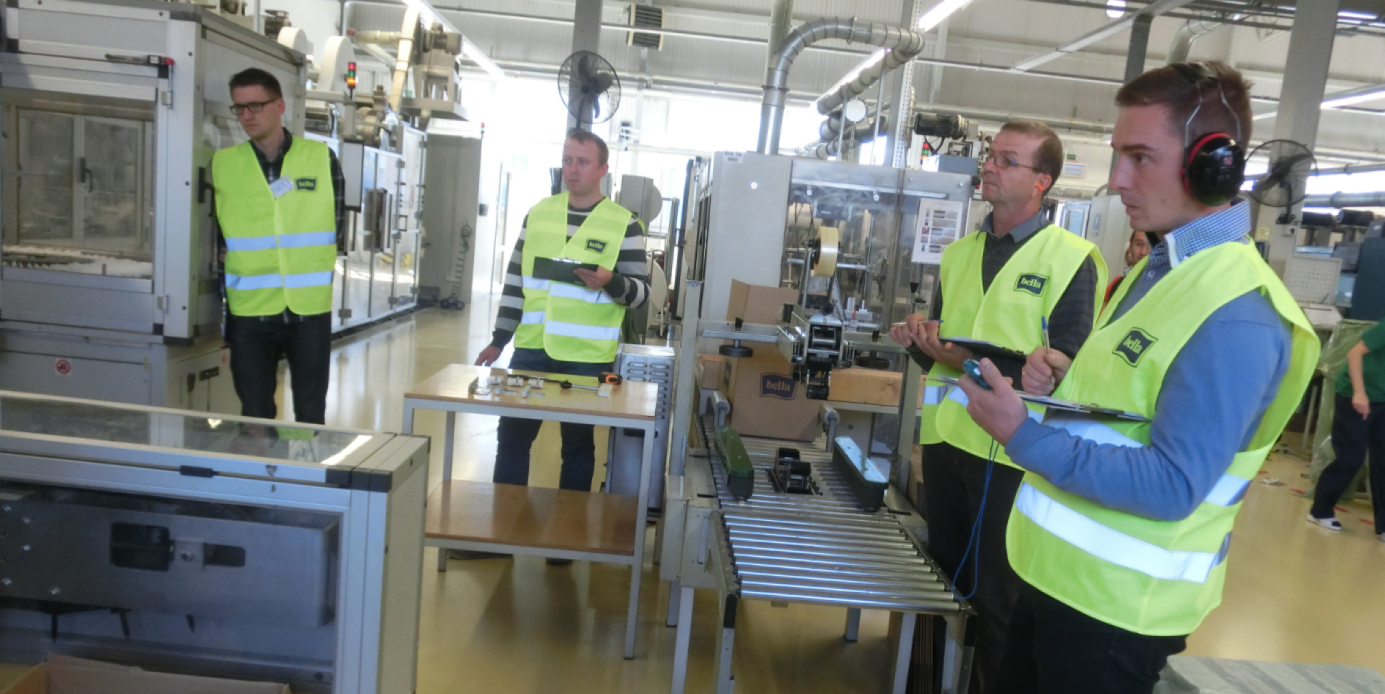
Rysunek 2. Zdjęcie z warsztatów SMED
Pomimo osiągniętego sukcesu niemożliwe było konsekwentne stosowanie wspomnianej instrukcji, w związku z:
- licznymi usterkami na maszynie,
- nieergonomicznymi osłonami,
- planowaniem produkcji opartym o prognozę i telefony,
- systemem wynagradzania opartym o akord.
Zrozumieliśmy, że pomimo sukcesu SMED dotarliśmy do głębszych problemów organizacji.
W odpowiedzi na wymienione problemy z początkiem 2014 roku zmieniono system wynagradzania, tak, iż za wyniki efektywności fabryki odpowiadają wszyscy pracownicy nie tylko pracownicy produkcji.
Jednocześnie w tym samym okresie przyjęto decyzje o zmianie sposobu planowania i zbudowania własnego modelu planowania opartego o system ssący.
Standaryzacja
Firma posiadała dobre standardy jakościowe, które koncentrowały się wyłącznie na produktach. Podjęto decyzje o ujednoliceniu rozproszonej formy standardów pracy. Początkowo w organizacji wyznaczono jedną osobę, której zadaniem było ustandaryzowanie procedur i instrukcji. Oczywiście skutek był taki, iż nie udało się tego zrealizować.
Rozwiązaniem okazało się desygnowanie do tego celu wielu osób w każdym z obszarów. Dodatkowo dzięki koordynacji służb BHP bądź koordynatora Lean oraz specjalisty ds. zapewnienia jakości (ISO) uzyskaliśmy spójny dla całej organizacji efekt. Autoryzacja wspomnianych wyżej specjalistów dla każdej z przygotowywanych instrukcji była oparta o jeden standard formatki. Warto zaznaczyć, że zdecydowaliśmy się na stosowanie technik i narzędzi Lean nie wykluczając dotychczasowego stosowania norm np. ISO a jedynie modyfikując metody chociażby w zakresie rozwiązywania problemów np. diagram Ishikawy (Rys. 3).
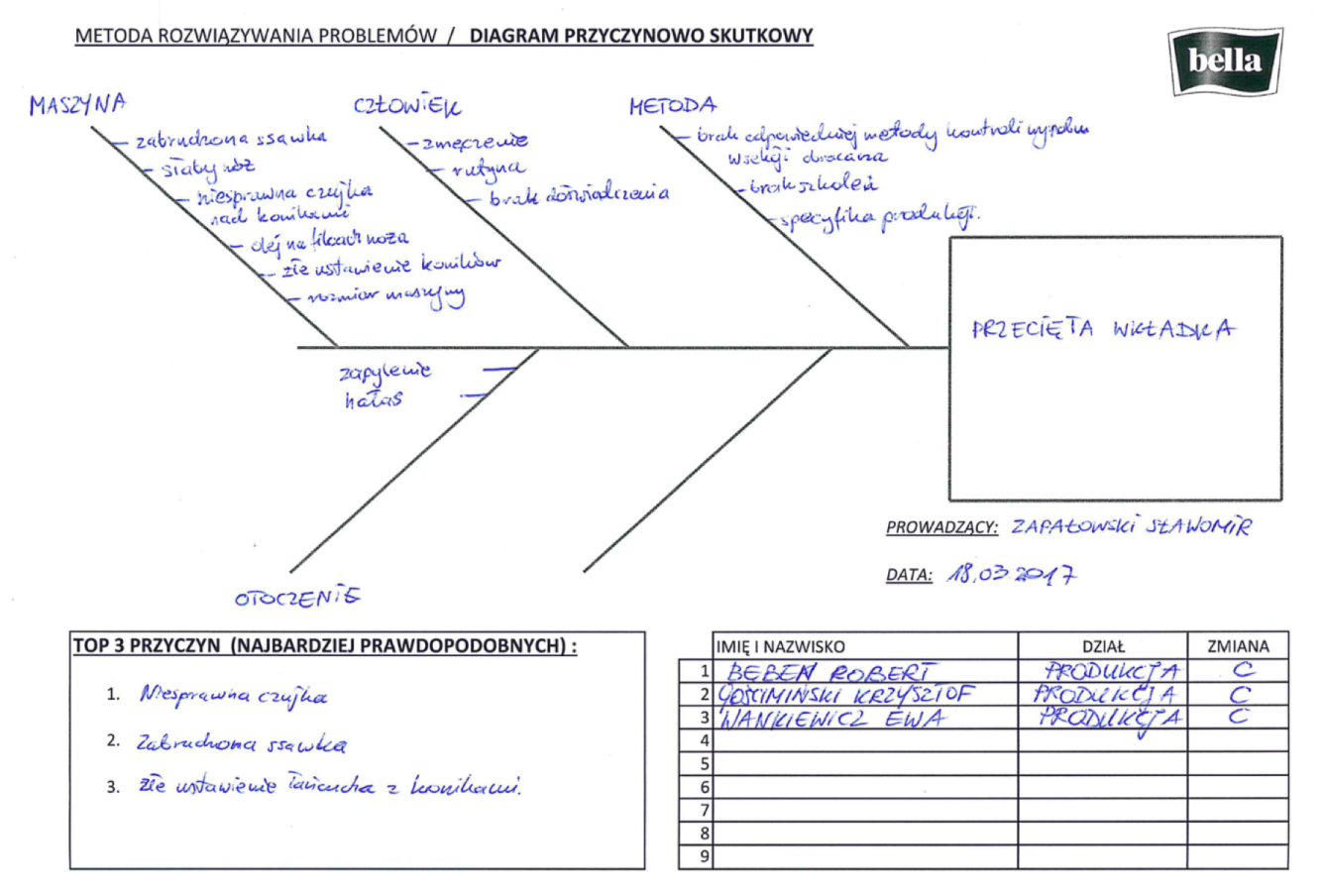
Rysunek 3. Fragment protokołu Polecenie Działań Korygujących (ISO), Diagram Ishikawy
System Ssący
W 2014 roku rozpoczęto wdrożenie na obszarze testowym poprzedzone szkoleniem grupy pracowników z działów produkcji i logistyki. Wybrany obszar ograniczał się początkowo do jednej maszyny a później jednej hali produkcyjnej. Problemem zasadniczym podczas wdrożenia okazało się administrowanie systemem. Początkowo był on zarządzany, przez koordynatora Lean. Po okresie blisko dwóch lat konieczne stało się wyznaczenie administratorów systemu oraz poprawa komunikacji z pionem planowania produkcji.
Tradycyjnie, jak w przypadku każdego narzędzia Lean, tu też odkryliśmy głębsze problemy tj.:
- konieczność zmian w strukturze organizacyjnej firmy i przełączenie wszystkich magazynów fabryki do pionu logistyki (między innymi z działu technicznego i produkcji),
- zakończenie relokacji maszyn produkcyjnych,
- zmiana sposobu planowania produkcji.
Rozwiązując przedstawione wyżej problemy udało nam się uporać z niepożądanymi efektami wdrożenia systemu ssącego, dzięki czemu doskonalimy oraz wdrażamy system ssący w pozostałych obszarach fabryki.
TPM
Schemat pilotażowego wdrożenia TPM w 2016 roku był realizowany w całej fabryce w dwóch formach. Pierwsza – pod oficjalnym hasłem TPM w peryferyjnej lokalizacji fabryki oraz druga pod nazwą „konserwacje bieżące” w głównej lokalizacji. Wdrożenia te zostały zrealizowane z udziałem operatorów i techników z maksymalnym nastawieniem na brak konieczności wykonywania przez nich czynności elektronicznej rejestracji problemów. Zadania te desygnowano do brygadzistów. Efektem prac dla obszaru pilotażowego, na którym oficjalnie używano nazwy TPM, było usunięcie ponad 40 usterek, podniesienie dostępności maszyn o 45% a także obniżenie odpadu o 35%. Podczas pilotażowych wdrożeń TPM nie napotkano większych utrudnień, ponieważ bazując na wcześniejszych doświadczeniach przygotowano zbilansowany plan pracy maszyn, właściwie oszacowano dostępne zasoby ludzkie oraz zrealizowano zadanie wspólnie z pracownikami liniowymi (Rys. 4).
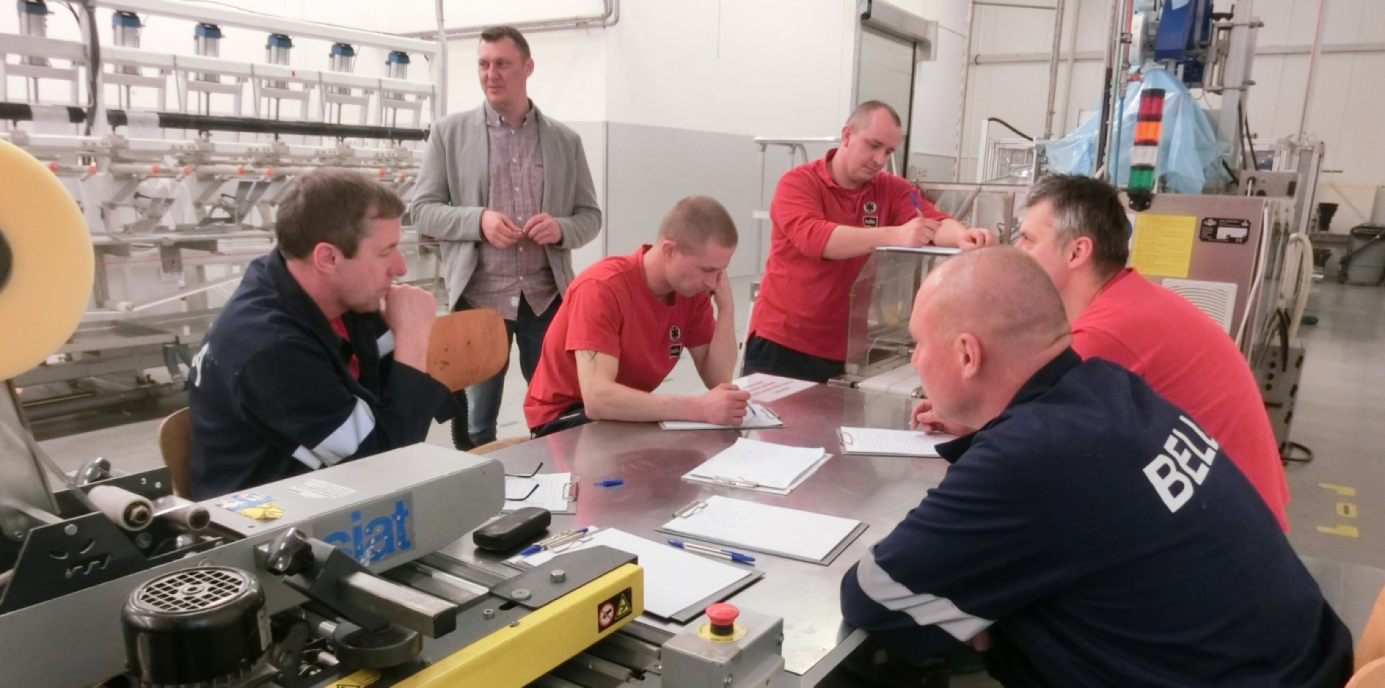
Rysunek 4. 2016 – Zdjęcie z warsztatu TPM
System TPM jest obecnie dalej wdrażany i doskonalony w głównej lokalizacji firmy.
ROZWÓJ POTENCJAŁU PRACOWNIKÓW
Jak zaangażować Pracowników mających wieloletnie doświadczenie nie zawsze dobre? Jak rozwinąć pracowników kierujących zespołami? Jak i gdzie zacząć?
W celu wyrównania relacji między rozwojem fabryki a rozwojem potencjału pracowników rozpoczęto pracę z osobami kierującymi zespołami. Osoby kierujące pracownikami na najwyższym szczeblu zarządzania podpisały Deklarację Bezpieczeństwa a następnie przez przykład dla średniego szczebla zaangażowały się w:
- poprawę bezpieczeństwa i warunków pracy,
- budowanie poczucie właścicielstwa,
- kształtowanie wzorców przywództwa.
Elementem pierwszym na liście celów przyjętych w 2011 roku było Bezpieczeństwo – „drzwi do wszystkiego”. Początkiem zmian było wprowadzenie audytów bezpieczeństwa z udziałem kierownictwa firmy oraz kierowników działów w cyklu miesięcznym. Celem audytów było wykrycie zagrożeń i ich eliminacja a w konsekwencji zbudowanie kultury bezpiecznej pracy. Służba BHP dzięki wsparciu zarządu ponownie uświadomiła wszystkich pracowników o właściwych priorytetach pracy i że to bezpieczeństwo jest bazą budowania stabilności procesów. Przez wiele lat fabryka bardzo dynamicznie się rozwijała a jej intensywny rozwój powodował, że kluczowe stało się zaspokajanie potrzeby Klientów, wyłącznie zewnętrznych, co oczywiście bardzo korzystnie wpływało na wyniki finansowe spółki. Mniej korzystnie wyniki te oddziaływały na klientów wewnętrznych – Pracowników, którzy mieli, co prawda udział w przychodach z osiąganych zysków, ale określonym kosztem m.in. wypadkowości.
Pomimo dużego zaangażowania zarządu i służb BHP w nowy plan działania nie odnotowano spadku a wręcz wzrost ilości zdarzeń i wypadków. Dopiero po dwóch latach nastąpił pozytywny przełom. Pracownicy stopniowo zaczęli dostrzegać i wierzyć w czystość intencji podejmowanych działań i rezygnować z niebezpiecznych rutynowych zachowań. 2016 rok zakończono z rekordowym wynikiem zaledwie jednego zdarzenia wypadkowego.
Rozwinięciem miesięcznych audytów bezpieczeństwa stały się w późniejszym okresie audyty cotygodniowe, dobowe oraz zmianowe realizowane jako wsparcie dla całego systemu bezpiecznej pracy. Audyty te realizowane są z udziałem pracowników, kierujących podległymi im obszarami.
Dzisiejsza kultura bezpiecznej pracy w Bella jest ciągle rozwijana a jej kluczową wartością jest szeroki zespół pracowników formalnie zaangażowanych w jej doskonalenie – blisko 20% wszystkich zatrudnionych. Osoby te, realizują dodatkowe zadania z zakresu poprawy warunków pracy i posiadają podwójną zależność służbową tj. w ramach pionu podlegają brygadziście lub mistrzowi oraz w ramach struktury matrycowej podlegają specjalistom z zakresu bhp, ppoż.
Na przestrzeni kilku lat przeprowadzono kilkukrotnie modyfikację struktury organizacyjnej firmy. Modyfikacje struktury organizacyjnej są konsekwencją wprowadzanych w firmie zmian:
- przesunięcia czynności pomocniczych z Pionu Produkcji do pozostałych Pionów Wspierających, np. sprzedaż wyrobu gotowego,
- przesunięcia części specjalistów z Pionu Produkcji do Pionów Wspierających, np. operatorzy wózków widłowych, mechanicy,
- przekazania władzy od nieformalnych liderów do liderów formalnych,
- dopasowania do zmian w layoucie fabryki,
- dopasowania do zmiany systemu wynagradzania,
- wzrostu odpowiedzialności na niższych szczeblach organizacyjnych.
W trakcie opisanych zmian organizacyjnych przygotowano nowy podział ról, zakresów obowiązków dla osób kierujących pracownikami. Konieczna była weryfikacja ich kompetencji a także umiejętności zarządczych. Przygotowano odpowiednie badania oraz program rozwoju tej grupy pracowników. Dla nich opracowane zostały odpowiednie sesje z najwyższym kierownictwem firmy, tak aby właściwe rozumieli cele biznesowe firmy i wyzwania przed jakimi staje fabryka. Proces ten jest istotny w kontekście dalszych planów związanych z wdrażaniem systemu sugestii w 2018 roku.
KORZYŚCI Z WDROŻENIA LEAN
W wyniku wprowadzenia zmian związanych z Lean Management w fabryce odnotowano wiele korzyści, które nie sposób wszystkie wymienić. Niewątpliwie do najważniejszych należą:
- podniesienie morale i zaangażowania pracowników – „mamy problemy, które rozwiązujemy”,
- poprawienie poziomu bezpieczeństwa pracy,
- poprawa poziomu obsługi Klientów – „brak telefonów z reklamacjami przez cały 2016 rok”,
- zwiększenie efektywności maszyn,
- poprawa efektywności i wyników finansowych spółki (eliminacja aktywów nieoperacyjnych).
Autorzy:
Michał Gawroński – Członek Zarządu, Bella Sp. z o.o.
Dariusz Kostkowski – Prezes Zarządu, Bella Sp. z o.o.
Artykuł stanowi przedruk publikacji zamieszczonej w materiałach konferencyjnych XVII Konferencji Lean Management, która odbyła się we Wrocławiu w dniach 6-8 czerwca 2017 roku. Konferencja, która organizowana jest corocznie przez Lean Enterprise Institute Polska, przeznaczona jest dla sektorów produkcyjnego i usługowego. Zapraszamy do odwiedzenia obszernego serwisu internetowego poświęconego Konferencji pod adresem www.leankonf.pl.
Artykuł został opublikowany dzięki uprzejmości i za zgodą firmy Bella Sp. z o.o.