Od Lean Manufacturing do Lean Enterprise na przykładzie historii, która zdarzyła się naprawdę
Historia wprowadzenia zmian na bazie Lean Manufacturing i Lean Thinking
Black Point S.A. to producent, dystrybutor i właściciel marki materiałów eksploatacyjnych do urządzeń drukujących. Spółka jest podmiotem wiodącym w działającej na rynkach międzynarodowych Grupie Black Point, w skład której wchodzą dwie spółki zależne: Eco Service, ogólnoświatowy broker pustych kartridży i niemiecka spółka TBG, która wspiera działania Eco Service na rynku zachodnioeuropejskim.
Black Point S.A. istnieje od 22 lat. Zatrudnienie w chwili obecnej wynosi około 160 osób, a obroty Grupy Black Point to około 75mln zł rocznie. Od początku istnienia spółka odnotowuje corocznie zyski. W roku 2009 zysk brutto w Grupie Black Point przekroczył 7mln zł.
Spółka specjalizuje się w produkcji i dystrybucji produktów o wysokiej jakości, wydajności i niezawodności, które sprzedaje do marketów, sklepów specjalistycznych i sieci wyspecjalizowanych w obsłudze biur działających w Europie Środkowo-Wschodniej. W Polsce Black Point jest jednym z liderów w branży i jedną z najbardziej rozpoznawalnych marek wśród alternatywnych materiałów eksploatacyjnych do drukarek.
Spółka oferuje ponad 300 rodzajów produktów marki Black Point m.in. tonery do drukarek laserowych, atramenty do drukarek atramentowych i taśmy do drukarek igłowych, a także papiery fotograficzne do wydruków fotografii. Przy rozwoju swojej oferty Black Point stosuje restrykcyjne procedury testowe oparte o normy ISO. Spółka współpracuje także z renomowanymi ośrodkami badawczymi na świecie, m.in. Rochester Institute of Technology, Politechniką Wrocławską oraz Instytutem Innovationstechnik.
Działając od 22 lat na rynku materiałów barwiących obserwujemy wzrost i coraz większe zróżnicowanie wymagań klientów zarówno co do produktów, jak i co do jakości obsługi. Chcąc realizować nowe wymagania, doskonalić swoje działania i dążąc do ciągłego rozwoju firma Black Point od początku poszukiwała nowych rozwiązań. Nasze starania na drodze do zwiększania efektywności działań obrazuje rys. nr 1.
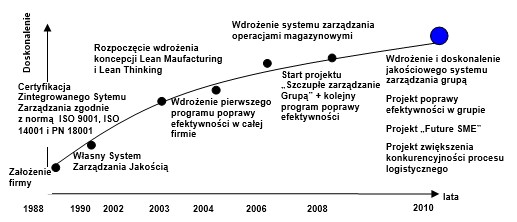
Rys. 1. Proces doskonalenia efektywności firmy
Rozpoczęliśmy od wprowadzania własnych, wewnętrznych zasad związanych z zarządzaniem jakością (produktów oraz realizowanych procesów). Wprowadzaliśmy procedury systematyzujące nasze działania, zaczęliśmy stosować standaryzowane metody testowania tonerów laserowych zgodne z normami STMC (Standardized Test Methods Committee) oraz nowe metody badania jakości innych naszych produktów. Uwieńczeniem wysiłków nad wprowadzeniem kompleksowego Systemu Zarządzania Jakością było uzyskanie w lutym 2002 roku Certyfikatu potwierdzającego jego zgodność z normą ISO 9001:2000.
Od stycznia 2003 roku rozpoczęliśmy prace nad wdrożeniem koncepcji Lean Manufacturing przede wszystkim w procesie produkcyjno-logistycznym [mapowanie strumieni wartości], a w drugiej połowie 2004r. rozpoczęliśmy etap doskonalenia wdrożonego systemu, w ramach którego wdrożyliśmy system ssący, standaryzację poszczególnych etapów wytwarzania z wykorzystaniem technik 5S oraz pracowaliśmy również nad wdrożeniem przepływu ciągłego zgodnie z celami map stanu przyszłego.
Dodatkowo Zarząd Firmy uruchomił szereg innych działań, zmierzających do poprawy efektywności firmy:
- na przełomie 2003/2004r. dokonano outsourcing’u procesu księgowego;
- w roku 2006 wdrożono system zarządzania operacjami magazynowymi, którego kluczowym celem była automatyzacja i usprawnienie działań realizowanych w magazynie Black Point.
W roku 2007 w ramach przeglądu strategicznego zdefiniowaliśmy, że jednym z kluczowych zagrożeń dla spółki jest dostępność surowców. Uznaliśmy wówczas za konieczne otwarcie się na współpracę z innymi producentami europejskimi co zaskutkowało uruchomieniem projektu Strategiczne Alianse Produkcyjne i w rezultacie dywersyfikacją produkcji naszych wyrobów z zachowaniem poziomu jakościowego, poprawą dostępności produktów jak również poprawą rentowności wytwarzania wyrobów w firmie Black Point.
W roku 2008 rozpoczęliśmy projekt „Szczupłego Zarządzania Grupą” polegający przede wszystkim na integracji wszystkich procesów zachodzących w spółkach Grupy z wyjątkiem sprzedaży. Aktualnie działamy w jednym magazynie, z jednym biurem rachunkowym i spójnym procesem zarządzania płynnością w grupie oraz wspólną logistyką zapasów i obsługą transportową.
W połowie 2008r. podczas kolejnego przeglądu strategicznego Zarząd opracował kolejny program efektywnościowy, którego wdrożenie okazało się sukcesem rentownościowym w 2009r., podwojeniem zysku. Podstawowym założeniem tego programu była likwidacja marnotrawstwa w wymiarze organizacyjnym od RN po wszystkie procesy w firmie, uzyskany efekt to 0,6mln zł oszczędności oraz udało się wprowadzić system zarządzaniami wydatkami w celu zapobiegania zbędnym wydatkom.
W roku 2010 realizujemy kilka projektów optymalizujących nasze działania:
- Projekt wdrożenia jakościowego systemu zarządzania grupą, który rozpoczął się w 2009r. mapowaniem strumieni wartości i układu procesowego w grupie oraz odświeżeniem standaryzacji działań;
- Kolejny program poprawy efektywności organizacji i działań w Grupie;
- Projekt zwiększenia przewagi konkurencyjnej w obszarze logistycznym poprzez drugi etap automatyzacji działań realizowanych w magazynie szczególnie operacji realizowanych w ramach spółki Eco Service jak również poprzez uruchamianie centrów logistycznych zewnętrznych i wewnętrznych aby zoptymalizować koszty transportu zagranicznego i uzyskać lepszy dostęp Grupy do klientów i dostawców z rynków dalekowschodnich;
- Projekt Future SME – dalsze doskonalenie efektywności produkcji.
Lean Manufacturing – Doskonalenie systemu ssącego i przepływu ciągłego
Na przestrzeni wielu lat firma Black Point przeszła istotną transformację. Poprzez zastosowanie narzędzi Lean produkcja stał się bardziej efektywna. Wszystkie podjęte działania wpisują się swoją ideą w filozofię i praktyki Lean Manufacturing, dając szansę na bardzie efektywne zarządzanie procesami produkcyjnymi i związanymi z nimi procesami wspierającymi.
Efekty tych działań widoczne są w postaci wciąż poprawiających się współczynników efektywnościowych fabryki oraz całego przedsiębiorstwa. A to za sprawą zoptymalizowanych zapasów surowców oraz wyrobów gotowych na stanach magazynowych, krótszych czasów planowania i realizowania zleceń produkcyjnych, mniejszych zapasów surowca oraz półproduktów w toku produkcyjnym.
Do najistotniejszych korzyści wdrażania Lean Manufacturing, z punktu widzenia celu funkcjonowania przedsiębiorstwa, należą:
- Możliwość dostarczenia klientom produktu w określonej ilości i na czas;
- Poprawa jakości produktów;
- Wzrost produktywności;
- Redukcja kosztów;
- Redukcja zapasów;
- Ograniczenie wykorzystywanej przestrzeni.
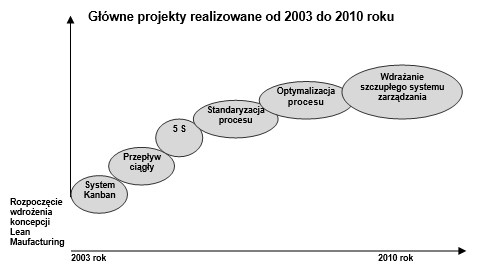
Rys. 2. Kamienie milowe – doskonalenie systemu ssącego i przepływu ciągłego
Od 2007 możemy obserwować, jaki wpływ miały wprowadzane zmiany na produktywność i koszt jednostkowy – kluczowe kryteria sukcesu firmy Black Point. Produktywność ogólna wszystkich wyrobów ma tendencję wzrostową, a koszt jednostkowy tendencję spadkową. Jest to dla nas dowód efektywności działań doskonalących.,
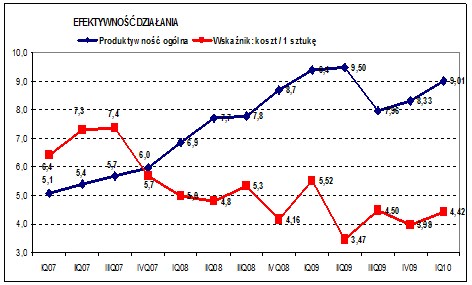
Rys.3. Poprawa produktywności i redukcja kosztów produkcji w latach 2007 – 2010
Wdrażanie koncepcji Lean w obszarze produkcji zaczęło się od 2003 roku i kolejne narzędzia i metody są wdrażane aż do dzisiaj. Program reorganizacji produkcji podzielono na kilka etapów.
I ETAP
LEAN MANUFACTURING – IDEA ORAZ WDROŻENIE I ETAPU, W OKRESIE OD 2003 ROKU NA PRZYKŁADZIE RODZINY TONERÓW LASEROWYCH
Na początku 2003 roku Zarząd firmy Black Point, w porozumieniu z Menedżerami podjął decyzję o rozpoczęciu wdrożenia idei „wyszczuplania firmy”.
Pierwszym krokiem było przeprowadzenie szkolenia Symulacja Lean Manufacturing w siedzibie Wrocławskiego Centrum Transferu Technologii Politechniki Wrocławskiej (WCTT) dla 33 pracowników naszej firmy. W szkoleniu wzięli udział reprezentanci wszystkich obszarów i szczebli zarządzania firmy. Celem szkolenia dla tak licznej grupy było zaprezentowanie koncepcji „odchudzonej produkcji” i „zaszczepienie” wiary w jej skuteczność u przedstawicieli wszystkich działów, tak, aby zapewnić zaangażowanie w proces wdrożenia wszystkich pracowników. Kolejnym etapem było przeprowadzenie warsztatów mapowanie strumienia wartości w siedzibie Black Point. Zdefiniowano trzy główne strumienie:
- tonery laserowe;
- głowice atramentowe;
- nowe grupy produktowe.
Następnie dokonano analizy przepływów materiałowych i informacyjnych w perspektywie od dostawcy do klienta (od surowca po wyrób gotowy). Efektem prac było określenie map stanu obecnego oraz, po analizie i dyskusji, opracowanie map stanu przyszłego dla każdego ze zdefiniowanych strumieni. Analiza, w której udział brali pracownicy firmy oraz reprezentanci WCTT, pozwoliła na określenie obszarów wymagających usprawnień oraz wyznaczenie podstawowych zadań i opracowanie wstępnego planu wdrożeń poszczególnych projektów.
Złożoność poszczególnych procesów oraz duża liczba zadań zdecydowały o podjęciu decyzji o rozłożeniu w czasie prac nad poszczególnymi strumieniami wartości. Ze względu na strategiczne znaczenie grupy tonerów do drukarek laserowych (największy udział w wartości sprzedaży) zdecydowano o rozpoczęciu prac od tych właśnie produktów.
Podstawowe cele, jakie zostały zdefiniowane dla rodziny tonerów laserowych po zaprojektowaniu mapy stanu przyszłego, to:
- poprzez zmiany w obszarze przepływu informacji – redukcja zapasów wyrobów gotowych (poprawa wskaźnika obrotów magazynowych), redukcja przestrzeni wymaganej na składowanie, poprawa płynności finansowej;
- poprzez zmiany w obszarze przepływu materiałów – redukcja lead-time’u, poprawa jakości, redukcja wymaganej przestrzeni produkcyjnej, poprawa elastyczności systemu produkcyjnego, określenie potrzeb i możliwości w zakresie przyszłych uruchomień.
Główne zadania oraz efekty ich realizacji przedstawia tabela poniżej:
działanie | stan-początek 2003 | stan obecny 2010 |
---|---|---|
Zmiana systemu składania zleceń produkcyjnych | Raz w tygodniu na dwa tygodnie (w oparciu o prognozę) | Codzienny system składania zleceń produkcyjnych – kanbanów. Reagowanie na faktyczne potrzeby klientów, zmniejszenie zapasów w toku. |
Odpowiednie harmonogramowanie produkcji | Plan produkcji tygodniowy | Dzienny plan produkcji. Pełna dostępność wyrobu gotowego na magazynie. |
Obniżenie poziomu zapasów wyrobów gotowych | Zapas na poziomie 18 dni (średnio) | Zapas na poziomie 10… dni (średnio). Obniżenie poziomu zapasów tonerów laserowych wartościowo o około 50%. |
Skrócenie czasu przyjęcia wyrobów gotowych z produkcji na magazyn handlowy | 1 dzień | Max 2h. Szybsze uzupełnianie stanów magazynowych, zapewnienie wiarygodnych informacji dla Biura Handlowego |
Eliminacja czynności zbędnych, np.:
| Kontrola w magazynie, w chwili dostarczenia na produkcję, ponowna w chwili rozpoczęcia procesu produkcji Foliowanie każdej sztuki (w opakowaniu jednostkowym) | Kontrola w magazynie oraz bezpośrednio przy rozpoczęciu procesu produkcji Nowe opakowanie niewymagające foliowania [Skrócenie czasu przekazania materiałów do produkcji – karta kanban na komponenty dodatkowe i surowce pod serie zamówienia co 2h.] Odciążenie pracowników magazynu i produkcji; Eliminacja kosztów foliowania (materiał, praca, energia) Skrócenie czasu realizacji zlecenia produkcyjnego] |
Zmiany w Dziale Produkcji – nowy layout | Mało efektywne rozmieszczenie stanowisk pracy oraz maszyn wykorzystywanych w procesie produkcji | Wprowadzenie przepływu ciągłego na etapie „przygotowania do produkcji” Stworzenie kolejek FIFO między operacjami „przygotowania do produkcji” i „montażu laserów” oraz „montażu” i „pakowania”. „Zero dystansu między stanowiskami” – eliminacja transportowania Efektywne wykorzystanie powierzchni produkcyjnej Eliminacja zapasów produkcji w toku Uproszczenie wykonywanych operacji w procesie produkcji |
Zwiększenie częstotliwości dostaw materiałów do produkcji | Dostawy co 3 tygodnie | Dostawy co 2 tygodnie Zwiększenie elastyczności – szybsze odnawianie zapasów według rzeczywistych potrzeb |
II ETAP
LEAN MANUFACTURING – DOSKONALENIE WDROŻONEJ KONCEPCJI, W OKRESIE: OD 2004 DO 2009 NA PRZYKŁADZIE RODZINY TONERÓW LASEROWYCH
II etap projektu obejmował dlasze wdrażanie systemu ssącego na wyroby gotowe oraz produkcję toku tak, aby jeszcze bardziej skrócić czasy realizacji partii produkcyjnych. Wprowadzono także ilmeny standaryzacji pracy, aby poprawić produktywność.
Wprowadzenie fizycznego systemu KANBAN
Kanbany na produkcji przynoszone są przez magazyniera 5 razy dziennie i wkładane są do kuwety na stanowisku szefa zmiany.
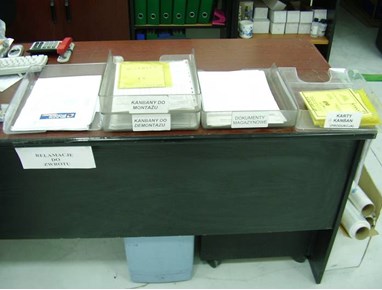
Rys. 4. Kuweta na karty kanban na stanowisku szefa zmiany. Kanbany przynoszone są z kuwet znajdujących się na magazynie
Planowanie bezpośrednie
Szef zmiany na bieżąco tworzy karty produkcyjne i zapotrzebowanie na surowce i umieszcza je w specjalnie przygotowanych kieszonkach.
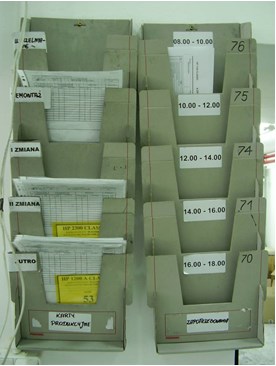
Rys.5. Karty kanban w ustalonej kolejności produkcji, skojarzone z drukami zleceń produkcyjnych
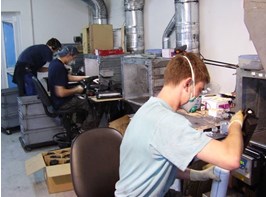
Rys. 6 Stanowiska demontażu tonerów laserowych – stan przed 2003 r.
Z procesu planowania wyeliminowany został logistyk i menedżer (pozostają osobami nadzorującymi i koordynującymi działania na styku). W bezpośrednim kontakcie pozostaje magazynier z szefem zmiany.
W 2004 roku w pierwszej fazie wprowadzania systemu ssącego zmodyfikowany został proces demontażu – linia technologiczna przygotowania surowca do produkcji. Zastosowano przepływ ciągły pomiędzy stanowiskami oraz wprowadzono standaryzację pracy. Pozwoliło to na skrócenie czasu operacji (średni czas realizacji serii produkcyjnej wynosił 120 min).
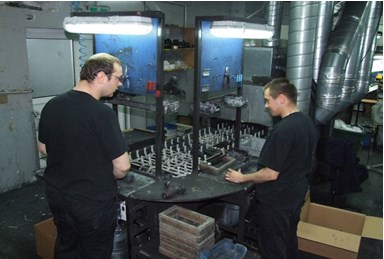
Rys. 7. Stanowiska demontażu – stan obecny 2010 r.
W następnych latach ciągle doskonaliliśmy nasz proces technologiczny poprzez zwiększenie stopnia automatyzacji i dalszą optymalizację. W efekcie dalej mamy przepływ ciągły pomiędzy stanowiskami, a obecnie średni czas realizacji serii wynosi 60 minut.
Skrócenie lead time’u procesu planowania
Aby skrócić czas oczekiwania półproduktu pomiędzy demontażem i montażem, jak również skrócić czas produkcji serii (realizacji zlecenia produkcyjnego) niezbędne było wprowadzenie elastycznych gniazd montażowych obsługiwanych przez 1, 2 lub 3 osoby. W efekcie tego został stworzony przepływ ciągły na montażu i pakowaniu i wyeliminowano zapasy pomiędzy stanowiskami, a realizacja serii wynosiła 120 minut.
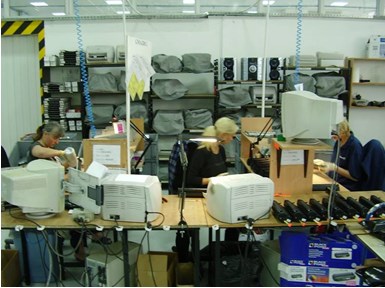
Rys. 8. Stanowiska montażu tonerów laserowych – stan przed 2003 r.
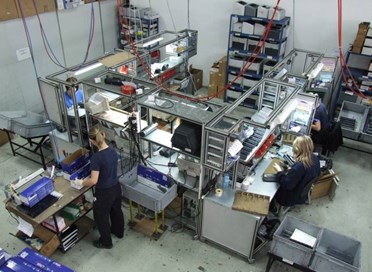
Rys. 9. Stanowiska montażu tonerów laserowych – stan obecny 2010 r.
W następnych latach ciągle doskonaliliśmy nasz proces technologiczny poprzez ergonomiczne stanowiska na montażu wprowadzając różne narzędzia Lean, takie jak np. 5S. W efekcie czego dalej mamy przepływ ciągły pomiędzy stanowiskami na montażu i pakowaniu. Ilość osób na gnieździe to czterech monterów (montaż 1 sztuki) oraz tester, który kontroluje jakość wydruków. Obecnie średni czas realizacji serii wynosi 60 minut.
Skrócenie lead time’u realizacji zlecenia nawet do jednego dnia nie dałoby to pełnego efektu, gdyby nie wprowadzenie systemu motywacyjnego z elementem wyszkolenia indywidualnego.
Sprzyjającego rozwojowi pracowników produkcji poprzez zdobywanie umiejętności na wszystkich stanowiskach produkcyjnych.
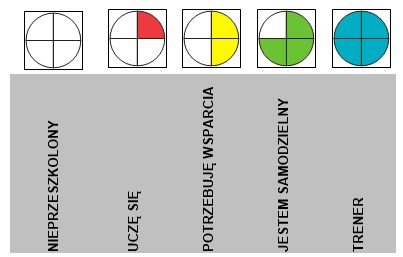
Rys.10. Oznaczanie kompetencji pracowników produkcyjnych
Zmiany w systemie wpływają bezpośrednio na skrócenie lead time’u produkcji serii, poprzez możliwość szybszego procesu szkolenia na stworzonych nowych stanowiskach pracy w elastycznych gniazdach.
III ETAP
W roku 2009 zarząd firmy Black Point zdecydował się postawić kolejny krok na drodze wdrażania szczupłego systemu zarządzania. Postanowiono ponownie prześwietlić cały proces, a następnie wykorzystać kolejne narzędzia Lean do dalszego zwiększania efektywności produkcji. Zmiany zapoczątkowane na produkcji będą kontynuowane także w innych działach firmy.
Od 2010 roku firma bierze udział w projekcie „Future SME” przy współpracy z Lean Enterprise Institute Polska.
Obecnie jesteśmy w trakcie realizacji tego projektu i na podstawie wyznaczonych wcześniej działań został opracowany szczegółowy harmonogram.
Analiza stanu obecnego
W ramach analizy stanu obecnego wykonano następujące zadania:
- Mierzenie czasów cykli dla poszczególnych etapów procesu;
- Mierzenie czasów przezbrojeń;
- Tworzenie godzinowych tablic spływu produkcji.
Tablice spływu dostarczają informacji o występujących problemach na poszczególnych etapach procesu. Pozwalają tym samym na ich zidentyfikowanie, a w dalszej kolejności rozwiązywanie poprzez zastosowanie odpowiednich narzędzi takich jak: wykresy Pareto, diagramy rybiej ości czy arkusze A3. Dodatkowo pozwalają na monitorowanie rzeczywistej ilości spływających sztuk z gniazda (w odstępach godzinowych) w stosunku do zaplanowanej ilości. Tablice spływu są również wykorzystywane przez szefów zmian do przygotowania codziennych spotkań z kierownikiem produkcji i wypełniania „Tablicy problemów”.
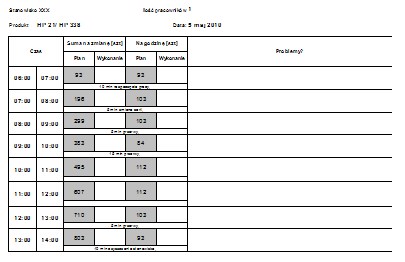
Rys. 11. Tablica godzinowa spływu produkcji
Mapowanie strumienia wartości na dziale tonerów atramentowych
Następnym etapem projektu było mapowanie strumienia wartości i opracowanie mapy stanu obecnego (rys.12).
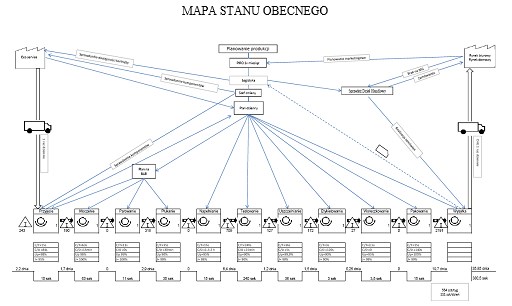
Rys.12. Mapa stanu obecnego na dziale tonerów atramentowych, stan na kwiecień 2010
Na podstawie analizy mapy stanu obecnego dla określonej grupy produktowej dostrzeżono marnotrawstwo na różnych etapach procesu. Kolejnym krokiem było opracowanie mapy stanu przyszłego (rys.13). Postanowiono połączyć niektóre etapy procesu zastosować supermarket, kolejki FIFO ,karty kanban oraz stworzenie przepływu „jednej sztuki”.
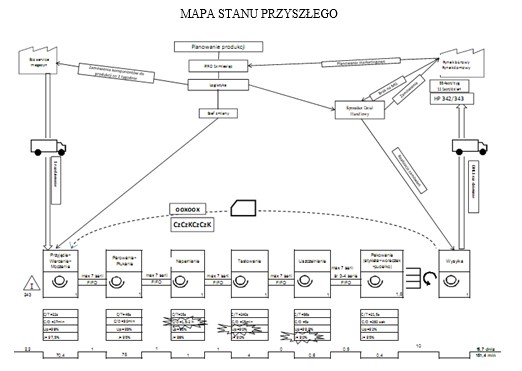
Rys.13. Mapa stanu przyszłego dla tonerów atramentowych
Optymalizację i usprawnienie obecnie istniejącego procesu chcemy osiągnąć poprzez:
- Połączenie stanowisk:
- „przyjęcia”, „ moczenia” i „wiercenia”;
- „parowania” i „płukania”;
- „etykietowania”, „woreczkowanie” i „pakowania do pudełek”.
co wyeliminuje zapasy w toku produkcyjnym oraz marnotrawstwo czasu;
- Wprowadzenie kolejki FIFO przed parowaniem i płukaniem, napełnianiem, testowaniem, uszczelnianiem i pakowaniem (max 7serii);
- Wprowadzenie supermarketu na wysyłce (zapas na 10 dni roboczych) – fizyczna karta kanban.
Przy okazji zobaczyliśmy także wiele nierozwiązanych problemów dotyczących stabilności: częste poprawki (wynikające z procesów wewnętrznych), długie czasy przezbrojeń, nadal brak standaryzacji niektórych procesów. Stąd też cel wyznaczony na lata 2010-2011 to dokończenie reorganizacji przypływu (strumieni wartości) i skupienie się na stabilności. Dotychczas reagowanie na problemy miało głównie formę działań doraźnych. Teraz chcemy jeszcze przyspieszyć doskonalenie, dzięki wdrożeniu usystematyzowanych metod rozwiązywania problemów.
Następnym etapem naszego projektu był warsztat z zakresu „Szczupłego systemu zarządzania”. Obejmował on kluczowe zagadnienia dotyczące identyfikacji problemów i usprawnienie przepływu informacji na różnych poziomach zarządzania.
Pozwolił on również na zdefiniowanie „łańcucha pomocy”, który zapewnia szybką reakcję na pojawiające się problemy.
Zastosowanie tablicy problemów oraz codzienne krótkie spotkania z osobami zarządzającymi danym obszarem pozwalają nam na szybkie zdefiniowanie przyczyny problemu i podjęcie odpowiednich działań korekcyjnych i zaplanowanie działań korygujących.
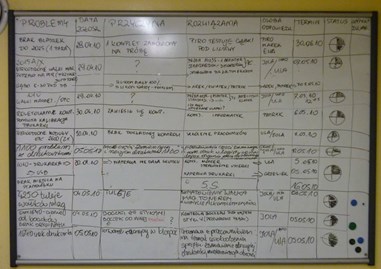
Rys. 14. Tablica codziennego monitorowania problemów
Efekty podejmowanych działań korekcyjnych i korygujących chcemy monitorować poprzez analizę trendów na następujących wykresach:
- wydajności;
- jakości;
- przyczyn utraty wydajności;
- zachowania dyscypliny.
Zestawione powyżej przykłady pokazują jak na przestrzeni kilku lat można znacznie podnieść produktywność i zmniejszyć koszty jednostkowe poprzez zrozumienie zależności pomiędzy całym procesem, a tymi operacjami, które rzeczywiście dodają wartość. Ciągłe doskonalenie poprzez wyznaczenie standardów, następnie wdrażanie odpowiednich narzędzi Lean pozwala stworzyć firmę konkurencyjną o wysokiej kulturze zarządzania oraz podnosi świadomość pracowników wszystkich szczebli. Każdy pracownik firmy Black Point dostrzega zalety ciągłego doskonalenia procesu technologicznego, integrując się z nim poprzez zgłaszanie własnych pomysłów oraz ich wdrażanie.
Projekt wdrożenia szczupłego systemu zarządzania pozwala nam spojrzeć na proces z innej perspektywy. Sprawia, że szybko dostrzegamy problemy, których wcześniej nie widzieliśmy, i co więcej pomaga je eliminować poprzez projektowanie usprawnień nie na zasadzie reakcji ad-hoc, ale na zasadzie systematycznej sformalizowanej analizy problemów na produkcji. Oczekujemy, że zakończenie projektu przyniesie wymierne korzyści, takie jak poprawa jakości, redukcja poprawek itp. Już pierwsze działania w tym kierunku zachęcają nas do ciągłego doskonalenia procesu oraz współpracy na stykach innych obszarów.
III Nowe obszary doskonalenia – Zarządzanie operacyjne i Planowanie Strategiczne
A. Historia wyniku finansowego Black Point 2001-2009.
Rozpoczęcie wdrażania systemu Lean na produkcji w 2003 roku połączyliśmy z zastosowaniem elementów szczupłego myślenia w zarządzaniu całą firmą. Między innymi wyeliminowaliśmy z oferty niskomarżowe produkty i zlikwidowaliśmy własną księgowość na rzecz biura rachunkowego. Działania te, obok relacjonowanego wcześniej, wzrostu produktywności doprowadziły do zmniejszenia sprzedaży i bardzo znacznego wzrostu zyskowności i zysku w tym samym i następnym roku.
B. Problemy, z którymi się zmierzyliśmy.
Niestety rekordowe wyniki uzyskane przez firmę w 2004 roku uśpiły naszą czujność i następne 4 lata były pod tym względem znacznie gorsze. Wynik finansowy spadł prawie o połowę …
Stało się to w wyniku równoczesnego działania czynników zewnętrznych i wewnętrznych.
Czynnikami zewnętrznym były:
- umacnianie się złotówki w stosunku do głównych walut co skutkowało spadkiem cen produktów importowanych i wywołało silną presję na obniżki cen naszych produktów;
- znaczny wzrost poziomu wynagrodzeń w Polsce w latach 2005-2008 co pociągnęło za sobą wzrost kosztów produkcji./li>
Czynnikiem wewnętrznym był rozrost organizacji połączony ze wzrostem zatrudnienia, który pociągnął za sobą komplikowanie relacji wewnętrznych i duży wzrost kosztów materialnych i niematerialnych funkcjonowania firmy.
Ponieważ systematyczny wzrost sprzedaży w latach 2006-2008 połączony z wdrażaniem pozytywnych zmian w organizacji produkcji nie przynosił odpowiednich rezultatów w postaci rosnących zysków zarząd postanowił w połowie 2008 roku opracować i wdrożyć program poprawy efektywności firmy, który oparty został o filozofię Lean Thinking i zmierzał do likwidacji marnotrawstwa i zbędnych wydatków we wszystkich sferach działalności firmy.
Przede wszystkim zmiany dotyczyły organizacji, wzmocniliśmy kryteria efektywnościowe w systemach motywacyjnych jak również dostosowaliśmy liczbę pracowników do aktualnych potrzeb firmy. Drugie pole optymalizacji to eliminacja zbędnych działań bez pozytywnego wpływu na biznes i wynik oraz odświeżyliśmy politykę bonusową oraz wsparcia sprzedaży naszych partnerów handlowych.
Wdrożenie programu poprawy efektywności połączone z osłabieniem presji cenowej na nasze produkty zaowocowało obficie w roku 2009, który zakończył się znakomitymi rezultatami w zakresie wzrostu sprzedaży i wyniku finansowego.
C. Problemy, które stoją przed nami.
Jednym z głównych problemów z jakimi musimy się zmierzyć w przyszłości jest znalezienie i opanowanie narzędzi, które pomogą nam w systematyczny sposób oceniać i zmieniać naszą organizację w obszarach „miękkich” takich jak marketing, sprzedaż i administracja.
Brak dostępności lub znajomości narzędzi równie zaawansowanych jak te, które mogliśmy zastosować w obszarze produkcji (przepływ ciągły, system ssący, Kaizen) stanowi dla nas istotne wyzwanie.
Stając przed nim zarząd Black Point opracował pod koniec 2009 roku nową mapę strumieni wartości i układ procesów w firmie, które obejmują wszelkie sfery działalności firmy a przede wszystkim proces strategiczny, którego cykl skróciliśmy z 1 roku do 6 miesięcy. Podstawowym założeniem, które przyjęliśmy do projektowania tych zmian było skutecznie wkomponowanie we wszystkich procesach cyklu PDCA, czyli etapu planowania, wykonania, sprawdzenia i doskonalenia. Kolejnym działaniem było odświeżenie standaryzacji procesów, którą traktujemy jako niezbędne narzędzie gwarantujące powtarzalność działań.
Układ ten został w firmie wdrożony w pierwszym kwartale 2010 roku a w drugim jest przeglądany i oceniany pod względem efektywności.
IV Wnioski
Historia siedmiu już lat wdrażania systemów Lean w naszej firmie pokazała ogromną ich przydatność i efektywność, ale wykazała także ponownie, że jesteśmy dopiero na początku drogi do Lean Enterprise, czyli pełnego wdrożenia zasad lean we wszystkich obszarach firmy, a praca nad efektywnością firmy nigdy się nie kończy.