Transformacja Lean na przykładzie najlepszych praktyk w Parker Hannifin Manufacturing Poland
100 LAT PARKER HANNIFIN
W 1917 r. inżynier Arthur Parker założył w Cleveland w Ohio (USA) firmę Parker Appliance Company (Rys.1). Pierwszymi produktami były pneumatyczne układy hamulcowe do samochodów ciężarowych i autobusów wg pomysłu własnego A. Parkera. Kolejne lata to dynamiczny rozwój i poszerzanie zakresu działalności. Wysokociśnieniowe złączki hydrauliczne były zastosowane m.in. w samolocie „Spirit of St. Louis” podczas pierwszego lotu przez Atlantyk w 1927 r. Charlesa Lindenberga (Rys. 2). Parker dostarcza technologie kosmiczne dla NASA już od czasu pierwszych misji Apollo.
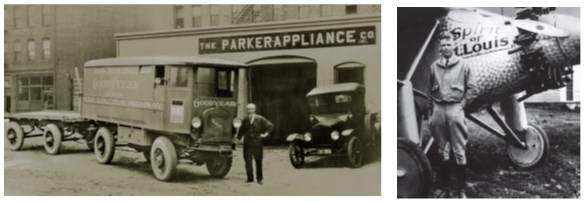
po lewej: Rys. 1 Pierwsza siedziba Parker Appliance Company; po prawej: Rys. 2 Charles Lindenbergh na tle samolotu Spirit of St. Louis
Firma Parker, obecnie pod nazwą Parker Hannifin jest notowanym na giełdzie nowojorskiej światowym liderem w dziedzinie napędów i sterowań. Globalna sieć firmy Parker obejmuje ponad 300 zakładów w 50 krajach, a także ponad 13.000 niezależnych partnerów dystrybucyjnych i przeszło 3000 sklepów ParkerStore. Obecnie Parker oferuje blisko milion produktów – to najszerszy na rynku asortyment rozwiązań z zakresu technologii przemysłowych, dostępnych u jednego dostawcy!
Pierwszy zakład produkcyjny Parker Hannifin w Polsce powstał we Wrocławiu w 1995 r. Od tego czasu wiele się zmieniło, m.in. zabrakło miejsca pod kolejne maszyny, co przyczyniło się do decyzji o wybudowaniu nowoczesnego zakładu w Siechnicach pod Wrocławiem w 2004 r. Od momentu powstania w zakładzie wyprodukowano ponad 500 milionów złączek. Na przestrzeni lat zwiększało się zapotrzebowanie na produkowane przez nas wysokociśnieniowe złączki hydrauliczne, dochodziły kolejne produkty, nowe maszyny i stanowiska montażowe. Radykalnie zmieniły się ilości szt. w 1 zleceniu produkcyjnym – kiedyś były to dziesiątki tysięcy, teraz coraz częściej są to pojedyncze sztuki. Takie zmienne środowisko wymuszało, wymusza i będzie wymuszać ciągłe usprawnianie procesów.
9 lat temu kierownictwo Zakładu Produkcyjnego Parker Hannifin Manufacturing Poland podjęło decyzję o znaczącym przyspieszeniu transformacji Lean. Lata 2011-2013 to intensywna praca nad uzyskaniem wewnątrzkorporacyjnego certyfikatu MMS (Manufacturing Model Site) zakończona sukcesem we wrześniu 2013 r. oraz wsparcie tego programu metodyką PMI.
W niniejszym artykule zostaną zaprezentowane praktyczne zastosowania wybranych narzędzi Lean z kolejnych etapów transformacji oraz praca nad rozwojem systemu produkcyjnego:
- Optymalizacja przepływu materiału i poprawa produktywności na montażu (milk run),
- Stabilizacja procesu produkcyjnego poprzez rozwój programu TPM,
- Rozwój metody kolejkowania zleceń na potrzeby SMED i obiegu logistycznego.
Przejście tej drogi umożliwiło nam przede wszystkim osiągnięcie wskaźników biznesowych na poziomie oczekiwanym przez akcjonariuszy. Wartością dodaną dla organizacji są: ogromne doświadczenie, zaangażowanie pracowników, transfery produkcji oraz kolejne inwestycje.
OPTYMALIZACJA PRZEPŁYWU MATERIAŁU I POPRAWA PRODUKTYWNOŚCI NA MONTAŻU (MILK RUN)
Decyzja o wdrożeniu rutyny mleczarza (milk run) na stanowiskach montażowych VS3/5 była podyktowana wieloma problemami, z którymi borykaliśmy się w tym obszarze. Należały do nich między innymi:
- Problemy logistyczne:
- Niejasny podział obowiązków między logistykami
- Niezbalansowane obłożenie pracą (największe obciążenie w momencie wypuszczenia nowych planów na montażu)
- Marnotrawstwo związane z szukaniem komponentów oraz chodzeniem między stanowiskami i magazynami.
- Problemy montażowe:
- Zlecenia montażowe nie były montowane przez monterów zgodnie z sekwencją w planach montażowych, co powodowało zakłócenia w obsłudze logistycznej stanowisk
- Operatorzy musieli czekać na brakujące komponenty (zgłaszanie braków poprzez alarm dźwiękowy i świetlny dla logistyka).
- Problemy planistyczne:
- Osobne pliki z planami montażowymi dla każdego stanowiska montażowego – 7 plików Excel
- Brak możliwości dostosowania planów montażowych do liczby osób pracujących na stanowisku montażowych
- Czasochłonne tworzenie (przeliczanie) planów montażowych.
Dodatkowym elementem, który przyspieszył decyzje o wdrożeniu rutyny mleczarza, były nowe transfery produkowanych wyrobów na tych stanowiskach montażowych. Transfery te nie mogły spowodować zwiększenia liczby pracowników logistyki.
Postanowiliśmy powołać zespół osób pracujących nad tym projektem, którzy pochodzili z różnych obszarów firmy: montaż, logistyka, planowanie, dział Lean, dział IT. Pozwoliło to na spojrzenie na dany problem z różnych perspektyw i na wypracowanie wspólnych, zaakceptowanych przez większość, zmian i usprawnień.
Przed rozpoczęciem projektu zespół postawił sobie również określone cele, które chciał osiągnąć po zakończeniu projektu:
- Zbalansowanie pracy logistyków, tak aby obsłużyć stanowiska montażowe VS3/5 za pomocą dwóch mleczarzy przy zwiększonej ilości produkowanych detali – rutyna mleczarza
- Zredukowanie ilość alarmów związanych z brakującymi komponentami o >50%
- Zredukowanie marnotrawstwa związanego z szukaniem, chodzeniem i oczekiwaniem – wzrost produktywności o 10%
- Optymalizacja i przyspieszenie działania narzędzia do generowania planów (redukcja czasu cyklu (C/T) na zlecenie dla koordynatora o 20%).
Pierwszym krokiem w projekcie było szczegółowe opisanie stanu aktualnego. Opisane zostały wszystkie problemy związane z zatrzymaniem stanowisk montażowych, z szukaniem komponentów, przygotowywaniem zleceń. Zmierzone zostały czasy przygotowywania zleceń montażowych i drogi przemierzane przez mleczarzy. Przeanalizowane zostały przyczyny zgłaszania alarmów przez operatorów montażu o brakujących komponentach i zleceniach. Mając dokładny obraz stanu aktualnego łatwo było zdefiniować niezbędne działania do usprawnienia poszczególnych procesów. Do najważniejszych usprawnień, jakie udało się wdrożyć należą:
- Wdrożenie supermarketów przystanowiskowych (Rys. 3) i systemu dwóch skrzynek dla szybko rotujących komponentów – pozwoliło to na skrócenie czasu przygotowywania zleceń montażowych, lepszą dostępność komponentów montażowych dla monterów oraz zredukowanie czasu uzupełniania wcześniejszych magazynów przy stanowiskach.
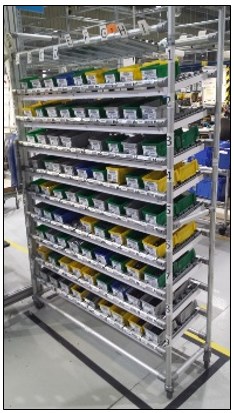
Rys. 3 Supermarket przystanowiskowy
- Wdrożenie transportowych kart Kanban – dla komponentów dostarczanych w ciężkich pojemnikach (Rys. 4) oraz dla komponentów współdzielonych z innymi magazynami w zakładzie. Pozwoliło to na czasową obsługę stanowisk montażowych przy uzupełnianiu zużytych komponentów oraz na znaczące zredukowanie chodzenia związanego z uzupełnianiem głównego magazynu komponentów o współdzielone komponenty.
- Wdrożenie tras mleczarza – postanowiono podzielić pracę między dwóch logistyków. Pierwszy logistyk zajmuje się obsługą stanowisk montażowych. Jego praca została podzielona na trzy osobne obiegi:
- żółty – związany z dostarczaniem zleceń montażowych na stanowiska montażowe (Rys. 5),
- niebieski – związany z uzupełnianiem supermarketów przystanowiskowych (Rys. 6),
- pomarańczowy – związany z odbiorem wyrobów gotowych (Rys. 7).
Rysunek 5 Pętla żółta kursu mleczarza – związana z dostarczaniem zleceń montażowych na stanowiska montażowe
Rysunek 6 Pętla niebieska kursu mleczarza – związana z uzupełnianiem supermarketów przystanowiskowych
Rysunek 7 Pętla pomarańczowa kursu mleczarza – związana z odbiorem wyrobów gotowych
Wszystkie te trasy są obsługiwane przez proste wózki transportowe, zbudowane przez zespół lub zakupione z dostępnych na rynku elementów (Rys. 8). Pozwoliło to na znaczące zredukowanie chodzenia oraz handlingu logistycznego.
Rysunek 8 Proste wózki transportowe, zbudowane przez zespół lub zakupione z dostępnych na rynku elementów
Drugi logistyk pracuje tylko w obszarze magazynu. Jego zadaniem jest kompletowanie zleceń montażowych, uzupełnianie pustych pojemników supermarketowych oraz rozkładanie zwrotów z montażu na magazyn.
Dla obu logistyków opracowany został szczegółowy harmonogram określający, jak ich praca ma wyglądać „minuta po minucie” (Rys. 9).
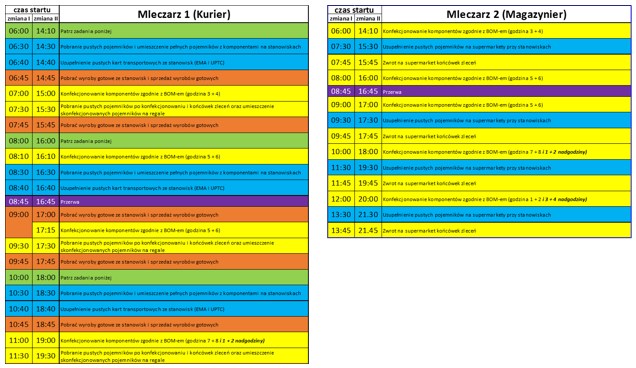
Rysunek 9 Harmonogramy pracy dla obu pracowników logistyki
- Wdrożenie Heijunki – wszystkie zlecenia montażowe drukowane są przez koordynatora montażu i umieszczane w heijunce, z wyprzedzeniem dwóch godzin (Rys. 10). Zlecenia drukowane są w takiej kolejności, jak znajdują się w planie. W czasie tych dwóch godzin magazynier ma czas na przygotowanie zleceń, a mleczarz na dostarczenie ich do stanowisk montażowych. Opracowany został dokładny harmonogram drukowania zleceń, aby sprząc pracę koordynatora, magazyniera i mleczarza. Dzięki takiemu rozwiązaniu logistycy dokładnie wiedzą, jaką pracę mają do wykonania. W przypadku jakichkolwiek problemów z przygotowaniem zlecenia, magazynier bezpośrednio informuje koordynatora, który ma możliwość szybkiej korekty planów montażowych i wydrukowanie nowych zleceń, zapobiegając zatrzymaniom na stanowiskach montażowych. Aby zapewnić montaż zleceń zgodnie z kolejnością w planie, na regałach z przygotowanymi zleceniami wprowadzono dodatkową wizualizację kolejności montażu.
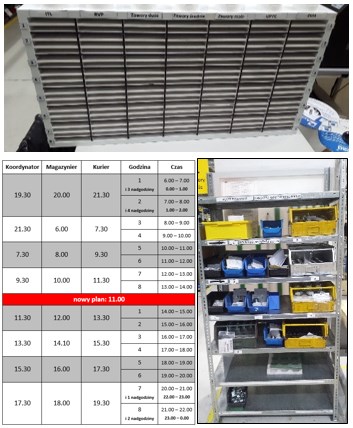
Rysunek 10 Heijunka dla zleceń montażowych, harmonogram drukowania tych zleceń oraz regał z przygotowanymi zleceniami
- Wdrożenie nowego narzędzia do tworzenia i zarządzania planami montażowymi – poprzednie siedem plików z planami montażowymi, zastąpione zostało jednym plikiem Excel (Rys. 11). Plik ten wykorzystuje makra do dokładnego planowania procesu montażu. Wprowadzane są informacje na temat zleceń, ilości sztuk do wykonania, ilości dostępnych pracowników na stanowisku montażowym. Po naciśnięciu jednego przycisku w kilka sekund generowany jest plan, pokazujący jakie zlecenia i w jakich ilościach mają zostać zmontowane godzina po godzinie. Największą zaletą tego narzędzia jest możliwość bieżącej aktualizacji planów, w przypadku problemów z przygotowaniem zleceń lub dostępnością osób. Pozwala to na zapewnienie zrównoważonej pracy dla logistyki i znacząco obniża prawdopodobieństwo zatrzymania stanowisk montażowych z powodu niewłaściwej obsługi logistycznej.
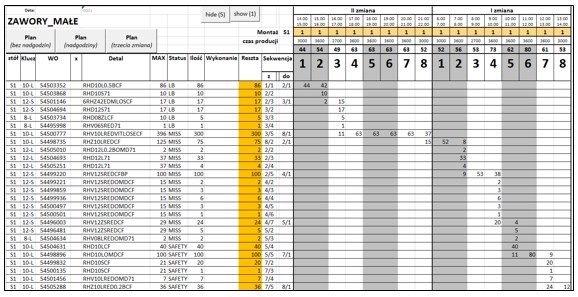
Rysunek 11 Arkusz pliku Excel do tworzenia i zarządzania planami montażowymi
Wszystkie powyższe usprawnienia pozwoliły nam w ostateczności na znaczącą poprawę obsługi logistycznej montażu oraz na wyeliminowanie wielu problemów planistycznych. Najważniejsze rezultaty, jakie udało się osiągnąć, to:
- Jasne zasady i przypisane zadania dla pracowników logistyki – zwiększone ilości montowanych części mogą być obsłużone przez tę samą liczbę logistyków
- Wzrost produktywności na montażu o 9%
- Ilość alarmów związanych z brakiem komponentów zredukowana została o 90%
- Wyeliminowanie poszukiwania części poprzez generowanie planów montażowych tylko dla dostępnych komponentów w magazynie
- Poprzez implementację 3 rutyn mleczarza i transportowych kart Kanban zredukowano długości dróg przemierzanych przez pracowników logistyki o 80%
- Poprzez wdrożenie nowego narzędzia do zarządzania planami montażowymi, zredukowano czas przygotowania zlecenia przez koordynatora montażu o 20%.
Oczywiście możliwe są kolejne rozwiązania celem usprawnienia opisanych tu procesów. Kolejnymi elementami, nad którymi chcielibyśmy popracować, są:
- Opracowanie narzędzia do bardziej precyzyjnego obliczania czasów cyklu dla wszystkich stanowisk, produktów i liczby pracowników
- Uproszczenie procesu drukowania zleceń i etykiet, a następnie przekazanie tego procesu do logistyki
- Zredukowanie ilości operacji wykonywanych przez mleczarza i magazyniera poprzez zastąpienie regałów ze zleceniami małymi wózkami transportowymi
- Zmiana layoutu stanowisk montażowych w celu optymalizacji przepływu materiałów i redukcji obsługi logistycznej.
STABILIZACJA PROCESU PRODUKCYJNEGO POPRZEZ ROZWÓJ PROGRAMU TPM
Decyzja podjęta przez kierownictwo zakładu o tym, by starać się o zdobycie w Parker Hannifin certyfikatu Manufacturing Model Site oznaczała podjęcie szeregu działań tak, aby osiągnąć zamierzony cel. TPM jest jednym z podstawowych narzędzi filozofii Lean Manufacturing i aby sprostać wymaganiom certyfikatu, konieczne było wdrożenie istotnych zmian w obszarze utrzymania ruchu. Wysokie i nieprzewidywalne koszty utrzymania ruchu, niezadowalająca planowa i autonomiczna konserwacja maszyn okazały się głównymi obszarami do poprawy. Decyzja o projektowym podejściu do realizacji zaplanowanych zadań była bardzo trafna. Powstała karta projektu (Rys. 12), w której określono główne cele, jakie należy osiągnąć oraz zdefiniowano kamienie milowe. Liderem projektu został kierownik utrzymania ruchu. Zespół projektowy, powołany przez lidera, składał się głównie z pracowników utrzymania ruchu, ale nie zabrakło też przedstawicieli innych działów, m.in. Lean, IT, produkcji, logistyki, personalnego i finansowego. Zidentyfikowano interesariuszy projektu, zebrano ich wymagania i oczekiwania. Na podstawie karty projektu oraz zebranych wymagań powstał harmonogram projektu oraz została wykonana analiza ryzyka i szans. Siedem celów zdefiniowanych w karcie projektu przełożyło się na 165 zadań rozpisanych w harmonogramie, a sumaryczny czas trwania projektu wyniósł 2 lata.
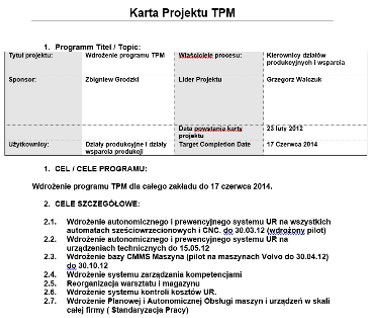
Rysunek 12 Karta projektu TPM
Wdrożenie programu TPM podzielono na trzy główne etapy:
I. Budowanie świadomości (ogłoszenie załodze decyzji o wdrożeniu programu przez kierownictwo zakładu, Kick-Off meeting, szkolenia dla wszystkich pracowników)
II. Budowanie podstaw „świątyni” TPM (5S – wizualizacja i wdrożenie standardów, praca zespołowa poprzez powołanie efektywnych zespołów pracowniczych)
III. Wdrożenie planowej (PM) i autonomicznej konserwacji (AM) maszyn.
Wdrożenie drugiego i trzeciego etapu jednocześnie w skali całej fabryki skazane byłoby raczej na niepowodzenie, dlatego wytypowano obszary pilotażowe, gdzie wdrożono zasady 5S, PM i AM. Po wnikliwej analizie wdrożonych rozwiązań, wprowadzono niezbędne udoskonalenia i sukcesywnie narzędzia TPM zostały wdrożone w całej fabryce. Standardy AM i PM ewoluują zgodnie z zasadą ciągłego doskonalenia.
Zasady wdrożenia pierwszego i drugiego etapu oraz zastosowane narzędzia są podobne we wszystkich przedsiębiorstwach nawet, jeśli różnią się one rodzajem produkcji, wielkością, itp. W przypadku trzeciego etapu, różnice mogą być znaczące i zastosowane narzędzia powinny być dostosowane do specyfiki przedsiębiorstwa i oczekiwań kierownictwa.
Zarząd firmy Parker Hannifin kładzie duży nacisk na pracę zespołową, upatrując w tym podejściu drogę do osiągania sukcesów. Dział utrzymania ruchu Zakładu Produkcyjnego Parker Hannifin w Siechnicach uczestniczy w programie HPT (High Performance Team). Na jednym z wyjazdowych warsztatów HPT została wspólnie zdefiniowana misja działu: „Wspieramy, naprawiamy, na czas działamy a brak reklamacji to wzrost naszych akcji” oraz powstała karta upełnomocnienia zespołu.
Zespół utrzymania ruchu, wspierany przez trenerów wewnętrznych, rozwija się w ramach uczestnictwa w programie HPT zwiększając swoje kompetencje m.in. we wzajemnej komunikacji, podejmowaniu decyzji i zarządzaniu konfliktem.
Podejście projektowe i zespołowe przyczyniło się do sukcesu w procesie wdrażania narzędzi TPM. Na rysunku 14 zaprezentowano przykłady przeprowadzonych zmian.
W zespołach produkcyjnych i działach wsparcia przeprowadzono warsztaty 5S oraz opracowano i wdrożono standardy czystości.
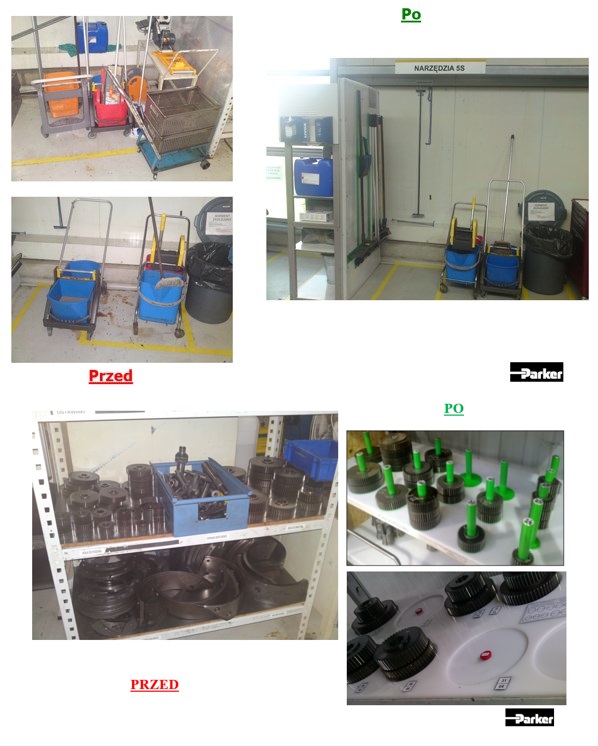
Rys. 14 Kąciki czystości i regały z częściami zamiennymi do maszyn przed i po zmianach

Rys. 14 Kąciki czystości i regały z częściami zamiennymi do maszyn przed i po zmianach
Przeprowadziliśmy warsztaty TPM (Rys. 15), które odbywały się zgodnie z harmonogramem projektu.
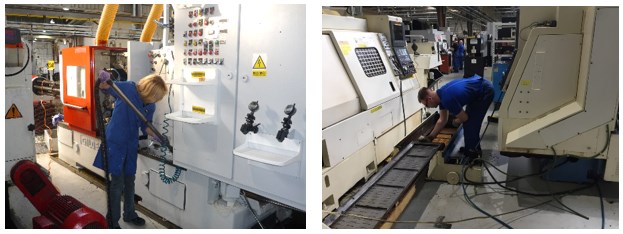
Rysunek 15 Czyszczenie maszyn podczas warsztatów TPM
Wdrożyliśmy instrukcje autonomicznej konserwacji na maszynach (Rys. 16). Instrukcje zostały opracowane przez zespoły składające się z operatorów maszyn i mechaników. Dzięki temu, proste czynności konserwacyjne są wykonywane przez operatorów maszyn.
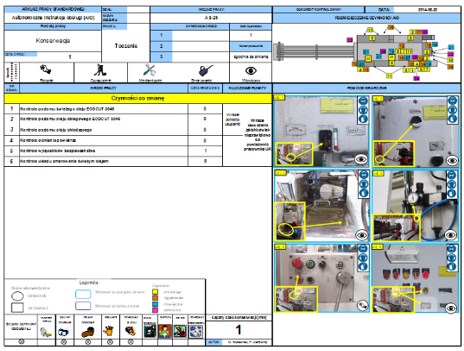
Rysunek 16 Przykład instrukcji autonomicznej konserwacji
Odpowiedzialność za prawidłowe funkcjonowanie autonomicznej konserwacji spoczywa na liderach zespołów produkcyjnych. System audytów poziomowanych, który obejmuje swoim zakresem 5S i TPM, pozwala na szybkie wykrycie niezgodności i natychmiastowe wdrożenie działań korygujących (Rys. 17).
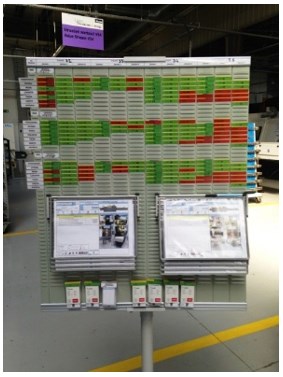
Rysunek 17 Tablica Kamishibai dla autonomicznej konserwacji
Równolegle z pracami związanymi z implementacją autonomicznej konserwacji, realizowane były zadania związane z rozwojem planowego utrzymania ruchu. Awarie maszyn i zgłoszenia serwisowe operatorzy maszyn wpisywali do dwóch zeszytów umieszczonych przy warsztacie utrzymania ruchu. W skrajnych przypadkach operator musiał pokonać 120 m w jedną stronę, aby dokonać wpisu do zeszytu.
Na podstawie wpisów do zeszytu niemożliwe było wyliczanie współczynników charakterystycznych dla utrzymania ruchu: MTBF, MTTR, dostępność maszyn. Brakowało macierzy krytyczności dla maszyn i urządzeń. Przeglądy maszyn wykonywane były sporadycznie, bez żadnego planu. Zarządzanie magazynem części zamiennych odbywało się ręcznie. Trudno było przewidzieć i kontrolować koszty utrzymania ruchu.
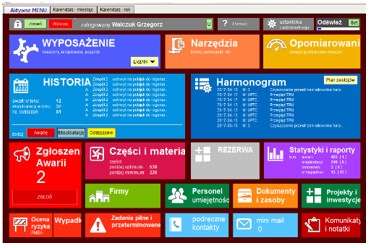
Rysunek 18 Ekran główny programu CMMS
Zakupiliśmy i wdrożyliśmy program komputerowy klasy CMMS (Computerised Maintenance Management Systems), wspierający zarządzanie utrzymaniem ruchu (Rys. 18). Program ten ułatwia zarządzanie bieżącymi naprawami, zaplanowanymi przeglądami maszyn i zapasami części zamiennych. Umożliwia również łatwy dostęp do historii eksploatacji maszyn i urządzeń. Operatorzy maszyn mają dostęp do modułu zgłoszeń awarii bezpośrednio przy swoich maszynach. Program CMMS zbiera dane i generuje statystyki związane z postojami maszyn, a także umożliwia analizę kosztów.
Na podstawie takich danych jak MTTR, MTBF i analiza Pareto najczęściej występujących awarii, można podejmować optymalne decyzje odnośnie planowania przeglądów i ustalania stanów magazynowych.
Nawet najlepsze programy wspomagające zarządzanie utrzymaniem ruchu nie zastąpią człowieka, nie naprawią maszyn i nie wykonają przeglądów prewencyjnych. Nasz park maszynowy jest bardzo zróżnicowany. Mamy maszyny, które mają 40 – 50 lat, ale obok tych starszych pracują nowoczesne obrabiarki CNC. Zespół utrzymania ruchu powinien składać się z osób kompetentnych, zaangażowanych i upełnomocnionych. Wzrost zaangażowania i upełnomocnienia zespołu realizowany jest w ramach programu HPT. Wiedzę i umiejętności potrzebne do realizacji prewencji i napraw maszyn zespół utrzymania ruchu nabywa poprzez uczestnictwo w specjalistycznych szkoleniach. Powstała macierz kompetencji i podczas corocznych, indywidualnych rozmów rozwojowych ustalane są plany szkoleniowe na kolejny rok dla każdego pracownika UR. Wdrażamy standardy pracy opracowane zespołowo przez pracowników utrzymania ruchu (Rys. 19). Szukając dojścia do przyczyn źródłowych występujących problemów z maszynami, stosujemy powszechnie znane narzędzia: diagram Ishikawy, 5xWhy czy też arkusz A3 (Rys. 20). Dzięki takiemu podejściu do problemów, dużą ilość przyczyn źródłowych awarii udało nam się wyeliminować lub znacznie zredukować ich występowanie.
Rysunek 19 Przykład standardu pracy UR
Opisane powyżej działania zrealizowano zgodnie z harmonogramem projektu TPM, co w znacznym stopniu przyczyniło się do zdobycia certyfikatu MMS we wrześniu 2013 r. Wdrożenie AM i PM oraz systemu CMMS, który pozwolił na analizę wskaźników UR i podejmowanie optymalnych decyzji, zaowocowało znaczną poprawą stanu technicznego parku maszynowego. Terminale do systemu CMMS znajdują się w każdym zespole produkcyjnym, zgłaszanie awarii jest szybkie i proste, dzięki temu czas reakcji UR na zgłoszenie awarii został zredukowany z 44 minut (w czerwcu 2014 r.) do 20 minut obecnie. Dostępność maszyn wzrosła o 9% w ciągu dwóch ostatnich lat. Analiza rzeczywistego zużycia części zamiennych pozwoliła na redukcję zapasów średnio o 50%, koszty utrzymania ruchu zostały zredukowane o ok. 30% na przestrzeni ostatnich trzech lat.
ROZWÓJ METODY KOLEJKOWANIA ZLECEŃ NA POTRZEBY SMED I OBIEGU LOGISTYCZNEGO
Tło
Przeprowadzone wcześniej warsztaty Mapowania Strumienia Wartości (VSM) wykazały wiele problemów w strumieniu wartości dla wybranej dominującej rodziny produktów w naszym zakładzie. Jednym z oznaczonych i zdefiniowanych wyzwań był czas przezbrojenia i liczba przezbrojeń wykonywanych na automatach tokarskich. Dodatkowym czynnikiem motywującym było zrealizowanie potrzeb wiodącego klienta związanych z terminowością dostaw dla założonych ograniczeń.
Pierwsze mocne uderzenie
Warsztaty SMED zostały przeprowadzone bardzo klasycznie. Wykonany został film i przeprowadzono jego analizę. Wykonany został wykres przebiegu czynności analizowany pod kątem siedmiu marnotrawstw. Szukano typowych problemów podczas przezbrojenia, takich jak regulowanie procesu, czy szukanie narzędzi oraz przerywanie pracy z różnych powodów. Na zakończenie powstał nowy standard przezbrojenia.
Pierwsza obserwacja wskazała nam bardzo poważny problem. Na jednym automacie tokarskim wytwarza się w zakładzie kilkadziesiąt różnych rodzajów części i przezbrojenia pomiędzy różnymi rodzajami części niestety się różnią. Przykładowo, dla maszyny produkującej 50 różnych referencji i zakładając, że przezbrojenie z części „A” na „B” to to samo, co przezbrojenie z „B” na „A”, mamy aż 1225 (kombinacji bez powtórzeń ) możliwych kombinacji przezbrojeń!!! Usprawnienie tylko jednej z kombinacji przezbrojeń nie będzie miało wobec tego żadnego realnego wpływu na produkcję i osiągane wyniki, takie jak OEE czy terminowość dostaw. Mało tego, aby przetestować nowy standard opracowany podczas warsztatów SMED trzeba byłoby tę konkretną kombinację przezbrojenia sztucznie wywołać, gdyż nie wiadomo, kiedy faktycznie z planów produkcyjnych wynikłaby potrzeba tej konkretnej kombinacji przezbrojenia. Plany produkcyjne i wynikająca z nich sekwencją przezbrojeń są bowiem opracowywane wyłącznie na podstawie zamówień klienta.
W tej sytuacji projekt mógłby się w tym momencie zakończyć, często używanym stwierdzeniem „Tak, ale to u nas niemożliwe. My jesteśmy specyficzni, inni,…..itd.”. Jedyne korzyści, jakie byłyby do uzyskania to, co najwyżej na drobnych działaniach związanych z redukcją szukania narzędzi i chodzenia, czyli praktycznie zakres działań „5S”. Do tematu podchodziliśmy kilkukrotnie szukając rozwiązania, jak wykonać działania „SMED” w środowisku produkcyjnym Parkera i od razu na wszystkich maszynach. Celem było osiągnięcie realnych zysków biznesowych.
Ważnym elementem dla dalszych kroków w projekcie, okazała się multi-dyscyplinarność zespołu, a przede wszystkim różnorodność doświadczeń zawodowych członków zespołu. Elementem, który pozwolił ruszyć z miejsca, okazało się być, doświadczenie zdobyte przy standaryzacji prac utrzymania ruchu narzędzi odlewniczych. Podstawą tej standaryzacji jest określenie i zdefiniowanie czynności elementarnych, z kombinacji których można złożyć jak z modułów każdą konserwację. W przełożeniu na język przezbrojenia automatu tokarskiego, trzeba było zdefiniować wszystkie zamknięte pakiety czynności, jakie mogą wystąpić w przezbrojeniu. Zadanie to wykonali ustawiacze z wieloletnim doświadczeniem, razem z inżynierami procesu. Zdefiniowanych zostało 23 takich zamkniętych sekwencji czynności. W zasadzie od tego momentu wystarczy przygotować dokładny standard czynności, których jest dokładnie 23 (Rys. 21). Standard przezbrojenia to już tylko wybranie konkretnych czynności i złożenie ich w sekwencje.
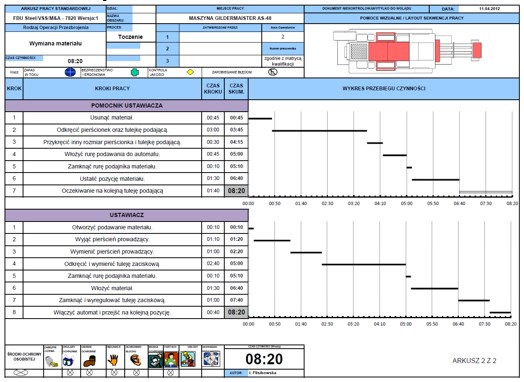
Rysunek 21 Przykład standardu dla jednej z dwudziestu trzech zamkniętych sekwencji czynności podczas przezbrojenia automatu tokarskiego, w tym przypadku – wymiany materiału
Bazując na tej standaryzacji powstał system szkoleń modułowych dla ustawiaczy. Został on rozszerzony o moduły z rysunku technicznego czy podstaw obróbki skrawaniem, ale jego główny trzon to moduły/standardy elementarnych czynności przezbrojenia. Ten system szkoleń dał też możliwość łatwego uzupełniania wiedzy czy przypomnienia sobie dawno nieużywanego modułu bez konieczności przechodzenia przez pełny program szkoleniowy. Zakres tego programu stał się podstawą do egzaminów kwalifikacyjnych dla ustawiaczy.
Takie podejście daje też świetny materiał do optymalizacji czynności wykonywanych przy przezbrojeniu. Idealnie wpisuje on się w podejście bazujące na wykresie Pareto. Mając do dyspozycji informacje o najbardziej czasochłonnej sekwencji czynności oraz jak często ten moduł jest wykorzystywany w przezbrojeniach, mamy idealny materiał do dalszych prac optymalizacyjnych. Kolejne warsztaty SMED nie wymagają już wykonywania długiego filmu. Wystarczy filmowanie jednego modułu i przeprowadzenie kompletu działań na mniejszej sekwencji czynności. Wprowadzone modyfikacje i tak będą łatwo oddziaływać na wszystkie przezbrojenia, gdzie ten moduł występuje.
W naszych realiach, została zdefiniowana najbardziej czasochłonna czynność, jaką jest wymiana materiału. Wygenerowało to trzy niezależne działania. Pierwsze działanie było związane z pogrupowaniem produktów wg wielkości materiału i przypisaniem do maszyn w celu zmniejszenia liczby długotrwałych przezbrojeń. Kolejne było związane ze zmianą standardu z pracy jednoosobowej na pracę w dwie osoby, czyli realizowanie czynności równolegle – metoda dobrze znana w SMED. Trzecie polegało na próbie ograniczenia różnych przezbrojeń poprzez wprowadzenie EPEI (Every Part Every Interval), co miało dać wymuszenie kolejności przezbrojeń. Działanie to zakończyło się niepowodzeniem ze względu na połączenie 2-ch strategii produkcyjnych w ramach pojedynczej maszyny tj. produkcji na zapas oraz produkcji na zamówienie. Zdobyte doświadczenie pozwoliło nam określić „bramki materiałowe”, czyli czas produkcji różnych detali z materiału o tym samym rozmiarze. Wymagało to korekty stanów magazynowych jednak bez wpływu na średnie stany magazynowe.
Pierwsza standaryzacja przezbrojeń udostępniona w obszarze produkcyjnym miała formę macierzy przezbrojeń. Oczywiście nikt nie wypełniał na początek setek kombinacji dla jednej maszyny. Macierz była wypełniana wstępnie na podstawie bramek materiałowych, czyli najbardziej prawdopodobnych przezbrojeń, jakie mogą się zdarzyć na maszynie. Kolejka ta też jest formą wzorca dla osoby planującej produkcję. Jeżeli wystąpiło niezdefiniowane przezbrojenie, ustawiacz miał prawo podać czynności elementarne wymagane dla danego przezbrojenia i ta wersja została zapamiętana jak pierwszy standard i oznaczona w tabeli, jako wersja do sprawdzenia. Daje to szybkie uruchomienie systemu. Takie podejście daje nam możliwość wystartowania mając zaledwie 10, może 20% wiedzy i przygotowanie systemu samouczącego się, ale w jasno określonym środowisku i na wyraźnie określonych zasadach. W tym systemie zmiany w produkcji są czymś normalnym, a dynamika rynku jest czymś wbudowanym w system i nie budzi żadnych emocji i podlega standardowej obsłudze.
Ewolucja
Kolejny krok został postawiony na maszynach CNC. Po ustandaryzowaniu programów NC, magazynów narzędziowych i wprowadzeniu bazy programów, oraz chwyceniu w ryzy zmian wprowadzanych w programach, doszliśmy do wniosku, że jesteśmy w stanie wygenerować macierz przezbrojeń na postawie standardowych programów. Brzmi to może jak chwila, ale jest to około dwóch lat pracy inżyniera procesu, liderów, oraz kilku ustawiaczy. Mocna standaryzacja naprawdę jest podstawą jakichkolwiek mocniejszych działań optymalizacyjnych. Ideą rozwiązania jest porównanie dwóch programów, a w zasadzie standardów narzędziowych dla konkretnych programów (Rys. 22). Takie porównanie daje możliwość wypełnienia znanej już macierzy przezbrojeń. W skrócie, jeżeli zmienia się materiał między dwoma standardami to znaczy, że wystąpi moduł przezbrojenia „Wymiana materiału”. Takie podejście umożliwiło opracowanie kalkulatora do przezbrojeń. Opisanie standardu produkcji detalu i wcześniejsze ustandaryzowanie sekwencji (modułów) przezbrojeń pozwala na wygenerowanie dowolnych standardów przezbrojenia dla detalu. Standard staje się wynikiem działania algorytmu, nie jest opisywany jednostkowo dla kombinacji detali, jak jest to wykonywane klasycznie.

Rysunek 22 Baza standardów narzędziowych na potrzeby SMED (obszar CNC)
Prowadzone wcześniej działania związane z EPEI materiałowym pozwoliły nam poznać świat klienta i jaki ma on wpływ na liczbę wykonywanych przezbrojeń. Powstały właśnie kalkulator pozwolił wejść w temat głębiej i jeszcze mocniej ograniczyć liczbę niepotrzebnie wykonywanych przezbrojeń, przy zachowaniu realizacji potrzeb klienta. W tym momencie ważne jest postawienie sobie istotnego pytania. Na czym nam tak naprawdę zależy? Czy ważny jest dla nas czas jednego konkretnego przezbrojenia? A, może ważny jest dla nas czas tracony sumarycznie w każdym miesiącu, tygodniu, dniu na wykonywanie czynności przezbrojenia. Nie widzimy różnicy? To, co jest ważne koszt zakupu narzędzia? A może koszt użycia narzędzia na wyprodukowany detal? Oczywiście, że ważny jest koszt, jaki będziemy ponosić z powodu zatrzymywania maszyn na przezbrojenia! To on przyczyni się do wyniku finansowego firmy.
Pierwsze uderzenie poszło w kolejkę produkcyjną. Klient, a w zasadzie klienci układają kolejkę, która przypomina rzut kostkami. Nie ma, co się oszukiwać potrzeby klienta są mocno nie po drodze z potrzebami produkcji. Sprawdziliśmy w takim razie wszystkie możliwe kombinacje, jakie może dać nam kilka zleceń. Ograniczeniem tu jest możliwości wykonywania obliczeń i czasu, jaki możemy poświęcić, czy czekać na wyniki. Kalkulacje wykonaliśmy dla kolejki 9 zleceń, które można ułożyć na 362880 różnych sposobów (permutacja bez powtórzeń P9 = 9!). Sprawdziliśmy wszystkie możliwe kombinacje i ile czasu trzeba będzie poświęcić na wykonanie niezbędnych przezbrojeń. Określony został najlepszy (100%) i najgorszy (0%) plan produkcyjny oraz ustalona została skala do oceny osiągniętej optymalizacji jako „%” uzyskanej oszczędności czasu przezbrojeń. Spodziewaliśmy się rozkładu zbliżonego do normalnego. Ku naszemu zdziwieniu rozkład czasu poświęcanego (traconego) na przezbrojenia nie jest zgodny z rozkładem normalnym. Klient zdecydowanie generuje plany w rozkładzie skośnym (Rys. 23), niestety „na naszą niekorzyść”. Plan wygenerowany przez klienta osiąga „optymalność” na poziomie 20 do 30%, nie jak byśmy oczekiwali w okolicach 50%. Tym bardziej problem stał się intratny do rozwiązania czyli atrakcyjny biznesowo.
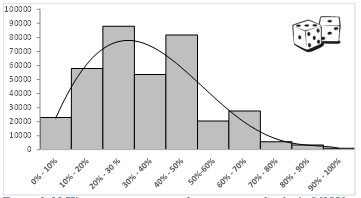
Rysunek 23 Histogram czasu potrzebnego na przezbrojenia 362880 możliwych kombinacji kolejki 9 zleceń produkcyjnych (od najdłuższego czasu przezbrojeń 0% – 0 optymalizacji czasu, do najkrótszego czasu przezbrojeń 100% – pełna optymalizacja)
Teraz wrócimy do multi-dyscyplinarności zespołu. Podstawę pod szukanie rozwiązania dla tego problemu dały zagadnienia z obszaru jakości. Dokładnie to doświadczenia zdobyte przy optymalizacji procesu kontroli statystycznej po procesie mycia. Generalnie zagadnienia te są bardzo zbliżone do tematyki poruszanej przez AQL (Acceptable Quality Limit). Nowa metoda planowania kolejki produkcyjnej opiera się na tej samej losowości, jaką generuje klient. Nie próbujemy szukać planu idealnego. Dla potrzeb próby szukania planu idealnego dla 9 pozycji w kolejce w Excelu zajęło ponad 24h. Losujemy kolejne plany i wykonujemy porównanie do najlepszego aktualnie znanego planu. Jeżeli wylosowany plan jest lepszy to zostaje zapamiętany i staje się planem do kolejnych porównań. Odnalezienie w ten sposób idealnego planu może zająć naprawdę dużo czasu, ale uzyskanie planu w 60% optymalnego to kwestia kilkudziesięciu losowań, a to w realiach zwykłego Excela wspartego VBA kwestia kilkudziesięciu sekund.
Dojście do 80% to kwestia kolejny kilkuset losowań, czyli kilku minut (Rys. 24). Stosując jeszcze dodatkowe warunki do losowania bardzo realne jest otrzymywanie 90% optymalizacji w dość krótkim czasie. Jak komuś 70% redukcji marnotrawstwa nie wystarcza, niech nie korzysta. Przekonywanie go to jak walka o ostatnie 10%, czyli dużo pracy a mało efektu. Zasada Pareto nadal nas obowiązuje.
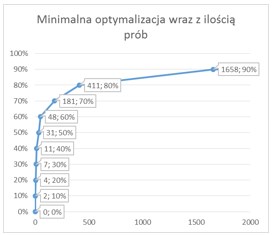
Rysunek 24 Ilustracja procesu losowego poszukiwania kombinacji kolejki zleceń, o coraz krótszym czasie przezbrojeń (w kolejnych punktach podano liczbę wygenerowanych planów produkcyjnych i uzyskany procent skrócenia czasu przezbrojeń znalezionej kombinacji)
Mutacje i adaptacje
Metoda ta została wsparta o doświadczenia ze zdefiniowaniem bramek materiałowych. Polegała ona na zdefiniowaniu grup według najbardziej czasochłonnej czynności i wykonywaniu losowań tylko wewnątrz pojedynczych grup. Jak łatwo się domyśleć im mniej pozycji w planie tym osiągany poziom optymalizacji wyższy. To wydatnie zwiększa skuteczność metody i skraca czas wykonywania symulacji. W tej formie jest używana do planowania produkcji w obszarach montażu. Optymalizacja polega tam na redukcji liczby wymienianych komponentów (elementów składowych finalnego produktu) pomiędzy kolejnymi pozycjami w planie, a co za tym idzie redukcji ilości ruchów wykonywanych prze logistykę i operatorów montażu. Dodatkowo zmniejsza się liczba przezbrojeń związana z kluczami skręcającymi, maszynami pakującymi czy cechowarkami. W tym obszarze, którego charakterystyką jest plan mający minimum kilkadziesiąt różnych referencji w jednym cyklu (tutaj cykl = czas od wysyłki do wysyłki), ważne jest dobre wyszukanie grup według wcześniej wspomnianej czynności najdłuższej. Istotne jest również uwzględnienie kolejnych czynników związanych z liczbą komponentów zużytych do zleceń produkcyjnych i wydłużaniu tychże zleceń, czyli optymalizacji lotu produkcyjnego. To już inny, równie ciekawy i mocno zazębiający się obszar o dużym potencjale optymalizacyjnym, w którym inżynierowie i specjaliści firmy PARKER w Siechnicach prowadzą nadal projekty i zdobywają praktyczne doświadczenie.
PODSUMOWANIE
Jak widać z przedstawionych powyżej przykładów, continuous improvement jest naprawdę procesem ciągłym i niekończącym się. Przed nami ktoś optymalizował produkcję w warunkach, jakie mu dano i po nas też ktoś to będzie robił. Ważne, aby dać pracownikom swobodę działania w dość dużym zakresie i zapewnić motywację. Wszystkie te działania doskonale się wpisują w motto Parkera „ENGINEERING YOUR SUCCESS”, gdzie your dotyczy zarówno Klienta jak również pracownika Parkera.
Autorzy:
Zbigniew Grodzki, Operations manager Parker Hannifin Manufacturing Poland
Grzegorz Lisiecki, Logistic leader Parker Hannifin Manufacturing Poland
Grzegorz Walczuk, Maintenance manager Parker Hannifin Manufacturing Poland
Łukasz Lesiński, Process leader Parker Hannifin Manufacturing Poland
Piotr Wolko, Production development manager Parker Hannifin Manufacturing Poland
Artykuł został opublikowany dzięki uprzejmości i za zgodą firmy Parker Hannifin Manufacturing Poland.