Zarządzanie produkcją typu High Mix – Low Volume w firmie WABCO Polska
WABCO (NYSE: WBC) jest liderem innowacji i globalnym dostawcą technologii poprawiających bezpieczeństwo oraz efektywność pojazdów ciężarowych. Założone prawie 150 lat temu WABCO niezmiennie pozostaje pionierem przełomowych produktów i systemów hamowania, stabilizacji, zawieszenia, automatycznych skrzyń przekładniowych oraz aerodynamiki. Obecnie wszyscy wiodący w skali globalnej producenci samochodów ciężarowych, autobusów i naczep korzystają z technologii WABCO. Ponadto, WABCO dostarcza również zaawansowane rozwiązania do zarządzania flotą samochodową oraz usługi dla rynku wtórnego. WABCO zaraportowało w 2015 roku sprzedaż na poziomie 26 mld dolarów. Firma, której siedziba główna mieści się w Brukseli (Belgia), zatrudnia 12 000 pracowników na całym świecie.
WABCO rozwija swoją działalność w Polsce od 1999 roku, świadcząc usługi na rzecz globalnych klientów i oferując ponad 2000 miejsc pracy w trzech zakładach: przy ulicy Ostrowskiego i Kwiatkowskiego we Wrocławiu oraz w zakładzie regeneracji produktów w Stanowicach koło Oławy. Uzupełnieniem prężnie działającego, największego w WABCO ośrodka produkcyjnego, są zespoły wspierające firmę lokalnie i globalnie, w obszarach: rozwoju produktu, zakupów, logistyki, jakości, zarządzania projektami, BHP, HR, marketingu oraz finansów. WABCO aktywnie współpracuje ze środowiskiem akademickim i lokalnymi władzami, angażując się w rozwój naukowy i gospodarczy Dolnego Śląska.
Więcej informacji znajduje się na stronie internetowej pod adresem www.wabco-auto.com.
Początki historii Lean Management w WABCO Polska
Historia Lean Managament w WABCO Polska sięga roku 2005, kiedy to wrocławski zakład stanął przed koniecznością rozbudowy istniejących hal produkcyjnych. Powodem takiej sytuacji był dynamiczny rozwój obszaru produkcji związany z licznymi transferami nowych linii produkcyjnych. We wcześniejszych latach WABCO Polska było zarządzane metodami „tradycyjnymi”, więc w tamtym czasie jedynym rozwiązaniem wydawał się zakup ziemi i postawienie nowej hali produkcyjnej obok dwóch już istniejących.
Jednak w 2005 w grupie WABCO pojawił się Pratip Dastidar, wiceprezydent ds. jakości. Jedną z jego pierwszych decyzji było zorganizowanie w WABCO Polska tzw. Lean Baseline Assessmentu, który miał ujawnić rzeczywiste problemy i możliwości poprawy sytuacji zakładu. Jako że głównym problemem biznesowym był brak miejsca, szczególną uwagę skupiono na kwestii wykorzystania powierzchni produkcyjnej. W wyniku przeprowadzonych warsztatów okazało się, że jedynie 20% powierzchni operacyjnej (Rys. 1) stanowiły linie produkcyjne (zaznaczamy, że zakład we Wrocławiu ma charakter produkcyjny). Pozostałe 80% wykorzystywane było jako zaplecze procesów produkcyjnych (głównie: drogi transportowe, regały, pola odkładcze z materiałem etc.).
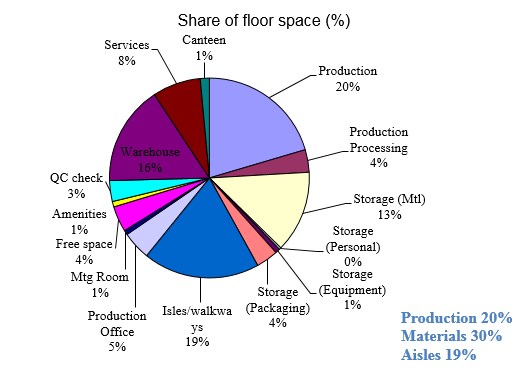
Rysunek 1 Rozkład przeznaczenia powierzchni operacyjnej w WABCO Polska w 2005 roku
Po tym wydarzeniu WABCO Polska zostało w ramach globalnej organizacji WABCO wybrane jako pilotażowa fabryka do wdrożenia rozwiązań szczupłej produkcji.
Dlaczego WABCO zdecydowało się wybrać Lean Management jako nową ścieżkę rozwoju? Pratip Dastidar powiedział krótko: „Po co wymyślać koło na nowo?”. Sukces Lean w innych przedsiębiorstwach stanowił najlepszy dowód tego, że warto iść tą drogą.
W związku z tym, że w pierwszej kolejności trzeba było odzyskać powierzchnię produkcyjną, wysiłki skierowano na ten obszar. Kluczowym elementem miały się tutaj stać tzw. linie wieloasortymentowe (mix-model lines). Ich istota polega na możliwości produkowania różnych rodzin wyrobów w tym samym gnieździe, na tych samych stanowiskach i na tym samym lub szybko przezbrajanym oprzyrządowaniu. Linie mixed-model stanowiły rewolucję nie tylko w zakresie filozofii wytwarzania (jedna linia – wiele wyrobów), ale także w odniesieniu do konstrukcji linii i logistyki. Ich najważniejsze cechy to:
- możliwie najlżejsza konstrukcja,
- minimalizacja rozmiarów / maksymalizacja proporcji „part-to-table”,
- jednokierunkowy przepływ materiału,
- brak wyizolowanych wysp,
- zasilanie w materiał oraz system zwrotny na puste opakowania z tyłu linii,
- uniwersalne lub łatwo przezbrajalne gniazda i stanowiska,
- balans pracy umożliwiający przepływ jednej sztuki,
- zasilanie materiałowe bezpośrednio z magazynu centralnego lub z regału przepływowego/supermarketu (zgodnego z zasadami kanban).
Pierwszy pilot odbył się w 2006 na liniach S2 (Simple & Small). Dzięki projektowi udało się 15 konwencjonalnych gniazd produkcyjnych i jedną skomplikowaną i zautomatyzowaną linię Prodel scalić (Rys. 2) w 3 zintegrowane linie mix-model (S2).
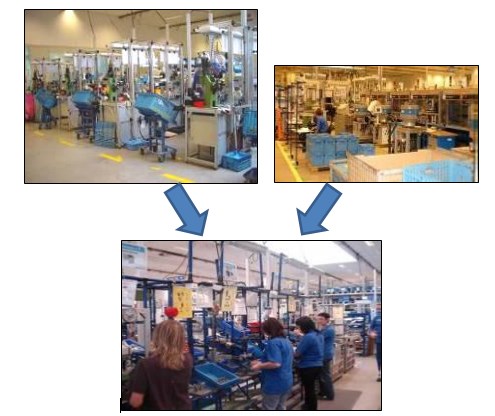
Rysunek 2 Scalenie 15 konwencjonalnych gniazd produkcyjnych i zautomatyzowanej linii Prodel w 3 zintegrowane linie mix-model
Na przestrzeni 2 lat stworzono grupę projektową, która opracowała koncepcję Linii Modelowej, przygotowała projekt linii jak również wdrożyła i przeszkoliła pracowników na nowych miejscach pracy (Rys. 3).
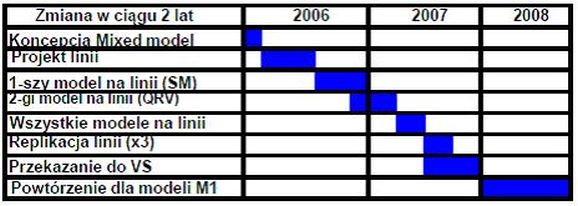
Rysunek 3 Plan opracowania i wdrożenia linii mix-model w WABCO Polska
Pierwszy projekt linii modelowej zakończył się spektakularnymi wynikami, ponieważ czas przejścia wyrobu przez linię (lead time) udało się skrócić z 30 do 3 minut. Dodatkowo stworzenie linii mix-model wpłynęło na inne kluczowe wskaźniki wyników (KPI), dając wymierne korzyści w aspektach jakościowych, logistycznych i finansowych (Tab. 1).
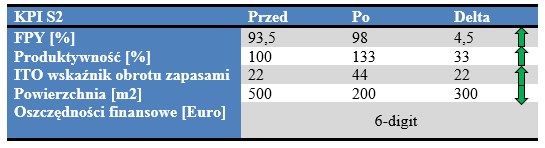
Tabela 1 Poprawa wybranych kluczowych wskaźniki wyników dzięki pierwszemu projektowi wdrożenia linii mix-model w WABCO Polska w 2006
Metodyka projektowania i wdrażania linii typu mix-model w WABCO Polska
Po sukcesie pierwszych linii mix-model postanowiono poszukać kolejnych potencjalnych linii do usprawnień i punktów do poprawy. W 2009 roku rozpoczęto projekt piątej linii mix-model REV 1-5 na obszarze VS-TS w WABCO Polska. Na etapie analizy zauważono wysoki potencjał do wzrostu wydajności i poprawy:
- Produktywności,
- FPY,
- ITO (wskaźnik obrotu zapasami),
- Fill Rate,
- Zdolności wytwórczych,
- Bezpieczeństwa,
- Jakości.
Projekt stał się bazą dla sposobu standaryzacji transformacji mix-model dzięki zastosowaniu takich elementów jak: Zarządzanie wąskim gardłem, TPM, praca standaryzowana, tablica z harmonogramem produkcji, PFEP (Plan For Every Part) i wdrażanie innych narzędzi Lean.
Pierwszym krokiem było wyznaczenie tempa, z jakim nowa linia musi pracować, aby spełnić oczekiwania klienta. W tym celu zebrano informacje o prognozach zamówień na pięciu pierwotnych liniach celem określenia nowego czasu taktu dla linii REV MIX MODEL. Wynik ten wyznaczył i zdefiniował ilość stanowisk, które muszą zostać zaprojektowane w nowej linii.
Kolejnym krokiem było stworzenie tzw. mock up, czyli kartonowej symulacji 3D dla nowej linii, w skali 1:1, aby wiernie oddać i zaplanować layout linii oraz zobrazować prezentacje części na stanowiskach (Rys. 4).
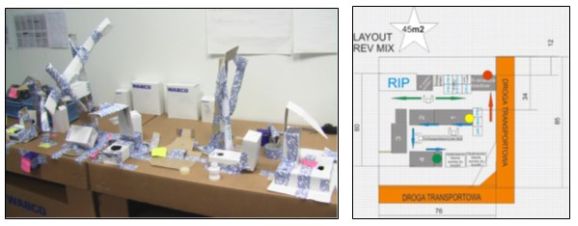
Rysunek 4 Mock up, czyli kartonowy model stanowisk linii REV MIX MODEL w skali 1:1 oraz projektowany layout tej linii.
Mając już zaprojektowaną linię i wyznaczony czas taktu dla tzw. stymulatora strumienia wartości, rozpoczęto prace nad częścią logistyczną tj. wyznaczeniem możliwego EPEI (Every Part Every Interval) – przedziału czasu, w jakim proces może wytworzyć wszystkie typy produkowanych wyrobów (Rys. 5), czyli wskaźnika informującego, jak często możliwe jest wytworzenie każdego spośród produkowanych typów (miernik powtarzalności cyklu produkcyjnego w przyjętym okresie).
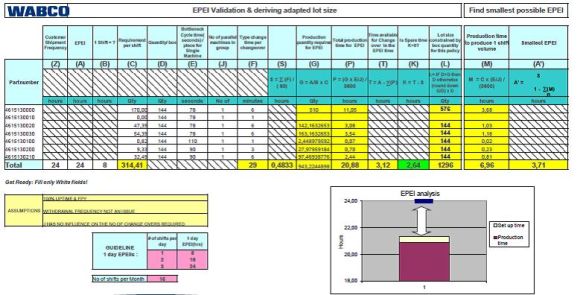
Rysunek 5 Przykład wyznaczania wskaźnika EPEI – najmniejszego przedziału czasu, w jakim proces może wytworzyć wszystkie typy produkowanych wyrobów
Znajomość wskaźnika EPEI pozwoliła na ustalenie możliwej liczby przezbrojeń i określiła ich maksymalny czas trwania. Aby móc sprostać takiej liczbie przezbrojeń i uniknąć możliwości popełnienia błędu, stworzono tzw. koło przezbrojeń (Pattern Wheel). Pozwala ono na optymalne przejście z jednego produkowanego wyrobu na drugi w sekwencji, która sprawia, że czas przezbrojenia jest najmniejszy z możliwych przy obecnym stanie wiedzy (Rys. 6). Unika się dzięki temu zbędnej straty czasu na przezbrajanie pomiędzy różnorodnymi, znacząco innymi od siebie wyrobami gotowymi, jeżeli chodzi o konstrukcję, a co za tym idzie, ilością komponentów potrzebnych do wyprodukowania.
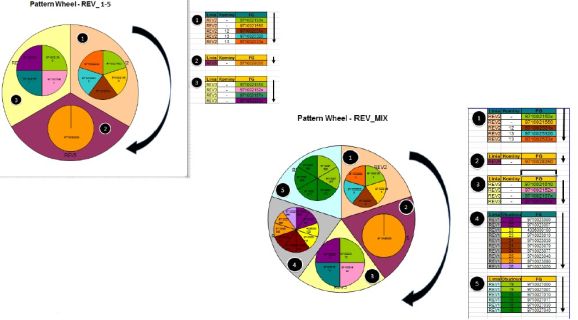
Rysunek 6 Koło przezbrojeń (Pattern Wheel) dla linii REV MIX MODEL
Ostatnim finalnym elementem systemu jest stworzenie odpowiedniego balansu pracy operatorów na linii. W tym celu dokonywany jest podział całej zawartości pracy na linii pomiędzy operatorów; następnie dodaje się czasy poszczególnych operacji i zabiegów przydzielonych operatorom i tworzy tzw. wykres Yamazumi (Rys. 7).
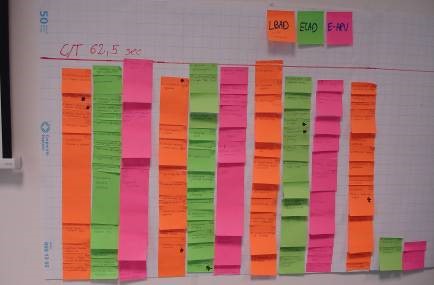
Rysunek 7 Przykładowy wykres obciążenia pracą operatorów na linii (jap. Yamazumi)
Wykresy Yamazumi wspomagają znajdowanie optymalnego zbalansowania pracy operatorów i maszyn tak, aby linia pracowała jak najbardziej efektywnie. Balans pracy pozwala również na stworzenie odpowiednich tabel kombinacji pracy. Dane te są podstawą do opracowania karty pracy standaryzowanej (Rys. 8), na której przedstawia się aktualnie najlepszą sekwencję pracy i standardowy zapas w toku (WIP). Niezbędne jest ustalenie wielkości supermarketu i ilości kanbanów krążących w pętlach.
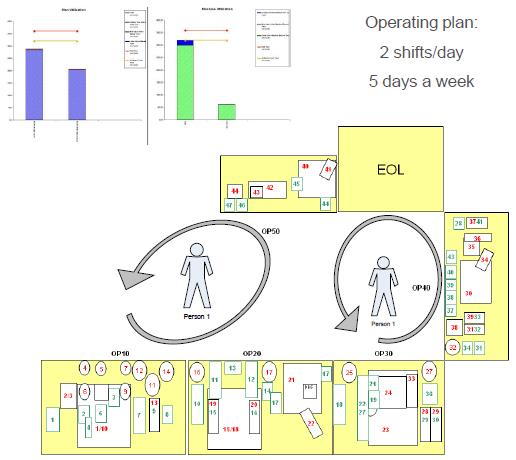
Rysunek 8 Przykładowa karta pracy standaryzowanej
Dodatkowo, aby skrócić czas przezbrojenia przeprowadzono warsztaty SMED, których wynikiem było obniżenie czasu przezbrojenia do 10 minut dla różnych rodzin i poniżej 1 minuty dla różnych wyrobów w obrębie tej samej rodziny.
Funkcją wspierająca jest również Water Spider, który oprócz zaopatrywania linii w komponenty bierze udział w przezbrojeniu, przygotowując przed przezbrojeniem odpowiednie komponenty, potrzebne do realizacji nowego zlecenia produkcyjnego. Projekt linii REV MIX MODEL oprócz redukcji miejsca (Rys. 9) przyczynił się do poprawy innych wskaźników (Tab. 2).
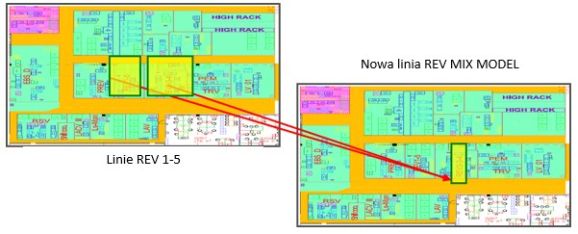
Rysunek 9 Redukcja powierzchni uzyskana dzięki wprowadzeniu linii REV MIX MODEL
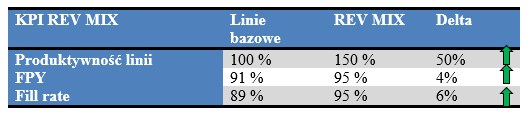
Tabela 2 Porównanie wybranych wskaźników dla produkcji rodzin wyrobów przed i po wprowadzeniu linii REV MIX MODEL
Projekt linii mix-model okazał się krokiem milowym i wielkim sukcesem w procesie transformacji Lean w zakładzie WABCO Polska. Pozytywne wyniki przełożyły się na:
- Poprawę produktywności w produkcji wieloasortymentowej (procesy manualne i półautomatyczne),
- Zwiększenie zdolności produkcyjnych procesów maszynowych i zautomatyzowanych,
- Optymalizację layoutu z uwzględnieniem redukcji czasów przejścia i zapasów międzyoperacyjnych,
- Poprawę dostępności na czas komponentów od dostawców oraz produkowanych wewnętrznie,
Obecnie prawie 25% produkcji wytwarzane jest w WABCO Polska na liniach mix-model. Wszystkie nowe linie są projektowane jako rozwiązania mix-model ponieważ dają dużą elastyczność produkcji pozwalając sprostać oczekiwaniom Klientów.
Podział linii produkcyjnych na wysoko- i niskowolumenowe z wykorzystaniem metody sita Glendaya
CB2 jest jednym ze strumieni wartości zlokalizowanych w zakładzie WABCO Polska. Jest to specyficzny obszar produkcji, którego indywidualny charakter wynika z dużych gabarytów produkowanego tam wyrobu – siłownika. W 2010 roku obszar ten borykał się z problemem ciągłej pracy w nadgodzinach w weekendy przy 3-zmianowym systemie operacyjnym. Kolejnym mankamentem był fakt, iż obszar nie miał prawidłowo zdefiniowanego czasu taktu, balansu linii i, w konsekwencji, technicznych zdolności produkcyjnych.
To wszystko prowadziło do niskiej efektywności produkcji (rzeczywista liczba produkowanych sztuk < 50% technicznych zdolności produkcyjnych) i wysokiego kosztu wytworzenia produktu oferowanego na mocno konkurencyjnym rynku.
Diagnoza wykonana na Gemba pokazała, że możliwe są 3 kierunki działań:
- Eliminacja procesów o długim czasie cyklu (leżakowanie siłowników i czas schnięcia tłoków),
- System ssący na komponenty malowane,
- Podział linii na wysoko- i niskowolumenowe z wykorzystaniem narzędzia tzw. sita Glendaya, które dzieli cały asortyment wyrobów na 4 grupy: zielony, żółty, niebieski i czerwony w zależności od wielkości ich sprzedaży.
Najważniejszym scenariuszem okazało się podzielenie linii na wysoko- i niskowolumenowe (ze względu na potrzeby, czas wdrożenia, koszty, efekty).
Wypracowanie nowego przepływu materiałów opierało się na podziale (Rys. 9) na dwie linie wysokowolumenowe (40% wolumenu, długie zlecenia, niewymagane duże ilości przezbrojeń) i jedną linię niskowolumenową (60% wolumenu obejmującego wyroby żółte, niebieskie, czerwone).
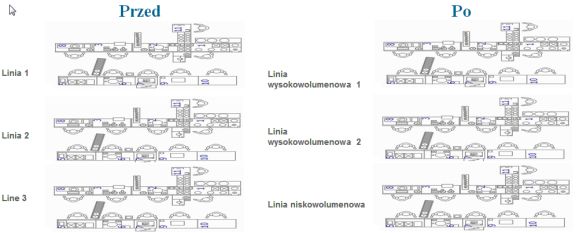
Rysunek 9 Podział linii produkcyjnych na 2 linie wysokowolumenowe (produkujące wyroby zamawiane w dużych ilościach) i 1 linię niskowolumenową (produkującą pozostałe wyroby)
Konsekwencją upływu czasu i wzrostu zamówień było podjęcie decyzji o zakupie nowej linii do produkcji siłowników. W związku z tym zmieniono też podział linii na wyroby wysoko- i niskowolumentowe. Nowo zakupiona linia wraz z jedną już istniejącą zostały liniami wysokowolumenowymi. Planowanie na tych liniach odbywa się tylko w strumieniu zielonym. Druga linia z wysokowolumenowych stała się linią dla strumieni żółtych i niebieskich. Ostatnia linia natomiast obsługuje tylko strumień czerwony.
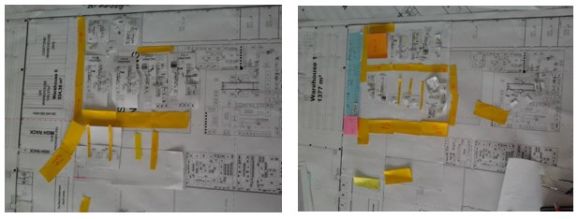
Rysunek 10 Planowanie zmian layoutu celem zainstalowania nowej linii produkcyjnej
Dodatkowo nowy transfer wymagał zmiany layoutu i pracy nad nowym przepływem materiału (Rys. 10).
Cały obszar siłowników zostały przeniesiony w nowe miejsce. Zorganizowano kolejny warsztat, który skupił się na przepływnie materiału oraz obsłudze linii nisko i wysokowolumenowych. Podjęto decyzję o obróceniu magazynu o 90 stopni, aby skrócić możliwie dostarczanie części do linii. Rysunek 11 przedstawia przepływ materiału przed i po obróceniu magazynu.
Do lini wysokowolumenowej materiał dostarczany jest w pełnych opakowaniach. Materiał zużywany jest w całości, co nie generuje zwrotów części na magazyn.
Linie niskowolumenowe zaopatrywane są w części wcześniej kompletowane. Przygotowywane są gotowe zestawy części pod plan produkcyjny. Dzięki zmianie layoutu w tym obrócenia magaznu i zastosowaniu sita Glendaya udało się stworzyć warunki do redukcji kosztów wytwarzania. Poczynione kroki doprowadziły do:
- Zwiększenia wydajności produkcji o 25%.
- Mniejszej ilości przezbrojeń na liniach wysokowolumenowych
- Spadek obciążenia pracą:
- 45% mniej zabiegów manipulacyjnych niedodających wartości,
- 70% krótszy dystans, który przemierza materiał, gdy nie jest do niego dodawana wartość.
Trwają prace nad zautomatyzowaniem systemu zamawiania kolejnych zleceń produkcyjnych. Trwają również prace nad zautomatyzowaniem procesu kompletowania części i podstawiania pod linię oraz synchronizacji planów produkcji dla magazynu, która przy wielowariantowości na naszych obszarach jest nieunikniona.
Katarzyna Kaczmarek – Lean Project Leader, WABCO Polska
Patryk Szatkowski – Lean Project Leader, WABCO Polska
Artykuł stanowi przedruk publikacji zamieszczonej w materiałach konferencyjnych XVI Konferencji Lean Management, która odbyła się we Wrocławiu w dniach 7-9 czerwca 2016 roku. Konferencja, która organizowana jest corocznie przez Lean Enterprise Institute Polska, przeznaczona jest dla sektorów produkcyjnego i usługowego. Zapraszamy do odwiedzenia obszernego serwisu internetowego poświęconego Konferencji pod adresem www.leankonf.pl.
Artykuł został opublikowany dzięki uprzejmości i za zgodą firmy WABCO Polska.