Stratom mówimy NIE – przykład wdrożenia w polskim przedsiębiorstwie
Pilotażowe wdrożenie metody Eco Lean (przeczytaj o metodzie klikając TUTAJ, a także o wdrożeniu w tureckiej firmie klikając TUTAJ) odbyło się w polskiej firmie Gaweł Zakład Produkcji Śrub, specjalizującej się w produkcji elementów złącznych takich jak: wkręty do drewna, metalu, tworzywa sztucznego. Firma ta dostarcza produkty dla wielu międzynarodowych korporacji z branży AGD, elektronicznej, budowlanej, motoryzacyjnej oraz meblowej.
Pierwszym etapem pracy było przygotowanie Mapy Eco Orbit View, gdzie zidentyfikowano główne etapy procesu produkcyjnego, które wchodziły w zakres analizy, czyli:
- tłoczenie,
- walcowanie,
- hartowanie.
Firma posługuje się wskaźnikami wydajności, z których najważniejsze to realizacja planu produkcyjnego i ilość defektów jakościowych. W trakcie wizyty w obszarze hartowania zauważono także problem z awariami, których fabryka w tym obszarze nie monitorowała poprzez ustalony wskaźnik. Z tego też powodu aspekt ten dodano do Mapy Eco Orbit View jako Kluczowe Wyzwanie Biznesowe.
Z ekologicznego punktu widzenia – fabryka śledzi zużycie energii i wody dla poszczególnych budynków (które są rozmieszczone w kilku różnych lokalizacjach) bez dokładnej informacji o zużyciu w poszczególnych procesach. W trakcie Gemba Walk zdiagnozowano, iż aspekty ekologiczne z całą pewnością są istotne dla organizacji i mają wpływ na wskaźniki biznesowe. Widać to wyraźnie na wizualizacji Mapy Eco Orbit View. Dla każdego z procesów wyszczególniono główne wskaźniki biznesowe (KPI) i środowiskowe (KEPI).
W ramach drugiego etapu jakim jest Macierz Wyboru zidentyfikowano powiązania pomiędzy wskaźnikami biznesowymi i środowiskowymi. Każdy z nich oznakowano zgodnie z informacjami zawartymi w legendzie.
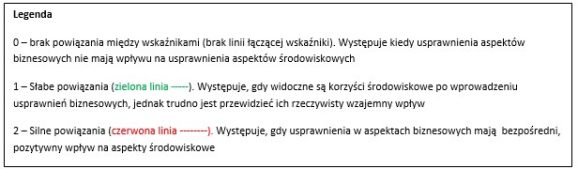
Rys. 1. Wizualizacja Mapy Eco Orbit View oraz Macierzy Wyboru
Dokonując przeglądu powyższych danych łatwo zauważyć, iż im większe rozbieżności między zaplanowaną a zrealizowaną produkcją tym wyższe zużycie energii, wody i gazu. Ponadto można zaobserwować ścisłą korelację pomiędzy ilością defektów jakościowych a stratami stali i ilością odpadu. Każde z tych powiązań ma charakter silnej synergii, w której łatwo odnaleźć wzajemny wpływ. Kończąc ten etap wyróżniono dwa procesy, które zostały poddane dalszemu badaniu w ramach analizy obszaru: Hartowanie i Tłoczenie.
Analiza obszaru w procesie Hartowania
Szczegółowe dane analizowano dla największego z 8 pieców, różniących się między sobą wielkością, budową i wydajnością. Na podstawie danych z okresu sierpień 2014 – sierpień 2015 roku, można dostrzec, iż największy wpływ na wydajność tego procesu miały awarie pieców.
Synergia dla dwóch aspektów (awarie i zużycie energii elektrycznej) została podczas Eco Orbit View wskazana jako silna ponieważ piece nie są wyłączane na czas awarii, ze względu na zbyt długi czas i koszt ich ponownego uruchomienia. Rzeczywisty poziom zużycia energii podczas awarii można zaobserwować na rys. 2.
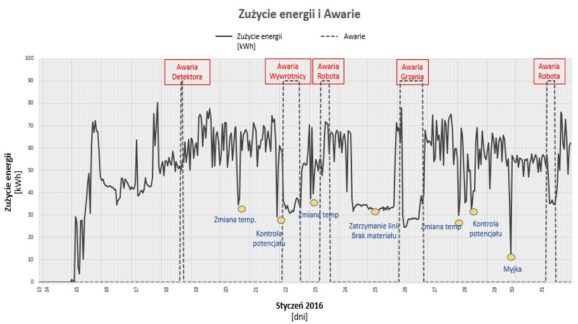
Rys. 2. Wykres zużycia energii elektrycznej
W oparciu o zebrane dane oszacowano, iż organizacja traci 10% energii na skutek podtrzymywania temperatury pieca w trakcie awarii.
W celu redukcji ilości awarii, a co za tym idzie redukcji straty energii elektrycznej zaproponowano wdrożenie narzędzia Lean jakim jest TPM (Total Productive Maintenance).
Według Masaaki, organizacje, które wdrożyły TPM potrafią zredukować ilość awarii o 80-90% a koszty defektów jakościowych o 55% [1]. W oparciu o te dane oszacowano roczne oszczędności energii elektrycznej dla wszystkich 8 pieców, które mogą osiągnąć nawet 200 MWh (co przekłada się na oszczędności finansowe rzędu 79 105,40 PLN), gdyby wdrożone usprawnienia osiągnęły swój maksymalny poziom.
Analiza obszaru w procesie Tłoczenia
Do analizy obszaru wybrano dwie kluczowe maszyny (T14 i T29) przeznaczone do tłoczenia łba śruby. Każde opóźnienie w tym procesie przekłada się na opóźnienia we wszystkich pozostałych. Największym problemem dla obu maszyn był długi czas przezbrojeń trwający od 3 do 24 godzin – w zależności od konfiguracji asortymentowej. Aby usprawnić ten proces zaproponowano wdrożenie narzędzia SMED. SMED to czteroetapowa metoda wykorzystywana do redukcji czasu przezbrojenia maszyny z jednego formatu na inny. Skrócenie tego czasu ma pozytywny wpływ na dostępność maszyn do produkcji i ograniczenie zużycia energii. Przystępując do wdrożenia SMED pracownicy uczestniczyli w warsztatach, przygotowujących ich do późniejszego zadania. W ramach projektu operatorzy zaproponowali:
- rozdzielenie aktywności zewnętrznych, które mogą być wykonane w czasie gdy maszyna jeszcze pracuje i wewnętrznych wykonywanych w trakcie postoju maszyny (etap 1),
- wyróżnienie aktywności, które wykonuje operator na innych maszynach (etap 1),
- zamianę aktywności wewnętrznych na zewnętrzne (etap 2),
- zmianę sposobu przygotowania stanowiska pracy m.in. przygotowanie wózka ze wszystkimi potrzebnymi narzędziami (etap 3),
- zmianę sposobu pracy. Jak pokazała analiza największą stratą jest konieczność jednoczesnego wykonywania przezbrojenia i obsługi innej maszyny przez tego samego operatora. Aby zoptymalizować ten proces przygotowano scenariusze działań w zależności od ilości dostępnych operatorów, ilości przezbrojeń do wykonania oraz maszyn do obsługi. Ten zabieg pozwolił skrócić czas przezbrojenia o 45% (etap 4),
- wdrożenie zasad 5S oraz nowych instrukcji i standardów pracy (etap 4).
Całkowita redukcja czasu przezbrojenia uzyskana w projekcie to 63% czasu wyjściowego. Zwiększając dostępność maszyn, fabryka zwiększyła swoją wydajność o 14,7 % w opisanym obszarze pilotowym, jednocześnie redukując ilość nadgodzin i konieczność pracy w weekendy.
Kierownictwo fabryki planuje realizację dalszych usprawnień zaproponowanych w trakcie warsztatów i wdrożeń mając nadzieję na osiągnięcie jeszcze lepszych wyników w przyszłości.
Powyżej opisane studium przypadku jest częścią serii artykułów, w których przedstawiono metodę Eco Orbit View oraz wdrożenia w polskim i tureckim przedsiębiorstwie.
Autorzy:
Agnieszka Fonfara, Project Expert LEI Polska
Katarzyna Skornowicz, Specjalista ds. projektów badawczych i przemysłowych, LEI Polska
Projekt dofinansowany ze środków Narodowego Centrum Badań i Rozwoju w ramach Programu ERA-NET Eco-Innovera na podstawie umowy Nr ERA-NET-ECO-INNOVERA2/2/2014.