Wpływ narzędzi digitalizacji realizujących koncepcję Przemysłu 4.0 na zarządzanie procesem produkcyjnym
Żyjemy obecnie w erze cyfryzacji i robotyzacji. Codziennie słyszymy o wynikach prac centrów rozwojowych prywatnych firm lub uczelni technicznych, które coraz lepiej radzą sobie ze zarządzaniem sztuczną inteligencją wprowadzając ją w codzienne życie w postaci wyspecjalizowanych robotów lub usług. W krajach najbardziej rozwiniętych technologiczne powstają inteligentne miasta tworzące zintegrowane rozwiązania dla mieszkańców i ich gości. Z łatwością znajdujemy hotel, połączenia komunikacyjne, możemy zdalnie zaplanować wizyty w muzeach czy uczestniczyć w wydarzeniach poprzez transmisje na żywo. Dzięki rozwiniętej sieci komputerowej i telefonii smartphonowej gromadzone są ogromne ilości danych na nasz temat, które tworzą tzw. Big Data analizowane przez wyspecjalizowane centra analityczne. Mamy wówczas do czynienia z tzw. Internetem Rzeczy IOT (ang. Internet of Things) gdzie w nieprzewidywany przez nas sposób informacje, które nas interesują same wpadają nam na strony internetowe podczas ich przeglądania. Internet poznaje nasze przyzwyczajenia i podpowiada nam jak sobie radzić w codziennych problemach.
Powyższe rozwiązania są stosowane w przemyśle pojedynczo lub w zintegrowany sposób. Były one początkowo znane pod nazwą rozwiązań typu MES (Manufacturing Execution Systems), które umożliwiały zbieranie danych z procesów produkcyjnych w czasie rzeczywistym. Obecnie najbardziej rozpowszechnioną nazwą jest Przemysł 4.0 (ang. Industry 4.0).
„Zasięg tej zmiany jest dużo bardziej rozległy: dotyczy ona nas wszystkich. Jest także głębszy, gdyż wnika w znaczącą część codziennego życia”.
„The Fourth Industrial Revolution” Klaus Schwab, 2016
Poniżej przedstawiam podstawowe informacje dotyczące tematyki Industry 4.0, które zapożyczyłem z materiałów ogólnodostępnych znajdujących się w intrenecie. Pozwolą one przybliżyć Państwu to zaganianie.
Co to jest Industry 4.0?
Przemysł 4.0 jest zbiorczym określeniem dla innowacji technicznych oraz koncepcji organizacji łańcucha wartości, które zmieniają produkcję przemysłową w rewolucyjny sposób. Termin (z niemieckiego Industrie 4.0) pochodzi z projektu strategii przemysłu wysokiej techniki opracowanej przez rząd Niemiec. Promuje ona komputeryzację procesów wytwórczych. Hasło zostało po raz pierwszy użyte na targach w Hanowerze w roku 2011. Dlaczego 4.0?
Według szacunków mamy dzisiaj około 50 mld urządzeń w sieci – do roku 2050 będzie ich około 500 miliardów. Mamy urządzenia smart, powstają samochody smart, w Korei Południowej powstało Songdo, pierwsze smart miasto. Aby wszystko to powstało, potrzebna jest jednak smart factory, a więc przedsiębiorstwo w dużym stopniu oparte o aktywa cyfrowe. Przemysł 4.0 to połączenie bardzo rozwiniętej cyfryzacji oraz oprogramowania uczącego się, które daje możliwości dotychczas niezapewniane przez tradycyjne algorytmy i systemy. Przed biznesem otwierają się zupełnie nowe sposoby organizacji.
Kamienie milowe rewolucji przemysłowych (Rys. 1):
- Przemysł 1.0 – mechanizacja. Wynalezienie silnika parowego wprowadziło produkcję w erę industrializacji.
- Przemysł 2.0 – Elektryczność wyparła silniki parowe. Linie produkcyjne po raz pierwszy umożliwiły wytwarzanie towarów w dużych seriach. Za pierwszą uważana jest linia przetwórstwa mięsnego w Cincinnati, uruchomiona w 1870 roku. Najbardziej znaną jest natomiast linia produkcyjna stworzona przez Henry’ego Forda w 1913 roku.
- Przemysł 3.0 – automatyzacja i robotyka. Wprowadzenie programowalnego sterownika logicznego Modicon 084 w 1969 roku otworzyło erę automatyki przemysłowej, zapoczątkowując tym samym trzecią rewolucję przemysłową. Zastosowanie sterowników PLC, oprogramowania przemysłowego (SCADA, ERP, MES) oraz robotów przemysłowych pozwoliło na pełną kontrolę przebiegu procesu produkcji w zakładzie. Bardziej wydajne procesory umożliwiły sterowanie maszynami za pomocą oprogramowania. Dzięki temu maszyny zyskały większą wydajność, precyzję i elastyczność, a proces cyfryzacji umożliwił osiągnięcie coraz wyższych stopni automatyzacji. Zaczęły powstawać systemy planowania i kontroli, których celem była koordynacja działań w obrębie produkcji.
Każda rewolucja przemysłowa była napędzana przez surowce, takie jak węgiel, stal, ropę, elektryczność. Dzisiaj będą to dane. Aby stworzyć przewagę konkurencyjną, każda firma musi znaleźć sposób na wykorzystywanie ogólnodostępnych danych do własnych celów. Właściwe dane, we właściwym czasie, mogą generować dodatkową sprzedaż, redukować koszty operacyjne, poprawiać wyniki operacyjne.
Przemysł 4.0
Oznacza tworzenie sieci (networking). Przemysł 4.0 należy traktować jako zagadnienie ewolucyjne, związane z cyfryzacją produkcji i zmianami biznesowymi. Na pewno nie chodzi tu o wymianę parków maszynowych, a raczej o wdrażanie rozwiązań pozwalających na zbieranie danych, ich analizę, a następnie optymalizację procesów. Pojęcie Przemysłu 4.0 oznacza unifikację świata rzeczywistych maszyn produkcyjnych ze światem wirtualnym, technologii informacyjnej i przetwarzania danych. Ludzie, maszyny oraz systemy IT automatycznie wymieniają informacje w toku produkcji – w obrębie fabryki oraz w obrębie różnych systemów IT działających w przedsiębiorstwie. Przemysł 4.0 obejmuje cały łańcuch wartości: od złożenia zamówienia i dostarczenia komponentów dla trwającej produkcji, aż do wysyłki towaru do klientów i usług posprzedażnych. Cyfryzacja i wprowadzanie nowych technologii same w sobie nie są celem. To narzędzia służące do zmiany modeli biznesowych na takie, które pozwalają utrzymać konkurencyjność na rynku. W przypadku przedsiębiorstw produkcyjnych cyfryzacja umożliwia pojawienie się „inteligentnych” systemów zarządzania produkcją opartych na komunikacji online pomiędzy elementami procesu produkcyjnego i zaawansowanej analizie danych (systemy typu SCADA, MES).
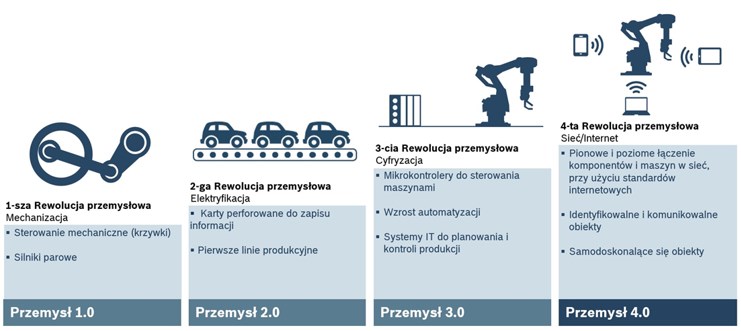
Rys. 1 Cztery rewolucje przemysłowe
Dwa filary
Przemysł 4.0 posiada dwa filary. Pierwszym jest „Internet Rzeczy” (z ang. IoT, Internet of Things) pozwalający na globalny dostęp do danych oraz maszyn. Drugim jest „inteligencja maszynowa” zakładająca pełną autonomizację procesów produkcyjnych, wliczając w to organizację produkcji oraz reakcję na zmiany zapotrzebowania rynku na produkt o konkretnych parametrach. Pod pojęciem „Internetu Rzeczy” kryją się technologie umożliwiające podłączenie dowolnego urządzenia do Internetu, a także możliwość zarządzania nim z każdego miejsca z dostępem do Internetu. Dotyczy to zarówno urządzeń, z których korzystamy na co dzień, takich jak: sprzęty domowe, telefony, zegarki, jak i maszyn oraz technologii działających w fabrykach. W ujęciu przemysłowym zjawisko to określane jest jako Przemysłowy Internet Rzeczy, ang. Industrial Internet of Things (w skrócie IIoT).
Zalety Przemysłu 4.0
- Dzięki usieciowieniu produkcji, przedsiębiorstwa mogą produkować bardziej ekonomicznie i szybciej reagować na indywidualne potrzeby klientów – większa automatyka i robotyka, poprawa produktywności.
- Tworzą się nowe miejsca pracy skupione wokół automatyki i IT oraz nowych branż związanych m. in. ze współpracą robotów z ludźmi, serwisy.
- Dane są dostępne w każdej chwili, na ich podstawie podejmuje się działania oparte o bieżące wyniki. Dane i informacje to podstawa konkurencyjności firm.
- Narzędzia produkcyjne mogą (w większości przypadków) same modyfikować swoje działanie, przystosowując się do nowych wyzwań – wystarczy zastosować odpowiednie polecenie programu do obsługi maszyn. Polecenie automatycznie włącza także moduły potrzebne do wykonania danego procesu i wyłącza te już niepotrzebne. Dzięki temu producenci mogą realizować zamówienia nisko seryjne, a nawet produkować pojedyncze sztuki po kosztach standardowej produkcji seryjnej. Oznacza to zwiększenie wydajności produkcji, ponieważ wszelkie przypadki obniżania efektywności oraz marnotrawstwa są wykrywane, dzięki większej przejrzystości łańcucha wartości, a to z kolei umożliwia producentowi zdobycie decydującej przewagi konkurencyjnej.
- Poprawa jakości: bieżące dane jakościowe on-line, statystyki procesowe dostępne w każdej chwili (typu raporty wad, SPC).
- Poprawa dostępności maszyn, redukcja awarii poprzez ciągły monitoring oraz rozwój technik predykcyjnych (reagowanie na anomalie przed wystąpieniem awarii).
- Optymalizacja pracy serwisów, skrócenie czasu reakcji. Serwisanci będą zatem w stanie zdalnie i proaktywnie identyfikować potencjalne usterki i zamawiać części z wyprzedzeniem. Dokonując przeglądu i naprawy, wyposażeni w rozwiązania rozszerzonej rzeczywistości (np. tzw. smart glasses), będą w stanie otrzymać instrukcje od ekspertów znajdujących się z dala od miejsca naprawy.
- Poprawa warunków pracy, BHP poprzez przekazywanie uciążliwych, monotonnych, niebezpiecznych prac robotom przemysłowym lub robotom kolaboratywnym (współpracującym z pracownikami).
- Racjonalne użytkowanie materiałów i poprawa efektywności energetycznej idą w parze ze zrównoważonym rozwojem.
W związku z tym Przemysł 4.0 pozwala tworzyć nowe modele biznesowe. Wyzwanie polega na dostrzeżeniu tych nowych modeli i jak najszybszym ich wdrożeniu oraz skoncentrowaniu się na wykorzystaniu korzyści ekonomicznych, jakie oferują.
- Dziewięć technologii zmieniających produkcję przemysłową wg Boston Consulting Group
W Saint-Gobain Sekurit Innovative Materials Polska wdrażanych jest 9 technologii Industry 4.0 które wymienia Boston Consulting Group (Rys. 2).
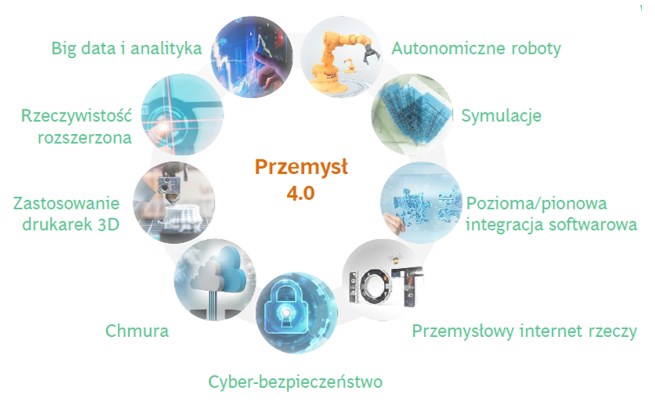
Rys. 2 Dziewięć technologii zmieniających produkcję przemysłową wg Boston Consulting Group
Autonomiczne roboty
Roboty stają się autonomiczne, coraz bardziej elastycznie dostosowują się do otoczenia i potrafią współpracować z człowiekiem w wielu obszarach.
Symulacje
Dzięki upowszechnieniu narzędzi analitycznych przetwarzających dane w czasie rzeczywistym, odzwierciedlenie świata rzeczywistego w modelu wirtualnym będzie zdecydowanie prostsze. Symulacje pozwolą operatorom testować i optymalizować ustawienia urządzeń, zanim zmiany zostaną wprowadzone w świecie rzeczywistym.
Pozioma/pionowa integracja software’owa
Integracja software’owa pozwoli stworzyć w pełni zautomatyzowany łańcuch wartości (np. z dostawcami i klientami).
Przemysłowy Internet Rzeczy
Obecnie w zakładach przemysłowych tylko część urządzeń i sensorów jest ze sobą połączona. Sensory połączone z systemami automatyki służą głównie do odczytywania parametrów i sterowania procesem produkcyjnym. Przemysłowy internet rzeczy sprawia, że coraz więcej urządzeń, a nawet elementy produkcji w toku, jest wyposażonych w wbudowane czujniki i procesory, co pozwala na sprawną komunikację i interakcję. Wpływa to również na coraz bardziej scentralizowaną kontrolę, a zdecentralizowana analityka umożliwia podejmowanie decyzji w czasie rzeczywistym. Już dziś wykorzystywane są elektroniczne układy RFID (identyfikatory wykorzystujące fale radiowe do przesyłania danych), które są wbudowywane w komponenty, dzięki czemu urządzenia na stanowisku pracy wiedzą, jakie czynności należy wykonać w celu dokończenia produktu oraz jak dostosować do zadania linię produkcyjną.
Cyberbezpieczeństwo
Potrzeba stosowania zabezpieczeń kluczowych systemów i linii produkcyjnych przed cyberatakami. W konsekwencji istotą cyberbezpieczeństwa jest niezawodna komunikacja i zaawansowane systemy identyfikacji użytkowników udzielające dostępu do urządzeń.
Chmura (Cloud)
Używanie oprogramowania opartego na chmurze, głównie w celach analitycznych i zarządzania przedsiębiorstwem.
Zastosowanie drukarek 3D
Drukarki 3D są już stosowane na coraz większą skalę. Obecnie korzysta się z nich głównie przy budowaniu prototypów i produkcji pojedynczych komponentów. W Przemyśle 4.0 technologie te będą używane do produkcji pełnych serii produktów cechujących się złożonym kształtem i lekkością. Druk części zamiennych skraca też czas przestoju maszyn.
Rzeczywistość rozszerzona
Systemy oparte o rzeczywistość rozszerzoną wspierają wiele czynności, np. identyfikację konkretnej części w magazynie czy przesyłanie instrukcji naprawy poprzez urządzenia mobilne. Rozwiązania te są dopiero w fazie rozwoju, ale w przyszłości pomogą one pracownikom w szybkim podejmowaniu decyzji i usprawnią procedury związane z wykonywaniem odpowiednich czynności. Rozwiązaniem takim mogą być np. okulary wyświetlające instrukcje naprawy urządzenia, na które w danym momencie patrzymy. Innym przykładem może być symulator wirtualnych szkoleń, uczący pracowników, jak radzić sobie z urządzeniami w razie awarii, bazując na środowisku opartym o trójwymiarowe dane w czasie rzeczywistym.
Big Data i analityka
Analityka oparta o Big Data znalazła do tej pory zastosowanie w przemyśle głównie w zakresie efektywności energetycznej, optymalizacji jakości produktów oraz poprawy utrzymania i serwisowania urządzeń. W kontekście Przemysłu 4.0 narzędzia przetwarzające dane zarówno z systemów produkcyjnych, produktów oraz systemów zarządczych staną się standardem w podejmowaniu decyzji w czasie rzeczywistym.
Predykcja Utrzymania Ruchu
Dzięki rozbudowanej sieci sensorów, Big Data i narzędziom analitycznym przetwarzającym dane w czasie rzeczywistym, Przemysł 4.0 umożliwia konserwację zapobiegawczą urządzeń. Technicy będą zatem w stanie zdalnie i proaktywnie identyfikować potencjalne usterki oraz zamawiać części z wyprzedzeniem. Dokonując przeglądu i naprawy, wyposażeni w rozwiązania rozszerzonej rzeczywistości, będą w stanie otrzymać instrukcje od ekspertów znajdujących się z dala od miejsca naprawy. Praca będzie mogła zostać automatycznie udokumentowana.
- Wnioski na przyszłość
- Pogoń za cyfrowym rozwojem
Historie Noki, Motoroli, BlackBerry, które przeoczyły moment rozwoju smartfonów, tracąc pozycję rynkowych liderów, dowodzą, że nie można bagatelizować cyfrowego rozwoju. Polska powinna w pełni wykorzystać nadchodzące zmiany. Cyfrowa rewolucja dopiero się zaczyna, zarówno w Europie, jak i na świecie. Potrzebne będą m.in. wykształcone kadry inżynierów, potrzebne są nowe kompetencje managerów do przeprowadzenia firmy przez proces transformacji cyfrowej, opracowanie nowego sposobu kształcenia oraz dostosowanie szkoleń. Ponad wszystko potrzebne jest odpowiednie nastawienie oraz otwartości na zmiany
- Spirala marginalizacji
Przez wiele lat inwestycje firm zachodnich w Polsce wynikały z tutejszych niskich kosztów pracy, ale czas ten przemija. Bez wdrażania innowacji z zakresu Przemysłu 4.0 na dłuższą metę stracimy na konkurencyjności. Może to doprowadzić do zjawiska „spirali marginalizacji”. Dla gospodarek, które do tej pory miały perspektywy wzrostu, może to oznaczać przede wszystkim transfer produkcji przemysłowej do krajów wdrażających Przemysł 4.0, nawet jeśli koszty pracy są tam wyższe. W konsekwencji w kraju pozostaje produkcja o niskiej wartości dodanej. Spada wówczas konkurencyjność na tle innych krajów i utrata rynku globalnego, co pociąga za sobą dalszy spadek zatrudnienia. Odpowiednio wczesna reakcja i proaktywne dostosowywanie się do trendów może uchronić kraje przed ryzkiem.
- Być albo nie być
Przemysł 4.0 powinien być istotnym zagadnieniem dla polskich firm, gdyż produkcja przemysłowa stanowi 20% wartości dodanej brutto w gospodarce i zatrudnia 3,1 mln osób. Co dziesiąty obywatel UE zajmujący się produkcją przemysłową, pracuje w Polsce. Dlatego ważne są też działania na szczeblu rządowym, bo tutaj jesteśmy daleko za Europą Zachodnią, gdzie większość państw posiada już powołane swoje programy. Rząd polski niebawem powoła do życia fundację, której zadaniem będzie integracja i koordynacja działań wielu jednostek, w tym administracji publicznej, firm, instytucji edukacyjnych i naukowo-badawczych, na rzecz cyfrowej transformacji przemysłu. Wzorem zachodnioeuropejskich państw, np. Niemiec, również u nas utworzona zostanie Polska Platforma Przemysłu 4.0. Wraz z rozwojem programu należy zwrócić szczególną uwagę na cyberbezpieczeństwo – cyfryzacja wymaga zapewniania bardzo dobrego cyberbezpieczeństwa, kwalifikacje pracowników – dostosowanie systemu kształcenia, szkoleń, przygotowanie kadry kierowniczej w dobie Industry 4.0.
Korzystając z okazji, chciałbym podziękować wszystkim tym, którzy przyczyniają się do rozwoju tego programu w naszym kraju.
Autor: Robert Marchewka, Kierownik Produkcji Samochodowych Szyb Przednich w Saint-Gobain Sekurit Innovative Materials Polska
Artykuł stanowi przedruk publikacji zamieszczonej w materiałach konferencyjnych XVIII Konferencji Lean Management, która odbyła się we Wrocławiu w dniach 12-14 czerwca 2018 roku. Konferencja, która organizowana jest corocznie przez Lean Enterprise Institute Polska, przeznaczona jest dla sektorów produkcyjnego i usługowego. Zapraszamy do odwiedzenia obszernego serwisu internetowego poświęconego Konferencji pod adresem www.leankonf.pl.
Artykuł został opublikowany dzięki uprzejmości i za zgodą firmy Saint-Gobain.