Area Cooling Solution: LEI Polska pomaga „zamrozić” wielkość powierzchni przy rosnącej produkcji
Uzasadnienie dla projektu
Wzrost wolumenu produkcji postawił zakład przed dylematem: inwestycja w nowe powierzchnie produkcyjne (dla sprostaniu rosnącym zamówieniom) czy poprawienie organizacji pracy z wykorzystaniem przepływu jednej sztuki.
Area Cooling Solutions
Area Cooling Solutions zajmuje się dystrybucją, projektowaniem i produkcją urządzeń dla chłodnictwa i HVAC od 1986 roku. Przedsiębiorstwo zlokalizowane jest w Nowej Wsi Wrocławskiej.
Area Cooling Solutions jest producentem i dystrybutorem komponentów i systemów chłodniczych i klimatyzacyjnych. Zasady, którymi kieruje się zarówno podczas projektowania produktów, jak i selekcji komponentów, to:
• Wydajność energetyczna (W/W),
• Korzystny stosunek ceny do jakości (€/W),
• Efektywne zużycie materiałów (g/W).
Wspierane przez:
• Doskonałą logistykę,
• Doskonałe wsparcie techniczne,
• Duże możliwości produkcyjne,
• Szerokie zaplecze dostawców z całego świata.
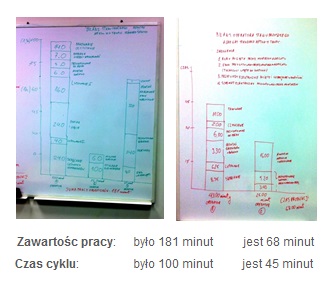
Redukcja czasu montażu Agregatu APTX Tropic
Wyzwania w projekcie
• Opracowanie nowej organizacji produkcji z wykorzystaniem idei przepływu jednaj sztuki – na produkcji znajdowało się wiele urządzeń w tej samej fazie produkcji zajmując niepotrzebnie miejsce i powodując spływ w partiach do testów, kontroli i pakowania
• Wiele podzespołów, typu szafki elektryczne czy przewody miedziane, były przygotowywane na bieżąco wydłużając cykl produkcyjny urządzenia
• Pracownicy mieli wyuczone specjalności, co powodowało, że trudno było zbilansować pracę, w związku z tym, najdłuższa operacja powodowała wydłużenie czasu przejścia
Korzyści, które osiągnęliśmy
• Znaczne zmniejszenie powierzchni montażowej – zwiększenie ~ 30% produkcji bez rozbudowy hali
• Uzyskanie uprawnień przez wszystkich pracowników – pozbycie się problemu balansowania operacji
• Znaczne skrócenie czasu wykonywania produktów poprzez przygotowanie supermarketów skrzynek elektrycznych, wygiętych rurek miedzianych i podstaw ~ 20-30%
• Stworzenie i utrzymywanie supermarketu wyrobów gotowych dla powtarzalnych agregatów
• Uporządkowanie miejsca dostaw na produkcji – były dostawy cało-paletowe, nierozpakowane, z częstymi zwrotami przy wykorzystaniu dużej powierzchni przy produkcji: po projekcie LEIP: dostawy skompletowanych agregatów znajdują miejsce na specjalnym wózku
• Poprawa pracy magazynu – magazyn kompletuje trzy kolejne wózki wg planu produkcji i zawsze jest przygotowany do podstawienia materiału na sygnał z produkcji
Główne kierunki działań w projekcie
Ekspert LEI Polska pomógł w wykonaniu Mapy Strumienia Wartości na podstawie której wytyczono główne kierunki działania.
Zespół Area pracując kilka miesięcy wdrożył:
• nową organizację pracy z przepływem jednej sztuki w trzech obszarach produkcyjnych
• nowe layouty
• całkiem nowe stanowiska montażowe dla przepływu jednej sztuki
• dodatkowe szkolenia pracowników montażowych aby mogli wykonywać inne funkcje
• nowy sposób dostarczania komponentów do montażu
• wizualizację do informowania o statusie wyrobu w trakcie produkcji
Podczas systematycznych konsultacji ekspert LEI Polska wspólnie z zespołem oceniał wykonane zadania, podpowiadał kolejne etapy i szczegóły nowych rozwiązań.
Jak LEI Polska pomogło
• Wykorzystano mapę strumienia wartości dla zidentyfikowania punktów w procesie od których należało rozpocząć przemiany
• Zaproponowano całkowicie nowe podejście do organizacji produkcji – przepływ jednej sztuki, dostawy materiałów do stanowiska na specjalnych stojakach wózkach dla pojedynczych agregatów
• Zorganizowano supermarket: szafek elektrycznych, przewodów miedzianych, podstaw