Czym jest „prawdziwa północ?” (ang. True North)
W swoich działaniach produkcyjnych Toyota przez dekady dążyła do osiągnięcia długoterminowej wizji, na którą składały się:
1. zero braków
2. 100% wartości dodanej,
3. przepływ jednej sztuki,
4. bezpieczeństwo dla ludzi.
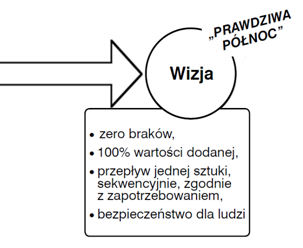
Wizja prawdziwej północy Toyoty
Firma postrzega ten szczególny stan jako sposób produkcji wyrobów o najwyższej jakości, przy najniższych kosztach i najkrótszym czasie przejścia. W ostatnich latach firma zaczęła określać go mianem „prawdziwej północy” dla działań produkcyjnych (ang. true north). Możesz traktować tę wizję produkcji jako „zsynchronizowany przepływ pojedynczej sztuki od A do Z, przy możliwie najniższym koszcie”. Zauważ, że wizja produkcji Toyoty opisuje stan, a nie wartości finansowe czy księgowe.
Kiedy po raz pierwszy natknąłem się na toyotowską wizję „prawdziwej północy”, myślałem, że znalazłem błąd, i wytknąłem to osobie z Toyoty. „100% wartości dodanej jest prawdopodobnie nie do osiągnięcia” – powiedziałem. „Jeżeli tylko przesuwacie produkt z jednego miejsca na drugie, to jest już w tym marnotrawstwo!”. Odpowiedź, jaką otrzymałem, brzmiała: „Możliwe, że nasza „prawdziwa północ” dla produkcji jest teoretyczna i nieosiągalna, ale to nie ma większego znaczenia. Nam służy jako wyznacznik kierunku i nie spędzamy czasu, dyskutując, czy da się to osiągnąć, czy nie. Spędzamy za to dużo czasu, starając się do tego zbliżyć”. Innymi słowy, dopuszczalne, a nawet pożądane jest, by wizja była na pierwszy rzut oka dylematem, a dzięki temu stanowiła wyzwanie.
Dążenie do doskonalenia w takim właśnie kierunku, we wszystkich procesach, jest światłem latarni dla działań produkcyjnych Toyoty i najwyraźniej się nie zmienia. Zarówno firmowa filozofia przetrwania poprzez ciągłe doskonalenie, jak i wyznacznik kierunku są cały czas spójne, niezależnie od tego, kto w danym momencie przewodzi firmie. Postęp Toyoty ku warunkom „prawdziwej północy” ma z całą pewnością charakter wzrostowy. Zawdzięcza to niewątpliwie spójnemu ukierunkowaniu realizowanemu nieprzerwanie przez ponad 50 lat. Dzięki temu Toyota zdołała osiągnąć prowadzenie w eliminacji marnotrawstwa oraz doskonaleniu przepływu wartości. I ciągle idzie naprzód.
Używanie poczucia kierunku w zarządzaniu ludźmi
W trakcie wizyty na linii montażu w fabryce produkującej przewody do układów ABS (kabelki zakończone czujnikiem z jednej i wtyczką z drugiej strony) dowiedzieliśmy się, że wielkość partii w procesie montażowym wynosi jeden tydzień. Oznacza to, że produkowana jest liczba jednego typu przewodów odpowiadająca pięciu dniom sprzedaży, a następnie proces montażu jest przezbrajany, aby wyprodukować pięciodniową partię kolejnego typu. Szybkie przeliczenie pokazało jednak, że dostępne moce przerobowe pozwalają na częstsze przezbrojenia a tym samym zmniejszenie partii produkcyjnych. Obszar montażu mógł określić warunek docelowy jednodniowej partii zamiast obecnych pięciu dni i uzyskać to nawet bez skracania, i tak już krótkich, przezbrojeń. W sali konferencyjnej zwróciliśmy zarządowi uwagę na potencjał związany z produkcją w mniejszych partiach. Korzyści wynikające z mniejszych partii produkcyjnych są dobrze znane i znaczące: zbliżenie do przepływu jednej sztuki, mniejsze zapasy i straty, szybsza reakcja na różnorodne wymagania klientów, mniej ukrytych braków i napraw, możliwość użycia systemu kanban i tak dalej. Kierownik produkcji natychmiast zareagował, mówiąc: „Nie możemy tego zrobić”. Wyjaśniał: „Nasz przewód jest komponentem systemu bezpieczeństwa w samochodzie i w związku z tym, przy każdym przezbrojeniu, musimy wypełniać mnóstwo papierków związanych z identyfikacją partii. Musimy także zdawać do działu kontroli jakości każdą pierwszą sztukę i opóźniać produkcję do momentu dopuszczenia jej przez jakość. Jeżeli zmniejszylibyśmy partie montażowe z pięciu dni do jednego, ilość dokumentów i opóźnień produkcji wzrosłaby pięciokrotnie. Te dodatkowe czynności bez wartości dodanej byłyby marnotrawstwem i zwiększyłyby nasze koszty. Wiemy, że lean oznacza eliminowanie strat, więc redukcja wielkości partii nie jest dobrym pomysłem”. Dyrektor zakładu zgodził się z przedmówcą. Na tym właśnie polega znacząca różnica w porównaniu z Toyotą. Menedżer w Toyocie prawdopodobnie powiedziałby swojemu kierownikowi montażu mniej więcej coś takiego: „Masz rację, że dodatkowe dokumenty i wymóg inspekcji pierwszego produktu są przeszkodami w osiągnięciu mniejszych partii produkcyjnych. Dziękuję za zwrócenie na to uwagi. Jednakże fakt, że chcemy zredukować wielkość partii, nie podlega dyskusji ani nie jest opcjonalny, ponieważ przybliża nas do przepływu jednej sztuki. Zwróć swoją uwagę na dwie przeszkody stojące na drodze naszego rozwoju, zamiast tracić czas na dyskusje, czy powinniśmy zredukować wielkość partii, czy też nie. Przyjrzyj się dokumentom i procesowi kontroli i złóż raport o tym, czego się dowiedziałeś. Potem poproszę Cię o propozycję, jak możemy zmniejszyć partie produkcyjne do jednego dnia bez zwiększania naszych kosztów.”
Jak pokazuje przykład producenta przewodów, bez wyznaczonego kierunku mamy tendencję do indywidualnej oceny propozycji na podstawie ich własnych zalet, a nie jako części dążenia do czegoś. Taka sytuacja stwarza często efekt czysto jałowej dyskusji, „polowania na rozwiązania” oraz wyboru rozwiązań pochodzących od osoby, która w danej chwili jest najbardziej przekonująca lub władna. Bez poczucia kierunku mamy tendencję do krótkoterminowej analizy kosztów i korzyści, a także podejmujemy decyzje, czy coś powinno być zrobione, w jakim kierunku podążać i co robić – raczej przypadkowo – zamiast pracować nad przeszkodami stojącymi na drodze do nowego poziomu efektywności. Jak wiele razy byłeś świadkiem storpedowania interesującej, choć jeszcze niesformułowanej do końca, idei pytaniem: „Czy będą z tego korzyści finansowe?”