LG Display Poland: budowa i utrzymanie systemu TPM
Uzasadnienia dla projektu
- Warunki środowiskowe, w jakich odbywa się proces wytwórczy modułów LCD, wymagają utrzymywania wysokich standardów względem czystości i niezawodności maszyn na liniach produkcyjnych.
- Analiza wykazała, że nawet drobny pył w maszynie czy powietrzu może być przyczyną braków albo awarii.
- Zauważono, że kluczem przy wdrażaniu systemu TPM jest zaangażowanie ludzi nie tylko w procesie czyszczenia maszyn, ale również w identyfikowaniu problemów w ich pracy. System TPM wymaga sprawnej komunikacji pomiędzy operatorami i pracownikami utrzymania ruchu, a także ich wspólnego zaangażowania w utrzymywania maszyn w należytej sprawności.
LG Display Poland
- Rok założenia: 2006
- Lokalizacja: Biskupice Podgórne pod Wrocławiem
- O firmie: działa w 10 krajach i zatrudnia ponad 55 000 osób. Jest częścią koncernu LG i zarazem czołowym producentem oraz dostawcą ciekłokrystalicznych modułów TFT – LCD.
- Ciekawostki: pionier w masowej produkcji paneli z diodowym podświetleniem LED, paneli OLED, paneli elastycznych LCD oraz modułów 3D.
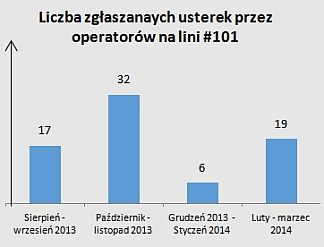
Przykłady wzrostu zaangażowania operatorów w działania konserwacyjne na maszynie
Wyzwania w projekcie
- Celem projektu było zmniejszenie awaryjności na liniach produkujących moduły LCD.
- Zaangażowanie operatorów w zgłaszanie i rozwiązywania problemów technicznych na maszynie.
- Zmiana mentalności ludzi pracujących w firmie z tego, że sprzątamy aby maszyna była czysta na to, że świadomie czyścimy i konserwujemy maszynę, aby wychwytywać na niej problemy i usterki.
- Szkolenie wewnętrzne z zakresu TPM grupy ponad 1500 pracowników produkcyjnych.
Korzyści
- Zwiększenie zaangażowania operatów w działania konserwujące na liniach produkcyjnych, które przełożyło się na liczbę zgłaszanych usterek na maszynach i związaną z nimi prewencje.
- Powtarzalność procesów autonomicznej konserwacji – dzięki opisaniu ich w postaci Karty Pracy Standaryzowanej i wdrożeniu systemu audytów.
- Opracowanie szeregu usprawnień Kaizen w oparciu o problemy dostrzeżone podczas wykonywania przeglądów autonomicznej konserwacji.
Główne kierunki działań w projekcie
Projekt wdrożeniowy rozpoczął się od warsztatu z kadrą kierowniczą, gdzie ustalono główne cele dla projektu TPM oraz opisano Road Map. Kolejnym etapem był dwudniowy warsztat praktyczny TPM dla wyselekcjonowanej grupy Champion, która składała się najbardziej doświadczonych operatorów i pracowników utrzymania ruchu. Podczas warsztatów z grupą Champion zaprojektowano:
- System zgłaszania usterek
- Standardy czyszczenia i konserwacji maszyn na liniach produkcyjnych – karty pracy standaryzowanej TPM
- Audyt TPM
Kolejnym etapem było szkolenie 6 trenerów wewnętrznych TPM, których celem było poprowadzenie szeregu całodniowych warsztatów praktycznych TPM dla pozostałych pracowników produkcyjnych w LG Display Poland. Dzięki temu dalsze rozpowszechnianie systemu TPM wśród pracowników LG Display Poland mogło odbywać się bez zaangażowania konsultanta LEI Polska. Finalną częścią projektu były wizyty konsultanta LEI Polska podczas których analizowano poziom wdrożenia systemu TPM oraz wdrażano działania korygujące.
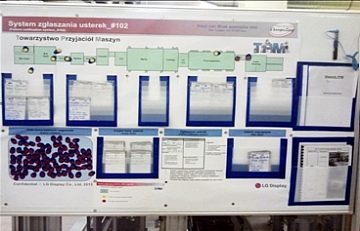
System zgłaszania usterek opracowany przez grupę Champion podczas warsztatów praktycznych TPM prowadzonych przez konsultanta LEI Polska
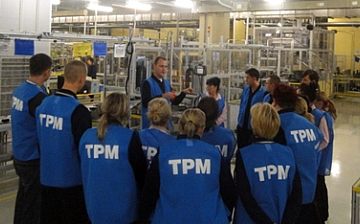
Wewnętrzne warsztaty praktyczne TPM prowadzone przez pracowników LG Display Poland w oparciu o standard opracowany przez LEI Polska
Wypowiedzi klientów
Bazując na dobrych nawykach wynikających z prawidłowo zaimplementowanego narzędzia 5S mogliśmy rozpocząć pracę nad wdrażaniem podstawowego filaru TPM, czyli autonomicznej konserwacji. Pierwszym etapem było wybranie firmy konsultingowej, która to będzie naszym przewodnikiem i wsparciem podczas całego procesu budowania nowego dla nas systemu. W taki sposób rozpoczęliśmy współpracę z Lean Enterprise Institute Polska.
Mariusz Maczuga, Inżynier Produkcji / TPM Task, LG Display Poland
Droga, którą LG Display Poland chce podążać, to droga poprzez świadome dostosowywanie narzędzi Lean do specyfiki naszych procesów. Wiemy, że każda zmiana wymaga poświęceń i pełnego zaangażowania, ale osiągnięte wyniki, w pełni rekompensują trudy, jakie do tej pory zostały poniesione. W dalszym ciągu będziemy poszukiwali marnotrawstwa i je eliminowali między innymi poprzez rozpoczęcie warsztatów z mapowania strumienia wartości również z firmą Lean Enterprise Institute Polska.
Bartłomiej Kotlarski, Inżynier Produkcji, Leader TPM Task, LG Display Poland