5S na produkcji i w biurze, czyli jak systemowo wdrożyć ład i porządek w miejscu pracy
5S jest zestawem technik i metod mających na celu ustanowienie i utrzymanie wysokiej jakości stanowisk pracy. 5S jest jednocześnie jednym z podstawowych narzędzi Lean Manufacturing i Lean Management, gdyż wiąże się bezpośrednio z właściwą organizacją środowiska pracy, doskonaleniem kultury organizacyjnej przedsiębiorstwa oraz – co bardzo ważne – pozwala na zwiększenie stabilności procesów. Z tego też powodu 5S traktowane jest bardzo często jako kluczowa technika Lean Management, wdrażana w firmach produkcyjnych i usługowych jako jedna z pierwszych, stanowiąca podstawę do dalszych działań Kaizen.
W systemie 5S wyodrębnić można 5 następujących po sobie kroków postępowania, przy czym nazwa każdego z tych kroków rozpoczyna się na literę S. Wymienić tutaj należy kolejno 1:
- 1. S – Sortowanie (jap. Seiri)
- 2. S – Systematyka (jap. Seiton)
- 3. S – Sprzątanie (jap. Seiso)
- 4. S – Standaryzacja (jap. Seiketsu)
- 5. S – Samodyscyplina (jap. Shitsuke).
Metodę 5S, stosowaną dla stanowisk produkcyjnych, biurowych, magazynowych i usługowych, przedstawia schemat na poniższym rysunku (rys. 1).
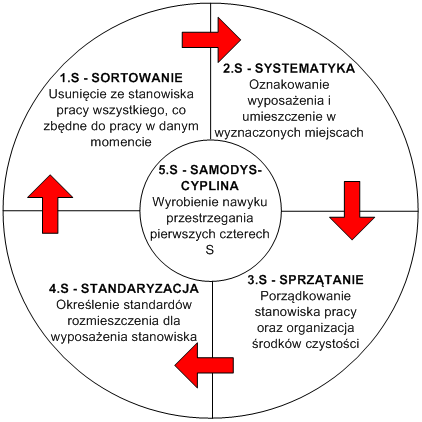
Rys. 1. Schemat metody 5S
1.S – Sortowanie
Sortowanie jest pierwszym z pięciu etapów metody 5S i ma na celu odseparowanie ze stanowiska pracy wszystkiego, co jest zbędne do jej wykonywania. Pozwala na identyfikację nadmiernych materiałów, nieużywanych narzędzi i przyrządów, starych instrukcji pracy, niepotrzebnych danych i innych informacji, które nie są konieczne do wykonywania zadań produkcyjnych lub usługowych, zakłócając jedynie poprawny ich przebieg oraz przyczyniając się do powstawania marnotrawstwa. W ten sposób etap sortowania pozwala utrzymać stanowisko pracy w czystości oraz pomaga pozostawić na nim tylko to, co jest naprawdę potrzebne. Schemat kroku sortowania przedstawia rysunek 2.
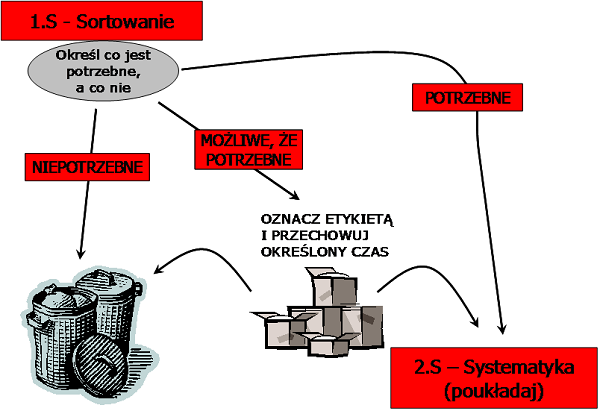
Rys. 2. Schemat sortowania
Etapowi sortowania powinna przyświecać zasada znana z podejścia „dokładnie na czas” (ang. just–in-time): na stanowisku pozostaje tylko to, co jest potrzebne, tylko w takiej ilości, jak potrzebne i tylko wtedy, kiedy jest to potrzebne.
Właściwe przeprowadzenie kroku sortowania pozwala na eliminację wielu problemów związanych z nadmiarem rozmaitych przedmiotów na stanowiskach pracy, takich jak np. 2:
- „zagracenie” stanowisk zbędnymi przedmiotami, powodującymi utrudnienia we właściwym wykonywaniu zadań,
- marnotrawstwo czasu na odnajdowanie przez pracownika właściwego wyposażenia, narzędzi, materiałów oraz informacji,
- zbędne zapasy materiałów, części i komponentów do produkcji, przechowywane na stanowiskach i tworzące tym samym dodatkowe koszty oraz ukrywające istniejące problemy,
- nieuzasadnione rozmiary stanowisk, zastawionych szafami, półkami i regałami, powodujące fizyczne bariery w komunikacji oraz utrudniające doskonalenie przepływu materiału i informacji, a także zajmujące zbyt wiele powierzchni.
Według metody 5S wszystkie rzeczy zbędne do pracy w danym momencie powinny być albo wyrzucone (złomowane), albo zabrane ze stanowiska i oznaczone tzw. czerwoną etykietą oraz przechowywane w wyznaczonym miejscu nazwanym magazynem czerwonych etykiet. Magazyn taki spełnia funkcję „poczekalni” dla przedmiotów aktualnie niepotrzebnych, umożliwiając pozostawienie na stanowiskach jedynie niezbędnego wyposażenia. Przykładowy wzór czerwonej etykiety przedstawiono na rysunku 3.
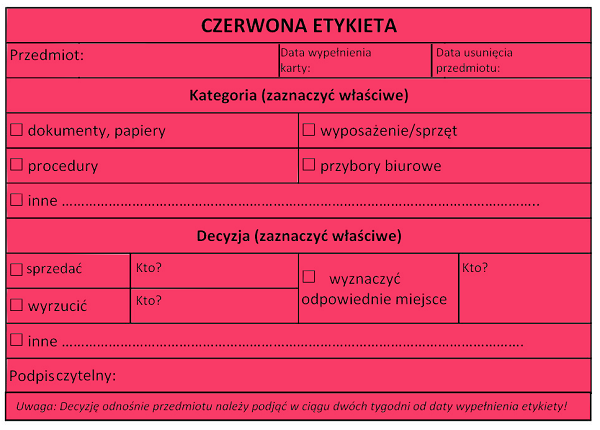
Rys. 3. Przykład czerwonej etykiety
Oprócz określenia kategorii usuniętych ze stanowiska przedmiotów, czerwona etykieta umożliwia również określenie powodów usunięcia, daty, ilości oraz pozostałych danych potrzebnych do identyfikacji rzeczy określonych na etapie sortowania jako zbędne.
2.S – Systematyka
Realizacja kroku systematyki polega na takiej organizacji oraz oznaczeniu wszystkich elementów stanowiska pracy (materiały, narzędzia, przyrządy, instrukcje, dokumenty itp.), aby były one łatwe do użycia i odłożenia na swoje miejsce, jak również do odnalezienia i identyfikacji przez każdego pracownika 2. Warte podkreślenia jest tutaj słowo „każdego”, ponieważ to właśnie przejrzystość i pełna wizualność miejsca pracy powinna być celem głównym drugiego etapu 5S. Wdrożenie odpowiednich narzędzi kontroli wizualnej pozwala na wyeliminowanie wielu rodzajów marnotrawstwa na stanowiskach pracy, co schematycznie przedstawiono na poniższym rysunku.
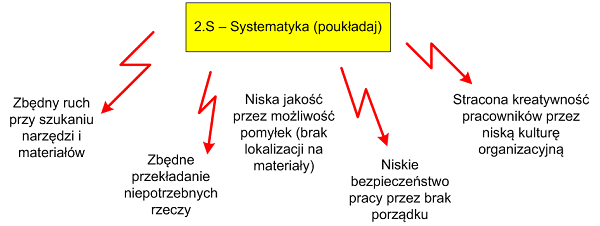
Rys. 4. Marnotrawstwo eliminowane przez systematykę
Podstawowym narzędziem do zastosowania w tym kroku 5S jest sterowanie wizualne, czyli w uproszczeniu, wszystkie rozwiązania stosowane w środowisku pracy, mające na celu szybkie i czytelne przedstawienie sposobu pracy, statusu obecnie wykonywanych działań oraz kontroli nad stanem i lokalizacją wyposażenia stanowisk, bez konieczności zadawania pytań.
Do podstawowych technik sterowania wizualnego zalicza się tutaj: jasno określone obszary składowania (linie, tabliczki, etykiety, pola odkładcze), oznaczanie kolorami, oznaczanie strzałkami, oznaczenie poziomów maksymalnych i minimalnych dla materiałów do produkcji, dla wyrobów gotowych i dla towarów oraz tzw. tablice cieni (ang. shadow boards). Na tablicy cieni każde narzędzie umieszczone jest na wyznaczonym miejscu, co pozwala na błyskawiczną identyfikację braku któregoś z nich oraz określenie rutyny pobierania i odkładania każdego z narzędzi.
Poniższe rysunki przedstawiają przykłady zastosowania oraz oznaczenia powierzchni produkcyjnej. Zostały one w ten sposób, aby każdy z używanych na hali produkcyjnej przedmiotów (urządzeń, materiałów) miał swoje najlepsze i dokładnie oznaczone miejsce składowania.
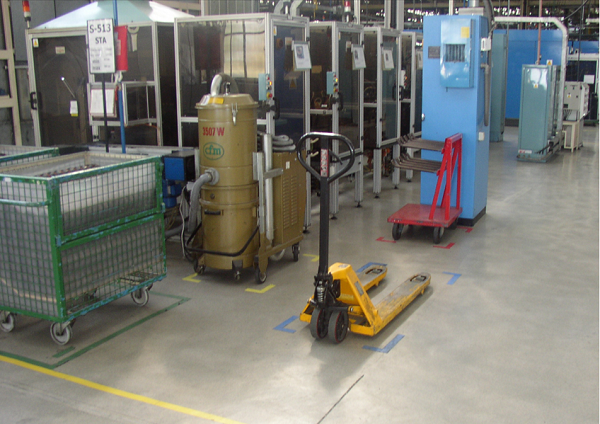
Rys. 5. Przykładowe oznaczenie powierzchni hali produkcyjnej
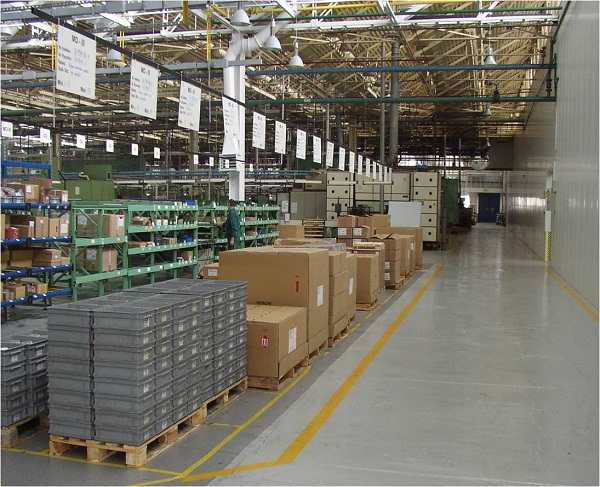
Rys. 6. Przykładowe oznaczenie powierzchni hali produkcyjnej
Dwa następne zdjęcia przedstawiają z kolei możliwości zastosowania koncepcji sterowania wizualnego w środowisku biurowym na przykładzie biura LEI Polska.
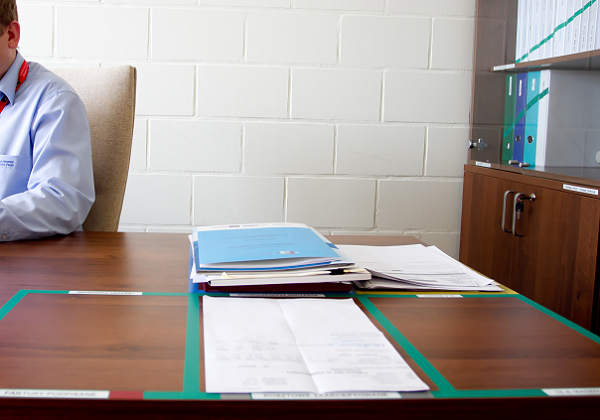
Rys. 7. Przykład sterowania wizualnego zastosowany w biurze LEI Polska
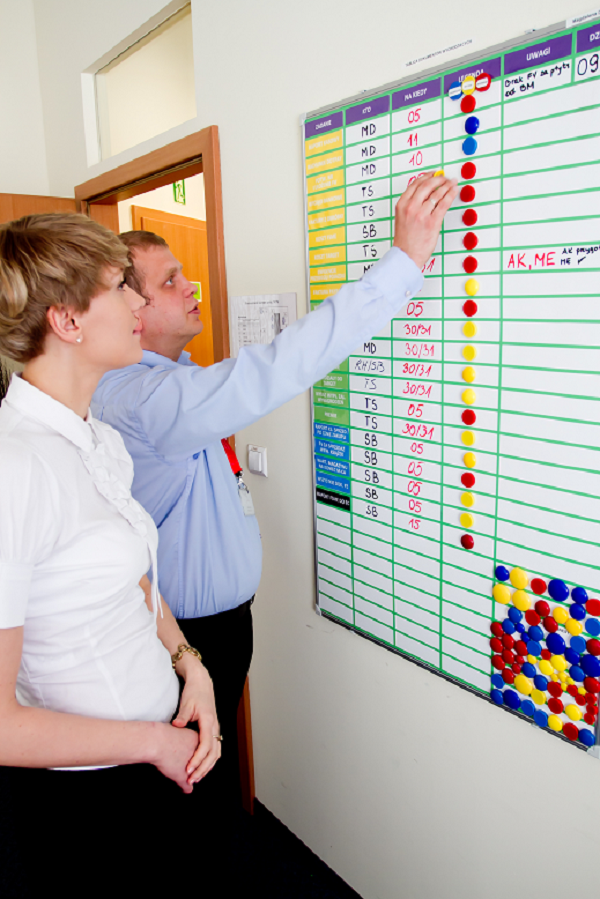
Rys. 8. Przykład sterowania wizualnego zastosowany w biurze LEI Polska
3.S – Sprzątanie
Trzeci etap metody 5S pozwala na określenie częstotliwości i metody sprzątania stanowiska pracy jak również dokładne wyznaczenie standardu poprawnego sprzątania oraz przypisanie określonych obszarów i niezbędnych zasobów z tym związanych. W 5S sprzątanie jest postrzegane na dwa sposoby: po pierwsze, jako fizyczne czyszczenie i konserwacja miejsca pracy (zamiatanie, używanie chemicznych środków czystości, smarowanie połączeń i powierzchni, itp.) i po drugie, jako tzw. sprzątanie „wizualne”, przez które rozumieć należy możliwość natychmiastowej identyfikacji ewentualnych awarii, problemów oraz braku ładu i porządku (co możliwe jest jedynie w przypadku wizualnej organizacji stanowiska pracy).
Jako główne cele do osiągnięcia w tym kroku wymienić należy:
- utrzymanie obszaru wdrożenia 5S w dobrym stanie przez właściwe czyszczenie stanowiska oraz jego konserwację,
- identyfikację źródeł i przyczyn powstawania zanieczyszczeń, brudu, wycieków płynów, itp. a następnie ich eliminację, identyfikację i precyzyjne określenie zakresu zadań i czynności przy czyszczeniu miejsca pracy poprzez utworzenie instrukcji i harmonogramów czyszczenia,
- ujawnienie materiałów oraz dokumentów o zbliżającym się terminie przedłożenia klientowi, czy to zewnętrznemu, czy wewnętrznemu.
Realizacja zasady trzeciego S poprzez regularne porządkowanie miejsca pracy powinna być włączona w zakres codziennych obowiązków operatora (właściciela) danego stanowiska i wykonywana przez niego osobiście. Oprócz oczywistych przesłanek (utrzymanie porządku oraz dobrego stanu maszyn, urządzeń, przedmiotów pracy), sam proces czyszczenia stanowiska wraz z jego wyposażeniem i używanymi maszynami daje również sposobność do identyfikacji anomalii oraz wykrycia potencjalnych problemów, które zazwyczaj pozostają niezauważone przy jedynie pobieżnym oglądzie miejsca pracy. Codzienne doglądanie newralgicznych punktów maszyn przez operatorów pozwala na poniesienie u nich zdolności obserwacji pracy maszyny oraz szybkiego wykrycia nawet drobnych nieprawidłowości.
Przedstawiony opis środowiska produkcyjnego nie oznacza, iż 3.S nie znajduje zastosowania w obszarach pozaprodukcyjnych. Rutynowe porządkowanie stanowiska biurowego pozwala m.in. uniknąć konsekwencji niezadowolenia klienta, którego zamówienie zawieruszyło się stosach zakurzonych dokumentów, zalegających na biurkach.
Warto podkreślić, że dzięki zastosowaniu prostych narzędzi wspomagających (np. metoda „5 x dlaczego”) na tym etapie 5S możliwe staje się również dokładne określenie przyczyn źródłowych powstałych nieprawidłowości. Spodziewanym efektem jest więc również eliminacja większości uciążliwych zakłóceń poprzez dotarcie do źródeł ich powstawania i skuteczne im zapobieganie.
Jednym z częściej spotykanych sposobów praktycznego wdrożenia 3.S jest dokładne odnowienie stanowisk pracy a następnie podzielenie ich na strefy i przypisanie odpowiedzialności za nie do konkretnych pracowników (lub zespołów pracowników). W zamyśle już samo odnowienie wyposażenia w miejscu pracy ma przyczynić się do odsłonięcia wszelkich nieprawidłowości oraz przełamać dotychczasowe praktyki, wynikające z wieloletnich zaniedbań. Przypisanie odpowiedzialności za utrzymanie wyznaczonych stref w nienagannej czystości powinno być sposobem na rozbudzenie w pracownikach poczucia własności wobec miejsca pracy, co powinno z kolei zaowocować lepszym wykonywaniem powierzonych obowiązków.
4.S – Standaryzacja
Standaryzacja ma na celu określenie standardów realizacji i przestrzegania pierwszych trzech kroków podejścia 5S. Standaryzacja określana jest również jako kluczowa technika do osiągnięcia powtarzalności wdrożonych zmian doskonalących stanowisko pracy. Implementację tego etapu 5S osiągnąć można poprzez 4:
- stworzenie dokładnych instrukcji wykonywania wszystkich czynności w zakresie pierwszych trzech kroków 5S,
- określenie zakresu czynności oraz odpowiedzialności pracowników za działania 5S,
- podjęcie działań mających na celu zabezpieczenie zmian doskonalących stanowiska pracy przed powrotem do stanu poprzedniego.
Określenie standardów ma na celu osiągnięcie sytuacji, w której wszystkie stanowiska pracy będą przejrzyste i wizualnie tak oznaczone, że zmiana zakresu obowiązków dla pracownika wiązać się będzie jedynie z krótkim przeszkoleniem, a identyfikacja odstępstw od wyznaczonego standardu będzie bardzo szybka. Standardy dotyczące rozmieszczenia i oznaczenia narzędzi, przedmiotów pracy, materiałów i jakiegokolwiek innego wyposażenia stanowisk powinny być ogólnie znane i wspólne dla całego przedsiębiorstwa. Standardy i procedury muszą być jasne, proste i bardzo łatwe do zrozumienia, dlatego też do dobrych praktyk 5S należy jak najszersze zaangażowanie pracowników danego obszaru do ich opracowywania. Ze względu na to, że to właśnie pracownicy wykonujący pracę najlepiej znają specyfikę działań na swoim stanowisku, są oni w stanie stworzyć najlepsze instrukcje i standardy, a dzięki temu jeszcze lepiej zrozumieć istotę zachodzących zmian i ciągle się doskonalić.
Standardowe instrukcje powinny spełniać postulat pełnej wizualności, a zatem winny przedstawiać na zdjęciach całe spektrum operacji do wykonania. Takie przedstawienie instrukcji pracy (lub sprzątania stanowiska) zapewnia, że będzie ona zrozumiała dla pracowników, zaś jej interpretacja nie będzie nastręczać trudności (w przeciwieństwie do np. instrukcji składających się jedynie z pisemnych opisów zadań do wykonania).
Prawidłowe wdrożenie 4.S powinno obejmować również określenie standardów oznaczania i rozmieszczenia narzędzi, przyrządów i przedmiotów pracy na stanowiskach pracy. Oznacza to konieczność zdefiniowania sposobu ich prezentacji dla operatora, identyfikacji odpowiednimi kolorami, etykietami, opisami, itp. Dzięki wdrożeniu takiego rozwiązania zmiana stanowiska pracy przez pracownika nie powinna powodować przestojów spowodowanych poszukiwaniem narzędzi lub instrukcji pracy, czy też kłopotami z ich właściwą identyfikacją (marnotrawstwo nadmiernego ruchu na stanowisku).
Poniższy dokument stanowi przykład standardu oznaczania i organizacji szaf magazynowych, który jest stosowany w biurze LEI Polska.
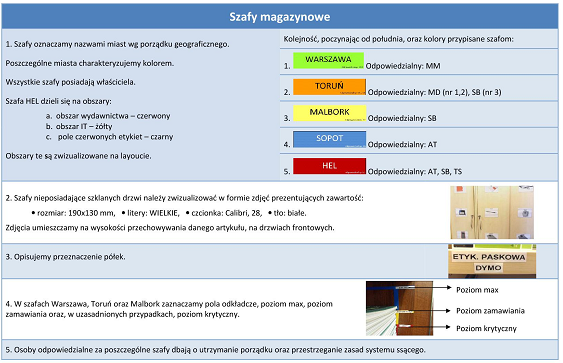
Rys. 8. Standard 5S stosowany w LEI Polska
5.S – Samodyscyplina
Ostatni krok metody 5S stanowi swego rodzaju klamrę spinającą wdrożenie czterech pierwszych etapów na stanowiskach pracy. Samodyscyplina nie powinna być jednak rozumiana jako zestaw nakazów dla pracowników, czy zasad do przestrzegania, których pomijanie rodzi za sobą negatywne konsekwencje, ponieważ wprowadzanie rozwiązań o negatywnym zabarwieniu może przynieść skutki odwrotne do zamierzonych. Chodzi tutaj bardziej o wyrobienie wśród użytkowników stanowisk pracy nawyków i przyzwyczajeń koniecznych do przestrzegania wdrożonych rozwiązań usprawniających, jak również umiejętności pracy zgodnie ze standardami.
Wypracowanie nowych nawyków jest niejednokrotnie procesem długotrwałym i wymagającym sporego wysiłku. Z tego też powodu samodyscyplina określana jest często jako najtrudniejszy do wdrożenia element w podejściu 5S, ponieważ wiąże się z koniecznością zmiany sposobu myślenia oraz zmianą dotychczasowych praktyk i przyzwyczajeń. Takie niejednokrotnie głębokie zmiany w kulturze organizacyjnej przedsiębiorstwa wymagają szerokiego zaangażowania najwyższego kierownictwa firmy. Rysunek zaprezentowany poniżej, przedstawia podstawowe zadania kierownictwa, konieczne dla udanej realizacji wdrożenia 5S.
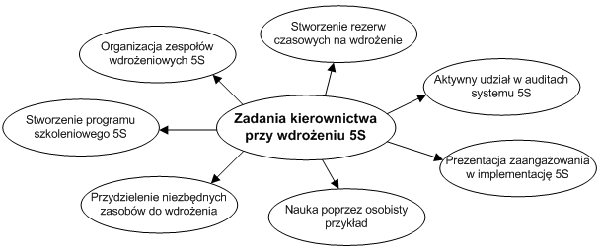
Rys. 9. Zadania kierownictwa przy wdrożeniu 5S
Wśród najistotniejszych narzędzi wspomagających realizację piątego kroku metody wymienić należy audity stanowisk pracy. Audity takie mają na celu przede wszystkim identyfikację odstępstw w funkcjonowaniu stanowisk pracy od założonych standardów oraz, w przypadku stwierdzenia niezgodności, określenie niezbędnych działań korygujących. Przeprowadzane regularnie i zawsze wg ustalonego harmonogramu oraz określonej karty auditowej, pozwalają na szybkie odkrycie nieprawidłowości oraz wyznaczenie niezbędnych działań dla ich eliminacji, terminu oraz odpowiedzialnych za ich podjęcie. W ten sposób fakt ciągłego nadzoru nad systemem 5S kształtuje odpowiednie postawy wśród pracowników, sprowadzające się do właściwego przestrzegania wprowadzonych zmian.
Poniżej przedstawiono dwie przykładowe karty auditowe. Pierwsza znajduje zastosowanie w środowisku produkcyjnym i obejmuje 1. oraz 2. krok 5S, druga natomiast dotyczy zasad 5S w obszarach biurowych.
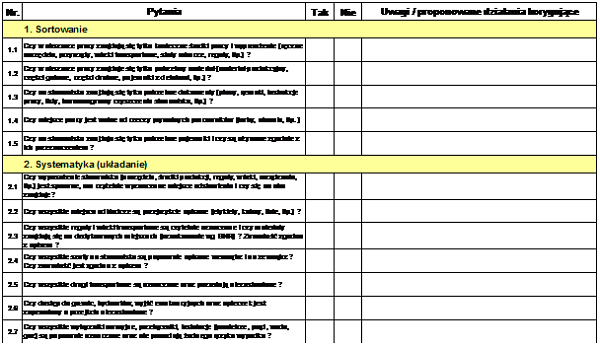
Rys. 10. Przykładowa karta audytowa 5S (produkcyjna)
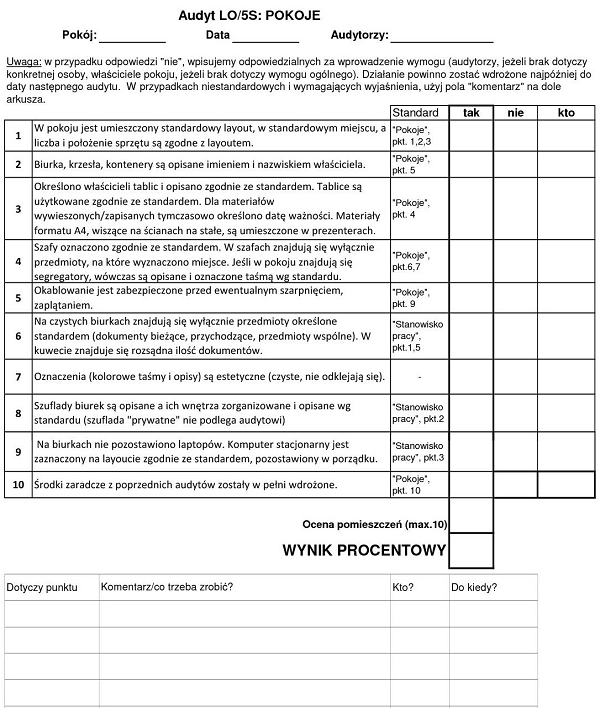
Rys.11. Przykładowa karta audytowa 5S, stosowana podczas audytów w biurze LEI Polska
Nieodłączną częścią auditów jest późniejsza prezentacja ich wyników, mająca również na celu wizualne wskazanie obszarów, w których wymagane są jeszcze intensywniejsze działania.
5S w obszarach pozaprodukcyjnych
Pojawiające się w artykule wielokrotne nawiązania do środowiska pozaprodukcyjnego, stanowią zabieg intencjonalny, mający na celu osłabienie silnego utożsamienia systemu 5S z halą produkcyjną. Przedstawione metody i techniki organizacji stanowisk pracy znajdują bowiem swoje zastosowanie również w obszarach biurowych, i tam także dowodzą swej wartości. 5S jest bowiem na tyle uniwersalnym podejściem, że kolejne kroki tej metody mogą obejmować np. stanowiska pracy biurowej lub miejsca przechowywania dokumentów oraz wyposażenia biur, pozwalając na pozbycie się z nich zbędnych sprzętów, dokumentów, niepotrzebnych w pracy formularzy czy segregatorów z dokumentacją, jak również lepszą organizację samego procesu.
Wdrożenie rozwiązań 5S jest z zasady identyczne jak przy wdrożeniach na hali produkcyjnej i przebiega w wyniku realizacji pięciu wymienionych już wcześniej kroków. Różnicę stanowić mogą natomiast rozwiązania dedykowane dla stanowisk administracyjnych. Rysunek 12 przedstawia przykład rozwiązania umożliwiającego sprawowanie kontroli wizualnej nad ilością i miejscem przechowywania segregatorów biurowych. Kolorowa, ukośna linia biegnąca przez grzbiety segregatorów dokładnie określa nie tylko miejsce przechowywania, kolejność, ale również orientację segregatora oraz pozwala na natychmiastowe rozpoznanie np. braku któregoś z nich.
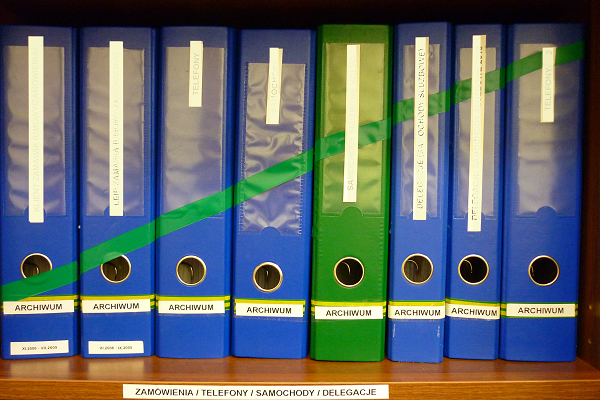
Rys. 12. Przykład kontroli wizualnej nad ilością i miejscem przechowywania segregatorów biurowych w biurze LEI Polska
Zasada 5S pozwala również na wyznaczenie reguł postępowania z dokumentami niepotrzebnymi do codziennej pracy biurowej i administracyjnej. Jak wynika z wykresu przedstawionego na szkicu poniżej, jedynie ok. 10 % dokumentów używanych jest po upływie 6 miesięcy od ich utworzenia. Jeszcze mniejszy odsetek dokumentacji używany jest po 12 miesiącach i wynosi zaledwie 1% 4. Liczby te stoją często w sprzeczności ze sposobem przechowywania tej dokumentacji – zamiast sortować niepotrzebne dokumenty i informacje lepiej jest określić zasady zapobiegania ich zbędnemu gromadzeniu w „pierwszoplanowym” miejscu pracy (np. na twardym dysku). Zalecane jest tutaj utworzenie właściwego archiwum, ułatwiającego codzienną pracę poprzez odchudzenie miejsca pracy z rzadko używanych dokumentów.
Tablica 5S
Procesowi wdrażania systemu 5S powinno towarzyszyć wizualne odzwierciedlenie postępów, co zwykle przybiera formę tablicy. Prezentując obowiązujące standardy, wyniki audytów, procedury związane z systemem itp. pełni ona funkcję centrum informacji dla pracowników. Umieszczona w dostępnym, widocznym miejscu, pozwala śledzić postępy, które są dokumentowane na wykresach i zdjęciach, wpływając tym samym na zwiększenie motywacji do doskonalenia oraz kształtowanie właściwych postaw wśród pracowników. Dostarcza ponadto niezbędnej wiedzy na temat obowiązującego systemu i pozwala zrozumieć rządzące nim reguły. Na poniższym rysunku umieszczono przykład tablicy 5S używanej w siedzibie LEI Polska.
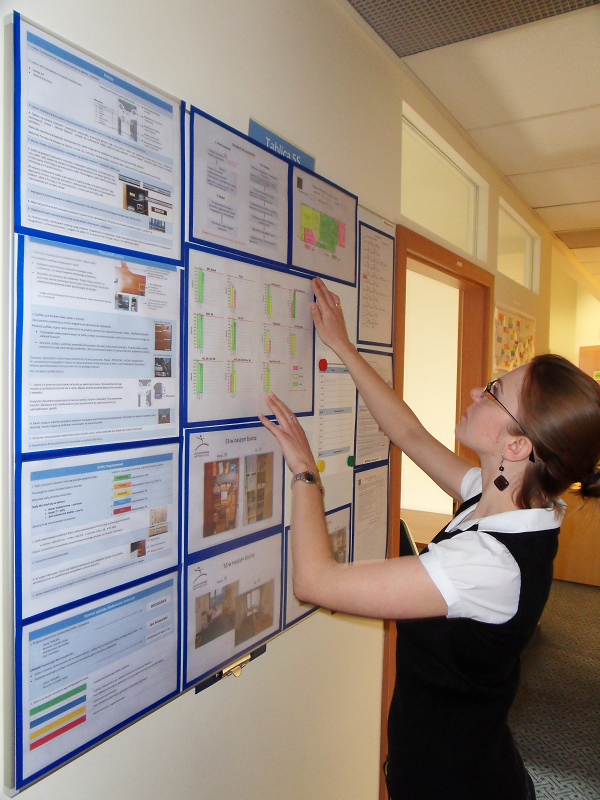
Rys. 13. Tablica 5S w biurze LEI Polska
Korzyści wynikające z odpowiedniego wdrożenia 5S
Profity wynikające z wdrożenia technik i metod 5S podzielić można na dwie grupy. Pierwsza z nich obejmuje bezpośrednie zyski dla osób pracujących na objętych procesem ciągłego doskonalenia stanowiskach, druga grupa wyraża korzyści dla samego przedsiębiorstwa.
Wśród korzyści z wdrożenia 5S dla pracowników wymienić należy m.in.:
- wzrost bezpieczeństwa pracy poprzez lepszą organizację wyposażenia i konfiguracji stanowiska oraz eliminację potencjalnych zagrożeń,
- podniesienie standardów jakości pracy,
- łatwiejszą pracę dzięki zwiększeniu ergonomii stanowiska pracy,
- wzrost wpływu na kształtowanie własnego środowiska pracy, pociągający za sobą wyższe poczucie świadomości i identyfikacji z miejscem pracy,
- wyższą satysfakcję i lepszą atmosferę pracy,
- stabilność tempa pracy poprzez ograniczenie zakłóceń i wdrożenie standardów.
Lista potencjalnych korzyści z wdrożonych rozwiązań 5S dla samego przedsiębiorstwa obejmować będzie np.:
- wyższą jakość produktów poprzez podniesienie standardów i stabilizację stanowisk pracy,
- obniżenie kosztów produkcji dzięki identyfikacji i eliminacji marnotrawstwa,
- polepszenie wizerunku przedsiębiorstwa,
- mniejszą potrzebną powierzchnię produkcyjną i administracyjną,
- osiągnięcie stabilności i wyższego stopnia realizacji zleceń produkcyjnych i administracyjnych, a tym samym podniesienie stopnia satysfakcji klienta,
- skrócenie czasów przestojów powodowanych zakłóceniami związanymi ze złą organizacją stanowisk pracy,
- lepszą kontrolę nad przebiegiem procesu dzięki wprowadzeniu narzędzi kontroli wizualnej.
Podsumowanie
5S jest podstawowym narzędziem Lean Management, pozwalającym nie tylko na stworzenie i utrzymanie dobrze zorganizowanych stanowisk pracy, ale przede wszystkim na zwiększenie stabilności pracy na tych stanowiskach. Ściśle określone i stałe miejsca przechowywania narzędzi, przyrządów, dokumentów i innych przedmiotów pracy, ustalone rutyny postępowania, właściwa prezentacja materiału dla pracowników produkcyjnych, przewidywalna wydajność oraz wizualna kontrola nad procesami, stanowią dobrą podstawę do wdrażania bardziej zaawansowanych rozwiązań Lean. Techniki 5S umożliwiają również pełniejszą integrację pracowników w działania przedsiębiorstwa, a poprzez aktywne wspieranie reorganizacji własnych stanowisk pracy dają możliwość wykorzystania umiejętności i zaangażowania w procesy ciągłego doskonalenia. Dodatkową zaletą wdrożenia 5S są zazwyczaj niewielkie koszty implementacji zasad 5S, co również w znacznym stopniu przyczynia się do pozytywnych zmian ogólnie pojmowanej kultury organizacyjnej przedsiębiorstwa.
Aby dowiedzieć się więcej na temat wdrażania systemu 5S, przeczytaj mi.in. książkę Arta Byrne’a Jak wdrożyć Lean. Książka ukazała się nakładem Wydawnictwa Lean Enterprise Institute Polska i jest dostępna w księgarni internetowej leanbooks.pl.