Heijunka – poziomowanie produkcji
Panuje błędne przekonanie – być może wywodzące się wprost z idei produkcji ssącej – że Toyota montuje samochody w kolejności, w jakiej zamawiają je klienci. Pewnego dnia Toyota chciałaby pewnie osiągnąć ten rodzaj elastyczności w produkcji (a także uregulować popyt na rynku). Jednakże dzisiaj zmaga się z produkcją według wypoziomowanego harmonogramu w wielu swoich procesach montażowych. Schemat na poniższym rysunku przedstawia w uproszczony sposób podstawową „mechanikę” heijunka, czyli poziomowanie procesu montażowego.
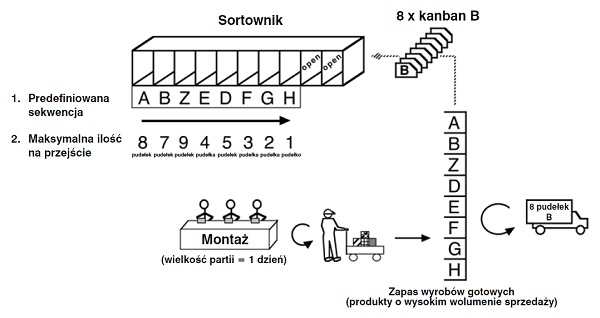
Schemat poziomowania z wykorzystaniem heijunki
Harmonogram produkcji – w tym przypadku karty kanban, które zaczynają krążyć w chwili, gdy klienci pobierają wyroby gotowe z magazynu – nie jest wysyłany bezpośrednio do procesu montażu. Zamiast tego karty przekierowywane są przez pewnego rodzaju sortownik przedstawiony na rysunku w formie skrzynki. Sortownik ten poziomuje zazwyczaj dwa elementy: warianty oraz ich ilość.
- Poziomowanie wariantów. Sortownik ustawia zamówienia klienta (karty kanban) w ustalonej sekwencji według typów. Sekwencja może być wybrana na przykład tak, aby zminimalizować czas przezbrojeń lub aby rozbić duże partie i rozłożyć je na cały dzień. W tym przypadku ustalona sekwencja to A→B→Z→E→D→F→G→H. Dwie dodatkowe przegródki w sortowniku na rysunku są puste i przeznaczone dla detali o niskim wolumenie, które są zamawiane okazjonalnie. Proces montażu będzie usiłował produkować w tak zadanej sekwencji. Zakładany czas realizacji całej sekwencji zależy od wielkości partii. Jeżeli na przykład proces jest w stanie przezbrajać się na tyle często, aby produkować jednego dnia wszystkie typy (co określane jest jako „każda część każdego dnia”), wtedy partia produkcyjna każdego detalu będzie równa jeden dzień. W takim przypadku proces będzie próbował wykonać codziennie całą sekwencję i rozpocznie ją od początku kolejnego dnia.
- Poziomowanie ilości. Sortownik określa także maksymalną ilość każdego typu, która powinna zostać wyprodukowana podczas „przejścia sekwencji”. Ilość ta oparta jest na wielkości pojedynczej serii produkcyjnej oraz bieżącym zapotrzebowaniu klienta. Jeżeli wielkość partii wynosi jeden dzień, to maksymalna ilość wykonywana podczas jednego przejścia przez sekwencję produkcyjną powinna odpowiadać średniemu dziennemu zapotrzebowaniu na dany produkt. W przykładzie z rysunku średnie dzienne zapotrzebowanie na produkt A = 8 pudełek, B = 7 pudełek, Z = 9 pudełek i tak dalej. Na rysunku widać, że klient zakupił osiem pudełek wyrobu B, pobierając je z magazynu, co sprawiło, że w obiegu pojawiło się osiem kanbanów. Jednakże, zgodnie z wzorcem poziomowania wyznaczonym przez sortownik, bieżące średnie zapotrzebowanie na produkt B wynosi siedem pudełek, więc proces powinien wyprodukować maksymalnie siedem pudełek B przed przezbrojeniem się na wyrób Z. Ósmy kanban na produkt B powinien zostać uzupełniony podczas kolejnego „przejścia przez sekwencję”.
W tym momencie, z perspektywy procesu montażowego, wysiłek Toyoty, mający na celu wypoziomowanie produkcji, staje się sprzeczny z intuicją. Wyobraź sobie, że kierownik montażu trzyma w dłoni osiem kart detalu B, proces montażu wytwarza właśnie produkt B, wszystko idzie świetnie, a my mówimy mu, że powinien wyprodukować jedynie siedem pudełek B, a następnie przejść na produkcję wyrobu Z.
Jaka jest przesłanka takiej decyzji? Po co to wszystko?
Dwiema dobrze znanymi przyczynami poziomowania produkcji w procesie montażu są: możliwość obsługi wielu różnych klientów w krótkim czasie oraz ograniczenie „efektu bicza”, zwanego też „efektem Forrestera”. Stanowi on, że każda nierównomierność w procesie produkcji na montażu stopniowo wzrasta, w miarę jak popyt przenoszony jest na procesy w górze strumienia wartości. Skoro procesy w górze strumienia muszą mieć wystarczający zapas, aby pokryć skoki zapotrzebowania, wielkość zapasu – a co za tym idzie również czas przejścia – w strumieniu wartości będzie niższa, gdy znajdujący się w dole strumienia wartości montaż będzie wypoziomowany. Z tego też powodu poziomowanie na montażu jest często warunkiem koniecznym do wprowadzenia kanbanów do procesów w górze strumienia wartości, ponieważ bez tego oparte na kanbanach magazyny w górze strumienia (czyli supermarkety) musiałyby przechowywać niedopuszczalnie duże ilości zapasów.
W prezentowanym przykładzie klient zamówił osiem pudełek wyrobu B, czyli o jedno pudełko więcej, niż wynosi jego średnie dzienne zapotrzebowanie. Zakłada się, że za jakiś czas klient będzie nabywał ilość średnią, a więc jeżeli dziś zakupił jedno dodatkowe pudełko, w najbliższej przyszłości kupi o jedno pudełko mniej. Jeżeli montaż miałby od razu wyprodukować dodatkowe pudełko, przekazałby do procesów w górze strumienia wartości sygnał o skoku zapotrzebowania, który uległby wzmocnieniu i wygenerował dodatkowe koszty w tych procesach.
„Wygładzanie” działań produkcyjnych jest główną przesłanką stojącą za koncepcją poziomowania, czyli heijunka. Jednak pomimo wielu prób, nigdy nie udało mi się jej długo utrzymać. Nie udaje się to także w wielu fabrykach, które odwiedzam. Zrozumiałem, jak zaprojektować sekwencję poziomowania i wielkość partii na wzór Toyoty, ale po krótkim czasie musieliśmy odchodzić od założonej sekwencji z powodu problemów i szybko wracaliśmy do częstych zmian harmonogramu, gaszenia pożarów i nadprogramowych wysyłek z powodu opóźnień. Wydawało nam się, że Toyota doświadcza mniejszej ilości problemów i jest bardziej zdyscyplinowana w trzymaniu się wypoziomowanego harmonogramu. Ale jak to jest możliwe? Odpowiedź przyszła do mnie za sprawą dwóch wydarzeń.
Kiedy odwiedziłem po raz drugi fabrykę w południowych Niemczech, kierownik planowania produkcji powitał mnie wściekłym wyrazem twarzy i okrzykiem: „Proszę zabrać stąd Pańską koncepcję poziomowania!”. Podczas mojej pierwszej wizyty ustaliliśmy wypoziomowaną sekwencję dla procesu montażu, ale, jak zwykle, nie przetrwała ona zbyt długo. „Mamy ciągły niedobór części do produkcji”, powiedział do mnie menedżer, „więc jeżeli staramy się trzymać ustalonej sekwencji, tracimy cenną zdolność”. Musiałem się z tym zgodzić.
Kierownik pokazał mi program komputerowy do harmonogramowania, który został opracowany i zastosowany w zastępstwie heijunki. Codziennie do programu wprowadzane są zamówienia klienta, stany magazynowe oraz dostępność części, a na podstawie tych informacji generowany jest plan produkcji na następny dzień. „Widzi pan”, wyjaśnił kierownik, „to jest harmonogram produkcji, który jesteśmy w stanie wykonać”. Rzecz jasna, harmonogram montażu był inny każdego dnia.
Do kolejnego zdarzenia doszło nieco później, ale jeszcze w tym samym tygodniu. Jadłem kolację z człowiekiem z Toyoty, który w pewnym punkcie rozmowy powiedział: „Cóż, w Toyocie robimy wiele rzeczy tak, aby powstał wzorzec działania”. W tym momencie zrozumiałem wreszcie, o co w tym wszystkim chodzi.
Artykuł jest fragmentem książki Toyota Kata. Książka ukazała się nakładem Wydawnictwa Lean Enterprise Institute Polska i jest dostępna w księgarni internetowej leanbooks.pl.