Lean Manufacturing w Remy Automotive Poland. Osiągnięcia i problemy
W referacie omówiono narzędzia Lean Manufacturing wdrożone w Remy Automotive Poland. Szczególnie skupiono się na zależnościach pomiędzy elementami techniczno – organizacyjnymi systemu a reakcjami pracowników i budowaniem załogi otwartej na zmiany. Omówiono wynikające z tego problemy oraz sposoby ich rozwiązania. W ostatniej części przedstawiono, jakie efekty zostały uzyskane w zakresie wdrażania systemu oraz osiągnięte wyniki ekonomiczne i jakościowe.
Wstęp
Remy Poland na poprzednich konferencjach Lean Manufacturing miała możliwość przedstawiania poszczególnych elementów wdrażanego systemu Lean: budowa celek na II konferencji i przedstawieniu przepływu ciągłego na IV konferencji. Obecnie postanowiliśmy omówić dokonane w ciągu sześciu lat przemiany w sposób całościowy ze zwróceniem szczególnej uwagi na prawidłowości systemowe, pokazanie problemów i sposoby ich przezwyciężania oraz omówienie osiągniętych wyników.
1. Informacja o firmie
Remy Automotive Poland jest częścią międzynarodowej Grupy Remy International Inc. z główną siedziba w Anderson stan Indiana USA. Początki firmy sięgają 1896 roku, gdy dwaj bracia Franka i Perry Remy założyli Remy Electronic Company. W roku 1918 firma przekształciła się w Delco Remy i stała się dywizją General Motors. W roku 1994 cześć związana z maszynami wirującymi wydzieliła się z General Motors jako całkowicie niezależna firma Delco Remy. Od roku 2004 nazwa firmy została zmieniona na Remy International, Inc.
Remy posiada 45 zakładów w jedenastu krajach, niemal na wszystkich kontynentach: USA, Meksyk, Brazylia, Indie, Chiny, Korea, Tunezja, Wielka Brytania, Węgry, Belgia, Polska. Remy zatrudnia około 8300 pracowników w tym 250 inżynierów. Posiada trzy ośrodki badawczo-rozwojowe: w USA, Polsce i Korei. Główne produkty to rozruszniki, alternatory, przekładnie, silniki elektryczne. Roczna sprzedaż przekracza 1,2 miliard dolarów. Remy działa zarówno na rynku pierwszego montażu (OE) jak również ma duży udział w rynku wyrobów regenerowanych elektrotechniki motoryzacyjnej i obsługuje rynek wtórny (AM).
Remy Automotive Poland jest zlokalizowana w Świdnicy i jest kontynuacją założonej w 1947 roku firmy przez wiele lat występującej pod nazwą Elmot. Program produkcji Elmot-u od początku zawierał rozruszniki, prądnice i następnie alternatory. Mamy w tym zakresie duże doświadczenie zarówno produkcyjne jak i rozwojowe. Posiadaliśmy własny Dział Konstrukcyjny i Laboratorium Badawcze. Na ich bazie powstało jedno z trzech centrów Inżynieryjnych Remy International. Po przejęciu Elmotu w roku 2000 przez firmę Remy ( w tym czasie miała nazwę Delco Remy) profil produkcji został zachowany i nadal produkujemy rozruszniki i alternatory. Oczywiście, korzystając z zasobów firmy globalnej znacznie zmodernizowaliśmy zarówno gamę produkowanych wyrobów jak również techniki wytwórcze oraz dotarliśmy do nowych, globalnych klientów. Naszymi odbiorcami na dzień dzisiejszy są tacy klienci jak: Saab, Opel, Fiat, Bosch, Perkins, Daimler Chrysler i wielu innych. Remy Poland posiada certyfikat Systemu Jakości zgodnego z ISO/TS 16949 i Systemu Ochrony Środowiska ISO 14 001.
2. Przebudowa bazy wytwórczej
W grupie Remy zasady Lean Manufacturing są wdrażane od 1999 roku. Pierwsze szkolenia i działania inicjujące prowadził współautor takich książek jak „Lean Thinking” i „Odchudzanie Firm” Jim Womack. Działania kontynuowano korzystając z pomocy firm doradczych. Celem było zaczerpnięcie od samego początku najlepszej wiedzy o Lean i zrobienie jak najmniejszej liczby błędów. Z perspektywy czasu wydaje się, że takie podejście jest chyba najskuteczniejsze, gdyż daje od początku szanse robienia dobrze właściwych rzeczy. Dziś wiemy, że na drodze wdrażania narzędzi Lean można popełnić wiele błędów podchodząc do tego w sposób przypadkowy i wdrażając przypadkowe narzędzia Lean bez wystarczającej wiedzy i perspektywicznego planu.
Początki wdrażania Lean w Remy Poland (Elmot) sięgają praktycznie tego samego okresu. Pierwsze inicjujące szkolenie odbyło się pod koniec roku 1999 i było prowadzone przez firmę consultingowa Rick’a Harrisa z USA. Następnie firma ta opiekowała się wdrażanym programem poprzez cykliczne szkolenia i ocenę wdrażanych tematów oraz wprowadzanie coraz szerszej gamy narzędzi LM. Równocześnie Elmot otrzymał wsparcie od kolegów z USA, którzy wcześniej zdobyli doświadczenie w tym zakresie. Wspólnie opracowaliśmy kilka celek i wdrożyliśmy je do produkcji. Pierwsze celki wdrażano na montażu, potem opracowano również celki na obróbce mechanicznej detali. Zakończone sukcesem wdrożenie pierwszych celek było najlepszą zachętą do rozszerzania działań na kolejne obszary.
W tym miejscu chcemy zwrócić uwagę, że pierwsze wdrożenie nowej idei musi być specjalnie przygotowane. Szczegółowe analizy oraz pomoc konsultantów jest tu bardzo istotna, bo nieadekwatne do oczekiwań efekty mogą na długi czas zamknąć w mentalności załogi drogę do kolejnych etapów wdrożeń. Można oczywiście w takiej sytuacji dalej wdrażać zatwierdzony przez kierownictwo plan, ale bez akceptacji i zaangażowania załogi, które płynie z obserwacji osiąganych wyników działanie takie są znacznie trudniejsze i mogą się nie powieść. Jest to tym ważniejsze przy wdrażaniu Lean, że opiera się ono na zrozumieniu zasad i współudziale całej załogi
Mówiąc o początkach wdrażania LM w Remy Poland mamy na myśli głównie organizację celek produkcyjnych z przepływem jednej sztuki. Był to pierwszy widoczny na produkcji element Lean, który na dość długi czas stał się podstawą naszych działań przy wdrażaniu całego systemu. W naszym zakładzie konsekwentnie używamy określenia „celka produkcyjna” dla wyraźnego odróżnienie „starej organizacji” składającej się z linii produkcyjnych, gniazd i komórek od „Lean organizacji” z celkami produkcyjnymi, gdzie celka od razu znaczy przepływ jednej sztuki, przemieszczanie pracowników, brak zapasów produkcji w toku itd.
Dobrze zorganizowana celka produkcyjna jest bardzo wdzięcznym polem do wizualnego pokazywania eliminacji podstawowych strat ( Rys.1 Celka produkcyjna)
- redukcja zapasów produkcji w toku, oszczędności sięgające nawet dziewięćdziesięciu kilku procent (Rys.2 i 3 Zapasy przed i po zmianie);
- wyeliminowania wszelkich oczekiwań pracownika na zakończenie cyklu – przemieszczanie pracowników wzdłuż procesu pozwala wyeliminować wszystkie, nawet najmniejsze oczekiwania na zakończenie cyklu; pozwala to zwiększyć wydajności pracy od kilku do kilkunastu procent (bez inwestowania w nowe oprzyrządowanie);
- znaczne zmniejszenie powierzchni produkcyjnej, poprzez wyeliminowania miejsca na zapasy produkcji w toku, oraz specjalne ustawienie stanowisk pracy w kształcie wydłużonej liter U osiągnięto oszczędność powierzchni produkcyjnej od kilku do nawet 50%.
(Rys.4 i 5 Powierzchnia zajmowana przed i po zmianie)
- poprawa jakości – poprzez wykonywanie pojedynczego wyrobu od początku do końca istnieje większa szansa szybszego ujawnienia błędów, dzięki przepływowi jednej sztuki błąd przed ujawnieniem można popełnić na jednym, lub max kilku wyrobach, gdy w celce pracuje kilka osób, a nie po wykonaniu całej partii często wielkości kilkuset sztuk;
- znaczne skrócenie czasu przejścia, możliwa szybka reakcja na zmienne potrzeby klienta, pośrednio przyczynia się do zmniejszenia zapasów;
- ograniczenie przemieszczanie materiałów – przy przepływie jednej sztuki w celce zostaje całkowicie wyeliminowany transport międzyoperacyjny, nie ma przemieszczania partii wyrobów pomiędzy operacjami przy użyciu wózków.
Dobrze opracowana i wdrożona celka daje możliwość łatwego zaobserwowanie tych efektów (bez mała dotknięcia ich) i to jest najlepsza zachęta do dalszego działania. Pozwalało to w łatwiejszy sposób wprowadzać zarówno kolejne narzędzia Lean: standaryzacja, 5S, audity kaskadowe, dostawy na czas, jak również pojęcia typu: Czas Taktu, Czas Cyklu, Czas Przejścia, przepływ, pociąganie, Kanban. Wszystkie te narzędzia stawały się „potrzebne” do doskonalenia już działających celek i efekty ich wdrażania były do zaobserwowania prawie natychmiast.
Podstawowym założeniem przy budowaniu pierwszych celek było wykorzystanie istniejącego wyposażenia i technologii do stworzenia nowej organizacji pracy z przepływem jednej sztuki i przemieszczaniem pracownika wzdłuż procesu produkcyjnego. Założenie takie pozwala łatwiej uzyskać akceptację dla działań, które są stosunkowo tanie ( nie inwestujemy w wyposażenia technologiczne) a pozwalają spodziewać się znacznych oszczędności. Rzeczywiste nakłady dla wdrożenia pierwszych celek sprowadzały się do:
- koszt podniesienia niektórych stanowisk, aby umożliwić pracę w pozycji stojącej (tam gdzie pierwotnie była praca w pozycji siedzącej);
- koszt podajników, które dostarczają detale i materiały do rąk operatora a są zasilane z zewnątrz celki;
- zmiana systemu podłączeń mediów ze sztywnego na elastyczny, umożliwiający łatwe usprawnianie jak również przenoszenie celek;
- i w końcu koszt samego przemieszczenia i ustawienia maszyn w celkę.
Kilkanaście pierwszych celek wdrożyliśmy przy takich założeniach, osiągając zakładane efekty przy bardzo ograniczonych nakładach. Technolodzy, którzy wykonali te zadania i mogli sprawdzać w praktyce swoje założenia, osiągnęli ogromne doświadczenie nie do przeceniania przy opracowywaniu nowych produktów i nowych celek z nowym zamawianym wyposażeniem. Skoro można uzyskać tak dobre efekty używając istniejącego wyposażenia i technologii jedynie przez zmiany organizacyjne to, jakie jest pole do popisu, gdy z tą wiedzą i doświadczeniem można zaprojektować od podstaw nowy proces i zamówić do niego odpowiednie, nowe wyposażenie.
Po pierwszych dwóch latach przebudowy tradycyjnych linii i gniazd produkcyjnych w celki z przepływem jednej sztuki przystąpiliśmy równolegle do budowania nowych mocy produkcyjnych w oparciu o koncepcję celki produkcyjnej. Aktualnie cała nasza produkcja wykonywana jest w celkach, których mamy około 60.
Kolejne elementy, które pojawiały się przy wdrażaniu celek to:
- organizacja stanowiska pracy 5S – wyszła od stanowiska pracy i celki, aby przejść na całą powierzchnię produkcyjną, magazyny i biura;
- standaryzacja pracy – przy zaangażowaniu pracownika do wykonywania w jednym czasie nie jednej, ale wielu operacji po kolei dużego znaczenia nabrało szczegółowe opisanie kolejności i niuansów każdej z operacji, tradycyjna technologia wykonania stawała się zbyt mało dokładna i karty standaryzacji ze szczegółowym opisem sekwencji operacji stały się koniecznością, standaryzacja pozwala również zmniejszać zmienność a tym samym ma wpływ na poprawę jakości;
- dostawy materiału na czas;
- system kart Kanban;
- usprawnienia Kaizen.
Chcielibyśmy w tym miejscu zwrócić uwagę, że w naszym przypadku istniała pewna równowaga pomiędzy pchaniem i ssaniem metod i narzędzi Lean. Nie staraliśmy się od początku mieć wdrożonych wszystkich możliwych narzędzi Lean. Kolejne narzędzia pojawiały się poniekąd w sposób naturalny jako odpowiedź na pewne pojawiające się zapotrzebowanie oczywiście częściowo podpowiadane i popychane poprzez szkolenia i analizy działania istniejących rozwiązań. Dobrym tego przykładem jest chociażby SMED, który praktycznie dopiero teraz wdrażamy. Dlaczego tak się stało? Pierwsze szkolenia ze SMED odbyliśmy w roku 2003. Wdrożyliśmy nawet przykłady na dwóch celkach. I na tym wszystko się zatrzymało. Struktura produkcji, dedykowane linie, na których produkowano rzadko zmieniający się asortyment nie stwarzały środowiska do szerszego wdrożenia tej metody. Dziś, gdy zwiększył się asortyment wyrobów wykonywanych na jednaj celce, zwiększyła częstotliwość przezbrojeń i w ten sposób straty produkcji podczas przezbrojeń każą zainteresować się szybkimi technikami przezbrojeń.
Przygotowanie kadry technicznej, nauczenie się metod i sprawne nimi operowanie to jedna strona zagadnienia. Jest to przygotowanie techniczne dające możliwość osiągania dobrych wyników, ale nie są to jeszcze dobre wyniki.
3. Budowanie zespołu
Po drugiej stronie są pracownicy, którzy wykonują operacje i od których wiedzy i zaangażowania zależy ostateczny efekt. Mogą oni pracować dobrze i skutecznie lub nie. Cała załoga musi być postrzegana jako podstawa przy realizującej Lean Manufacturing i głównie od jej zaangażowania zależy czy osiągniemy sukces. Przestrzeganie zasad 5S i standaryzacji pracy, udział w usprawnieniach Kaizen, eliminacja dostrzeżonych błędów, akceptacja zmiany sposobu pracy decydują o końcowym wyniku wszelkich działań.
Dlatego równie ważna, o ile nie ważniejsza, była przebudowa świadomości i postawy wszystkich pracowników od operatora począwszy. Działania te są bardzo istotne, ponieważ błąd popełniony w ustawieniu procesu, przepływie materiału lub standaryzacji można stosunkowo prosto skorygować. Błędy popełnione przy pracy z ludźmi są często nie do naprawienia. Zgubiony zapał czy innowacyjność, utratę wiary w sensowność prowadzonych przemian trzeba często naprawiać latami.
Działania w zakresie przebudowy świadomości załogi i budowy zespołów gotowych do akceptacji zmian odbywają się w naszym zakładzie na kilku płaszczyznach:
- A- Budowanie świadomości poprzez szkolenia i treningi. Wszyscy operatorzy zostali przeszkoleni, oprócz umiejętności czysto zawodowych, w tematyce związanej z podstawami Lean Manufacturing takimi jak organizacja stanowiska pracy 5S, standaryzacja pracy, 7 narzędzi jakości i podstawy rozwiązywania problemów, 7 rodzajów strat i ulepszenia typu Kaizen. Szkoląc wszystkich pracowników z podstaw Lean Manufacturing i sposobów realizacji nowych wymagań pokazywano jednocześnie, jaki wpływ na wyniki ma każdy pracownik i podkreślano, że realizacja tego programu jest jedyną droga utrzymania się na konkurencyjnym rynku motoryzacyjnym;
- B- Informacja podstawą współudziału i współodpowiedzialności. Wszystkie informacje użyteczne dla pracownika: od standaryzacji pracy na stanowisku, poprzez wiedzę o aktualnych wynikach aż do wskaźników na poziomie całego zakładu są dostępne i przedstawione w bardzo czytelnej formie. Standaryzacja pracy wraz z wieloma rysunkami i zdjęciami jest na stanowisku pracy. Aktualne godzinowe wyniki produkcji oraz informacja o pojawiających się problemach umieszczana jest na tablicach produkcyjnych bezpośrednio przy celce. Na tych też tablicach pojawiają się informacje o sposobie rozwiązywania problemów i wdrożonych Kaizen-ach. W pomieszczeniach narad działowych dostępne są informacje o planach produkcji, zagrożeniach wysyłek, problemach z dostawami materiałów itd. W końcu informacja ogólne: plany produkcji, wyniki na poziomie zakładu, zapasy i wiele innych umieszczone są na tablicach zakładowych w dwóch miejscach przy głównej drodze hali produkcyjnej. Informacje te pozwalają pracownikom czuć się współodpowiedzialnym za to, co się dzieje w firmie i przyczyniają się do lepszej komunikacji a przez to do lepszego zrozumienia istoty procesów przebiegających w zakładzie. (Rys.6 i 7 Tablice informacyjne);
- C- Współudział w tworzeniu standaryzacji pracy i rozwiązywaniu problemów. Oprócz wykonywania swoich zadań zgodnie ze standaryzacją pracy pracownicy mają również udział w ostatecznym ustalaniu sposobu pracy. Swoje uwagi, odnośnie przebiegu procesu technologicznego, ergonomii, ewentualnych usprawnień mogą zgłaszać nie tylko do mistrza i technologa, ale również bezpośrednio do wszystkich szczebli zarządzania włącznie z Prezesem (jest do tego dogodna okazja podczas Auditów Kierownictwa wykonywanych codziennie w celkach przez Prezesa firmy). Pracownicy uczestniczą również w rozwiązywaniu bieżących problemów: z jednej strony jako członkowie zespołów rozwiązywania problemów pracujący zgodnie z arkuszem „Scenariusz rozwiązywania problemów”. Prowadzącym taki „Scenariusz…”jest najczęściej technolog lub inż. jakości, ale członkami zespołu są również operatorzy, którzy pracują w miejscu powstania problemu. Z drugiej strony pracownicy uczestniczą również w programie drobnych usprawnień Kaizen. Zgłaszane usprawnienia są również prezentowane w miejscu ich wdrażania.(Rys.8 Prezentacja usprawnień Kaizen);
- D – integracja poprzez wspólne świętowanie i wypoczynek. Pracownicy uczestniczą w wspólnym celebrowaniu szczególnych zdarzeń, typu nagroda jakości, osiągnięcie certyfikatu, spotkania przedświąteczne itp. Corocznie jest organizowany pikniki dla całej załogi z rodzinami. Organizowany tradycyjnie od 34 lat samochodowy Rajd Elmot-Remy, będący Rundą Rajdowych Samochodowych Mistrzostw Polski, jest też ważnym wyznacznikiem tożsamości i dumy pracowników z współudziału w tak prestiżowej imprezie sportowej. (Rys.9 Wspólne świętowanie sukcesów, Rys. 10 Rajd Elmot-Remy).
Suma wszystkich tych działań pozwala krok po kroku budować załogę zaangażowaną we wspólne dobro, otwartą na zmiany i aktywnie uczestniczącą w usprawnianiu procesów produkcyjnych.
4. Problemy i trudności
To, że udało nam się skutecznie wdrożyć tak wiele narzędzi Lean nie oznacza wcale, że nie napotykaliśmy po drodze na trudności. Pierwsze kłopoty rozpoczęły się wraz z wdrażaniem pierwszych celek. Z punktu widzenia pracownika pojawiły się liczne zagrożenia:
- A- Zamiast pracy w pozycji siedzącej praca w pozycji stojącej i przechodzenie od stanowiska do stanowiska. Jest to rzeczywisty problem w szczególności dla pracowników, którzy z dnia na dzień musieli zmienić swoje nawyki i obciążenia. Pracownik, który przez 15 lat pracował w pozycji siedzącej musiał teraz przez osiem godzin pracować w pozycji stojącej. Było to dla niego bardzo duże utrudnienie i powodowało znacznie większe zmęczenie. Po kilku trudnych miesiącach, pracownicy przystosowali się do nowej organizacji i ostatecznie okazało się, że praca zróżnicowana i prowadzona kolejno na kilku stanowiskach, bardziej równomiernie obciąża różne partie ciała i w sumie jest mniej uciążliwa dla pracowników od powtarzalnego, wykonywanego czasami w cyklu 10-15 sek. ciągle takiego samego zestawu ruchów. Dodatkowo do wszystkich celek wprowadzono specjalne maty dla ochrony stawów, co znacznie przyczynia się do zmniejszenia zmęczenie, ale pokazało również pracownikom, że ich głosy są brane pod uwagę i tam gdzie można wprowadzić ułatwienie jest ono wprowadzane. Problem ten praktycznie nie występuje, gdy nowy pracownik od początku startuje w celkowym systemie organizacji pracy;
- B – Zamiast wykonywać jedną operacje trzeba nauczyć się wykonywać kilka a nawet kilkanaście różnych następujących po sobie operacji wykonując kompletny detal, podzespół lub wyrób finalny. Z jednej strony wymaga to od pracownika znacznie większego zaangażowania się zarówno w proces szkolenia jak również podczas codziennej pracy. Z drugiej jednak strony nauczenie się wprawnego wykonywania wielu operacji jest daje pracownikowi poczucie większej własnej wartości. Pracownicy szybko to zrozumieli i nie stanowi to dziś żadnego problemu, tym bardziej, że w ramach wizualizacji informacji wprowadziliśmy matryce szkoleń, które ukazują umiejętności każdego pracownika a są umieszczone na tablicach w pokojach spotkań załogi i każdy widzi, kto, potrafi i z jaką wprawą wykonywać więcej różnorodnych operacji. Rozleglejsze umiejętności są również brane pod uwagę przy ocenach pracowników;
- C – Zamiast wykonywania pracy wg swoich własnych metod (oczywiście w ramach obowiązującej technologii) pracownik musi ściśle przestrzegać opracowaną standaryzację pracy. Standaryzowane wykonywanie pracy rodzi pewną monotonię i automatyzm, ale daje pewność, że osiąga się możliwie najlepszą i powtarzalną jakość i wydajność. Pewną kompensata dla pracownika jest możliwość zgłaszania wniosków o zmianę standaryzacji, jeżeli pracownicy maja propozycje lepszego wykonywania niektórych czynności. Z drugiej strony praca standaryzowana na zorganizowanym zgodnie z wymogami ergonomii stanowisku jest bezpieczniejsza i mniej uciążliwa. Osiągana jest również większa wydajność pracy, ale za tę wydajność odpowiada przede wszystkim organizacja i przygotowanie stanowiska pracy a nie bezpośrednio pracownik. Pracownicy wynagradzania są w systemie godzinowym i nie są wprost uzależnieni od osiągniętej wydajności pracy. W przypadkach nie osiągnięcia założonej wydajności nigdy nie rozpoczyna od oskarżania pracownika. Oczywiście pracownik powinni dokładać wszelkiej staranności we właściwym wykonywanie pracy, ale w przypadku nie osiągania założonej wydajności poszukiwania niepowodzenia rozpoczynają się od powtórnej analizy standaryzacji, organizacji pracy i tam poszukiwane są też rozwiązania. Najważniejsze jest ustalenie przyczyn, usunięcie ich i zapewnienie, że tego typu sytuacja nie powtórzy się w przyszłości;
- D – Zamiast raportować dzienną wielkość produkcji trzeba spływ produkcji i występujące problemy raportować, co godzinę. Ostatni blok spraw to jest właściwie problem z ujawnianiem prawdziwych problemów występujących w produkcji. Planowanie i raportowanie produkcji odbywa się w Remy Poland z podziałką godzinową. Żeby miało to sens konieczne jest, aby zarówno wyniki godzinowej produkcji jak również zapisywane zakłócenia w przebiegu procesu były zgodne z rzeczywistością. Na tym polu było szczególnie wiele do zrobienia. Na początku pracownicy mieli tendencje do „wygładzania zapisów”, czyli zapisywania tego, co im się wydawało, że jest oczekiwane a nie wpisywanie prawdziwych informacji. Jest oczywiste, że takie dane są nikomu nieprzydatne. Aby dokonywać rzetelnej analizy problemów potrzebne są rzetelne dane. Dlatego, podobnie jak przy poprzednim punkcie, trzeba było przekonać pracowników do wpisywania rzetelnych danych i uwolnić ich od obaw, że jeżeli pojawi się zapis o nie wykonaniu planu lub problemach jakościowych albo np. awarii maszyny to winny będzie ten pracownik, który ujawnił i zapisał problem. System auditów, rozwiązywanie problemów a nie poszukiwanie „winnych” pozwoliły powoli uwolnić pracowników od starych, złych nawyków i obaw. Potrzeba było wielkiej staranności i wytrwałości, konsekwencji w tropieniu przyczyn a nie szukaniu winnych, aby zaczęto ujawniać coraz więcej problemów. Jest to bardzo ważna część przemian i wyszukiwania strat. Żeby można było usunąć stratę trzeba poznać jej rzeczywistą przyczynę. Ale jeszcze wcześniej trzeba w ogóle wiedzieć, że taka strata lub problem występuje. Mamy przekonanie, że obecnie przedstawiane dane są w znakomitej większości prawdziwe i dzięki temu umożliwiają poszukiwanie prawdziwych przyczyn problemów i ich rozwiązywanie.
5.Co mamy dziś, jakie efekty osiągnęliśmy?
Budując kolejno narzędzia i techniki LM nie stworzyliśmy kolorowej mozaiki, która dryfuje w niewiadomym kierunku. Staraliśmy się zbudować spójny system kierują się celami strategicznymi określonymi przez Zarządu Remy International:
- zero wypadków;
- zero defektów;
- zero zaległości w dostawach;
- zero nadmiernych zapasów.
Osiąganie tych celów wspiera Remy Operation System składający się z czterech filarów:
- EHS (BHP) Best Practice
- Komisje EHS&S (BHP);
- Działania „Zależy nam”;
- Internetowe raportowanie zdarzeń;
- Działania po wypadkowe;
- Podstawy ergonomii stanowisk pracy;
- Audity Kierownictwa EHS&S (BHP);
- Audity techniczne EHS&S (BHP).
- Quality Best Practice
- Praca standaryzowana;
- Jakość u źródła;
- Error Proofing (odporność na błędy);
- Pierwsza – ostatnia sztuka;
- Polityka nie naprawiania;
- 7 Narzędzi Jakości;
- Scenariusz Rozwiązywania Problemów;
- PFMEA;
- Six Sigma Black Belts.
- Manufacturing Best Practice
- Celki produkcyjne;
- Usprawnienia Kaizen;
- Godzinowy rejestr spływu produkcji;
- Karta trendów;
- 5S organizacja stanowisk pracy;
- Audity kaskadowe.
- Material Movement Best Practice
- Mapa Strumienia Wartości;
- PFEP (Plan For Every Part) – PDKC (Plan Dla Każdej Części);
- Czas Taktu;
- Dostawy na czas;
- Supermarket;
- Kanban;
- Minimarket;
- Przepływ jednej części.
Wdrażając system Lean przebudowaliśmy bazę wytwórcza, staraliśmy się zmieniać postawy pracowników, upowszechniać pracę zespołową, uprościliśmy struktury, przybliżyliśmy obsługę do stanowiska pracy, przenieśliśmy cześć biur w bezpośrednie sąsiedztwo hali produkcyjnej. Wszystko to można robić kierując się podstawową zasadą Lean – to, co nie przysparza wartości powinno być eliminowane, bo jest stratę.
Omawiając przemiany organizacyjne należy zwrócić uwagę na następujące fakty: Elmot w 2000r.
- głębokie przetwarzanie – wykonywanie detali, podzespołów i wyrobów finalnych;
- linie produkcyjne, gniazda wg podziału technologicznego;
- duże odległości pomiędzy kolejnymi fazami procesu, duże partie, wysokie zapasy.
Remy w 2006r.
- koncentracja na montażu podzespołów i wyrobów finalnych;
- zorganizowanie całej produkcji w celkach z przepływem jednej sztuki;
- zamknięcie na jednej powierzchni całego procesu związanego z jedną rodziną wyrobów.
Osiągnięte wyniki organizacyjno-ekonomiczne:
Elmot 2000 | Remy 2006 | ||
---|---|---|---|
zatrudnienie | 710 | 455 | osób |
sprzedaż roczna | 72 | 220 | mln zł |
sprzedaż na 1 zatrudnionego | 101 | 483 | tyś zł |
powierzchnia produkcyjna | 40 | 15 | tyś. m. kw. |
Osiągnięte wyniki jakościowe: Jakość Pierwszego Wykonania w PPM (FTQ – First Time Quality) Początek 2003r.: wskaźniki jakościowe mocno zróżnicowane i sięgały nawet 45.000 PPM przy średniej ponad 20.000 PPM
Koniec 2005 r. : wskaźniki nie przekraczają 3500 PPM przy średniej około 1300 PPM
Oznacza to około 15 krotną poprawę w ciągu 3 lat.
Osiągnięte wyniki są w dużej części efektem wdrażania Lean Manufacturing, ale nie tylko. Działania te wspierane są oczywiście różnymi innymi inicjatywami takimi jak Six Sigma, System Jakości, System Ochrony Środowiska, działania w zakresie BHP, zmiana struktury organizacyjnej i inne. Najważniejsze jest jednak, aby wszystkie te działania dopasowywać do siebie w taki sposób by nie stawały się konkurencyjne, skoncentrowane na wybranych odcinkach. Każde działanie odcinkowe musi być zawsze oceniane z punktu widzenia efektów dla całej firmy.

Rys.1. Przykład celki produkcyjnej.

Rys.2. Zapasy przy tradycyjnej organizacji.

Rys.3. Zapasy w celce.

Rys.4. Powierzchnia potrzebna przy tradycyjnej organizacji.

Rys.5. Powierzchnia potrzebna przy organizacji celki.

Rys.6. Informacje o zakładzie.
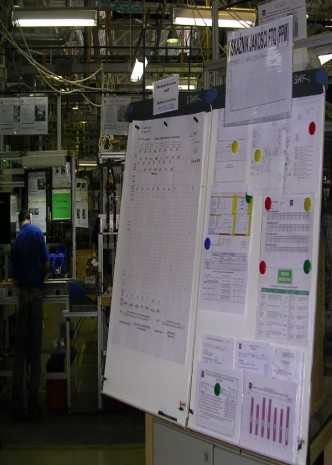
Rys.7. Informacje z celki.
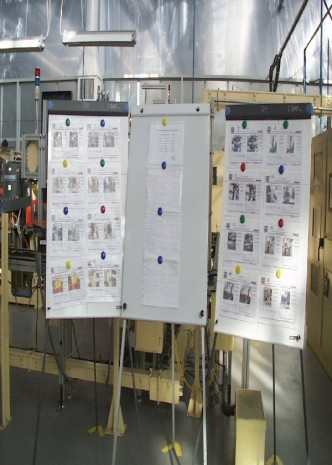
Rys.8. Prezentacja usprawnień Kaizen.

Rys.9. Wspólne świętowanie sukcesów – General Motors przyznał Remy tytuł Dostawca roku 2004.

Rys.10. 34 Rajd Elmot-Remy.
Janusz SZOSTAK
Andrzej BIELEWSKI
__________________
REMY AUTOMOTIVE
POLAND Sp. Z o.o.
Szarych Szeregów 16/18
58-100 Świdnica