TPM – kompleksowe produktywne utrzymanie ruchu
Maksymalizacja efektywności maszyn przez zaangażowanie wszystkich pracowników firmy
Dowiedz się więcejSystem kompleksowego produktywnego utrzymania ruchu (TPM) to całościowe podejście pozwalające zwiększyć efektywność maszyn i urządzeń. Przy zastosowaniu tej koncepcji możliwe jest osiągnięcie nie tylko bardzo niskiej awaryjności maszyn, ale także wyeliminowanie wszelkich strat obniżających ich wydajność przy stosunkowo niewielkich nakładach finansowych. W porównaniu z tradycyjnym podejściem, w którym za funkcjonowanie maszyn i urządzeń odpowiada personel utrzymania ruchu, w TPM zadania związane z maksymalizacją efektywności maszyn i redukcją strat przypisane są wszystkim pracownikom firmy. TPM pozwala na skuteczne zarządzanie działaniami planowej konserwacji w przedsiębiorstwie oraz skrócenie czasu reakcji na awarie i przestoje maszyn.
Podczas szkolenia uczestnicy nauczą się, jak zaprojektować i wdrożyć skuteczne narzędzia autonomicznego oraz prewencyjnego utrzymania ruchu, zaobserwują również ich efektywne zastosowanie w praktyce. Poznają też podstawowe wskaźniki stosowane w podejściu TPM oraz procesy szybkiego zgłaszania i usuwania awarii, a także sposoby zarządzania maszynami kluczowymi oraz częściami zamiennymi do nich.
LICZBA GODZIN SPĘDZONYCH NA HALI PRODUKCYJNEJ PODCZAS SZKOLENIA: 4h
Adresaci szkolenia
Osoby związane z utrzymaniem ruchu i produkcją w przedsiębiorstwie: liderzy, brygadziści, mistrzowie, kierownicy produkcji, inżynierowie procesu, kierownictwo i pracownicy działu utrzymania ruchu.
Korzyści dla uczestnika
- Umiejętność wskazania przyczyn problemów przy wprowadzaniu TPM
- Umiejętność obliczenia i analizy wskaźnika OEE
- Umiejętność wskazania czynności, które powinny trafić do autonomicznej konserwacji
- Umiejętność przygotowania karty autonomicznej konserwacji
- Umiejętność definiowania priorytetów w utrzymaniu ruchu dla maszyn i urządzeń (klasyfikacja ABC)
- Umiejętność klasyfikowania ewentualnych awarii czy uszkodzeń
- Umiejętność analizy stanu obecnego w procesie usuwania awarii i wskazanie możliwych udoskonaleń
- Umiejętność określania wymaganych zasobów utrzymania ruchu w odniesieniu do danej grupy urządzeń
- Umiejętność identyfikacji i eliminacji źródeł zanieczyszczeń i miejsc trudno dostępnych
- Po szkoleniu uczestnik otrzymuje od prowadzącej/prowadzącego pakiet przydatnych materiałów w postaci m.in. arkuszy, tablic, prezentacji, grafik, wideo, raportów, artykułów itp.
Opinie uczestników
Korzyści dla firmy
- Zmniejszenie liczby awarii i nieplanowanych przestojów
- Obniżenie liczby defektów związanych ze stanem maszyn oraz mikroprzestojów
- Podniesienie jakości produktów i bezpieczeństwa pracy
- Zmniejszenie nakładów na utrzymanie ruchu dla maszyn o niskim priorytecie
- Skrócenie czasu reakcji na problem pojawiający się na urządzeniach kluczowych
- Skrócenie czasu konserwacji maszyn kluczowych dla procesu
- Redukcja czasu usuwania awarii
- Optymalizacja kosztów utrzymania ruchu
Uzyskaj do 80% dofinansowania do naszych warsztatów i szkoleń
Jeśli Twoje przedsiębiorstwo należy do sektora MSP, teraz możesz zdobyć aż do 80% dofinansowania do naszych usług. Dowiedz się więcej >>
Certyfikat
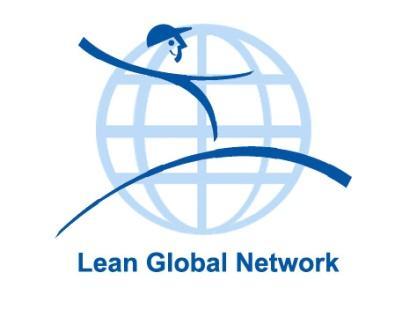
Sygnowany Lean Global Network
Program
Program szkoleniaPDF, 0.4 MB
Terminy szkoleń
Data | Nazwa firmy i miejsce | Cena netto | Stan zapisów | |
---|---|---|---|---|
15-16.10.2025 | ![]() Poledno | 2400 zł* | Zapisy w toku | Zapisz się |
*Cena EARLY BIRD obowiązuje przy zgłoszeniu do 30.09.2025r. Cena regularna wynosi 3500 zł.
Prowadzący
W zależności od terminu, szkolenie będzie prowadzone przez jednego ze wskazanych poniżej ekspertów.
Bartłomiej Kotlarski
Doświadczenie menadżerskie
Posiada ponad dwudziestoletnie doświadczenie w Lean Management oraz zarządzaniu działami operacyjnymi w międzynarodowych korporacjach, głównie w sektorze motoryzacyjnym, chemicznym i elektronicznym. Swoją karierę rozpoczął w 2004 roku w Toyota Motor Industries Poland jako Team Leader linii montażu silników.
W kolejnych latach zarządzał dużymi zespołami w obszarze produkcji i wsparcia produkcji. Jego wiedza i umiejętności, zdobyte w Toyota, zostały rozwinięte w innych firmach, gdzie pracował jako Lean Specjalista, Trener i Menedżer Produkcji oraz działów technicznych. Jest szczególnie skuteczny w trudnych sytuacjach, wymagających szybkiej adaptacji do zmieniających się warunków rynkowych lub wewnętrznych.
Rozwijał struktury Lean zarówno globalnie, jak i lokalnie w wielu firmach. Praca w Amazon umożliwiła mu doskonalenie umiejętności w obszarze logistyki wewnętrznej branży e-commerce.
Specjalizuje się w szczególności w: budowaniu skutecznych zespołów, budowaniu i utrzymaniu systemu 5S, zwiększaniu dostępności parku maszynowego poprzez wdrożenie TPM, standaryzowaniu procesów i TWI, rozwiązywaniu problemów, SMED, budowaniu systemu ssącego kanban, doskonaleniu operacyjnym liderów i kierowników średniego szczebla.
Doświadczenie doradcze
Współpracował m.in. z: Współpracował m.in. z firmami: Sempertrans, Nowy Styl, Etisoft, Autoliv, Wkręt-met, TRW (aktualnie ZF Automotive Systems), Mayr Polska.
Agnieszka Fonfara
Doświadczenie menadżerskie
Kilkanaście lat pracowała w przedsiębiorstwach sektora spożywczego takich jak: Terravita, Lisner i Nestle Polska. Doświadczenie zdobywała w działach jakości, BHP, HR i ciągłego doskonalenia. Współtworzyła strategię organizacji, strukturę celów, system audytów i rozwiązywania problemów. Odpowiedzialna była za wdrożenie struktury spotkań operacyjnych, TPM ora wielu standardów i narzędzi korporacyjnych. Zarządzała portfelem projektów dbając o to, aby każdy z nich przebiegał zgodnie z ustalonym planem i nadanymi priorytetami. Przez kilka lat koordynowała wdrożenie Nestle Continuous Excellence dla dziewięciu fabryk koncernu, będąc jednocześnie członkiem europejskiego zespołu wdrożeniowego. To co najbardziej ją interesuje to zintegrowane doskonalenie uwzględniające wzajemne relacje pomiędzy narzędziami ciągłego doskonalenia a systemami zapewnienia jakości i bezpieczeństwa pracowników.
Specjalizuje się w szczególności w: skracaniu czasów przezbrojeń z wykorzystaniem metody SMED, rozwiązywaniu problemów w relacjach z pracownikami wg TWI, budowaniu systemu codziennego rozwiązywania problemów, TPM, Gemba Walk.
Doświadczenie doradcze
Współpracowała m.in. z: Electrolux, ZF Automotive Systems, Tauron Ciepło, Japan Tobacco International, Bridgestone, Kompania Piwowarska, Coroplast, Diehl, Nidec, Neapco, Mayr, Filplast, Fabryka Mebli Forte, MEYN, Georg Utz, JMP Flowers, System-Barosz Gwimet.
*LEI Polska zastrzega sobie prawo do zmiany trenerów prowadzących szkolenie, zapewniając odpowiednio wysoki poziom merytoryczny szkolenia
Nie udało Ci się zapisać na to szkolenie?
Skontaktuj się z nami i zapytaj o możliwość zorganizowania dodatkowego terminu.
Szkolenie na wyłączność na terenie fabryki
Jeśli chciałbyś zobaczyć, jak wybrane narzędzie lub rozwiązanie funkcjonuje na hali innej firmy, skontaktuj się z nami i zapytaj o możliwość zorganizowania tego szkolenia w formie zamkniętej (na wyłączność dla Twojej firmy) – pomożemy Ci dobrać odpowiednie przedsiębiorstwo z listy naszych firm partnerskich.
Potrzebujesz pomocy w wyborze szkolenia? Skontaktuj się z nami!
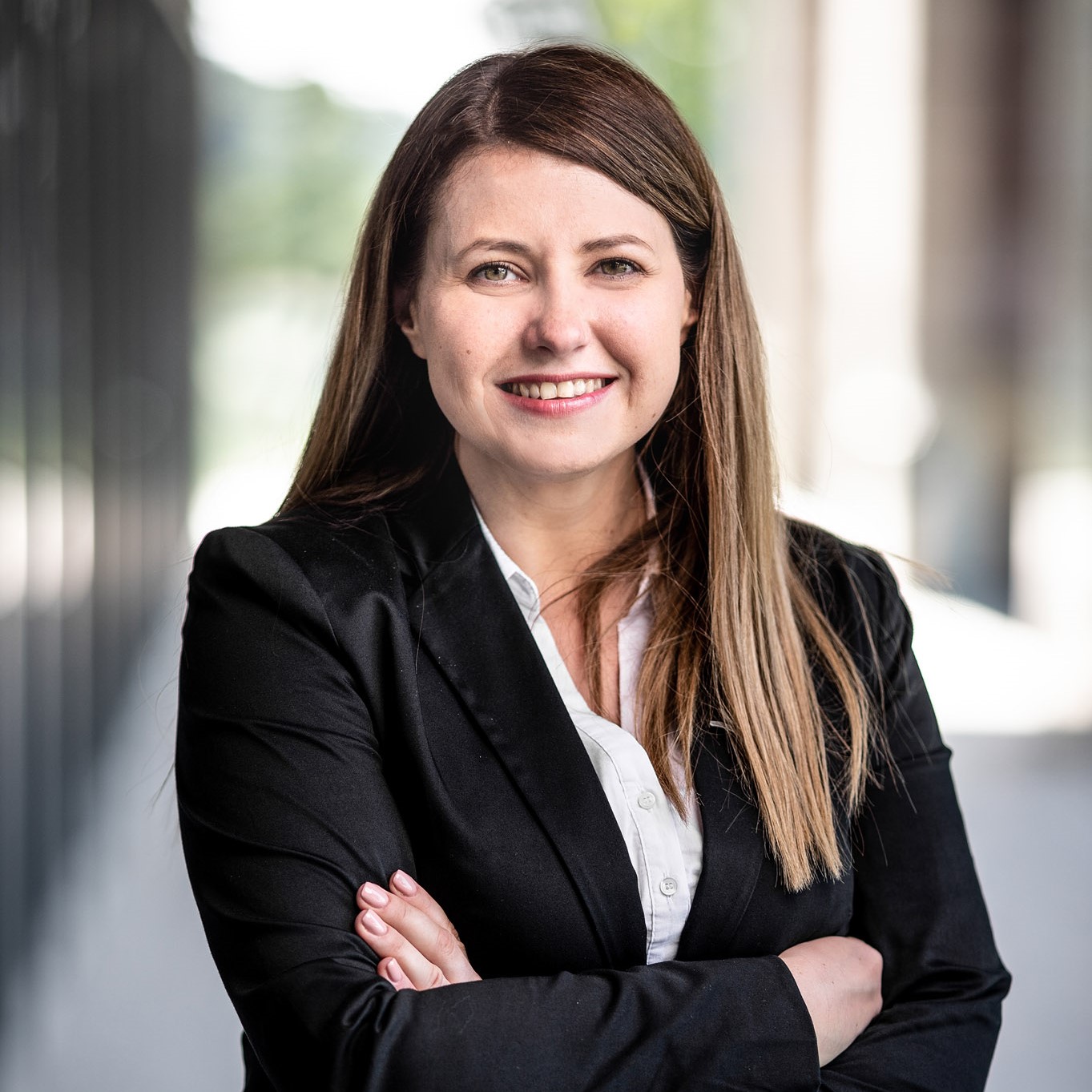
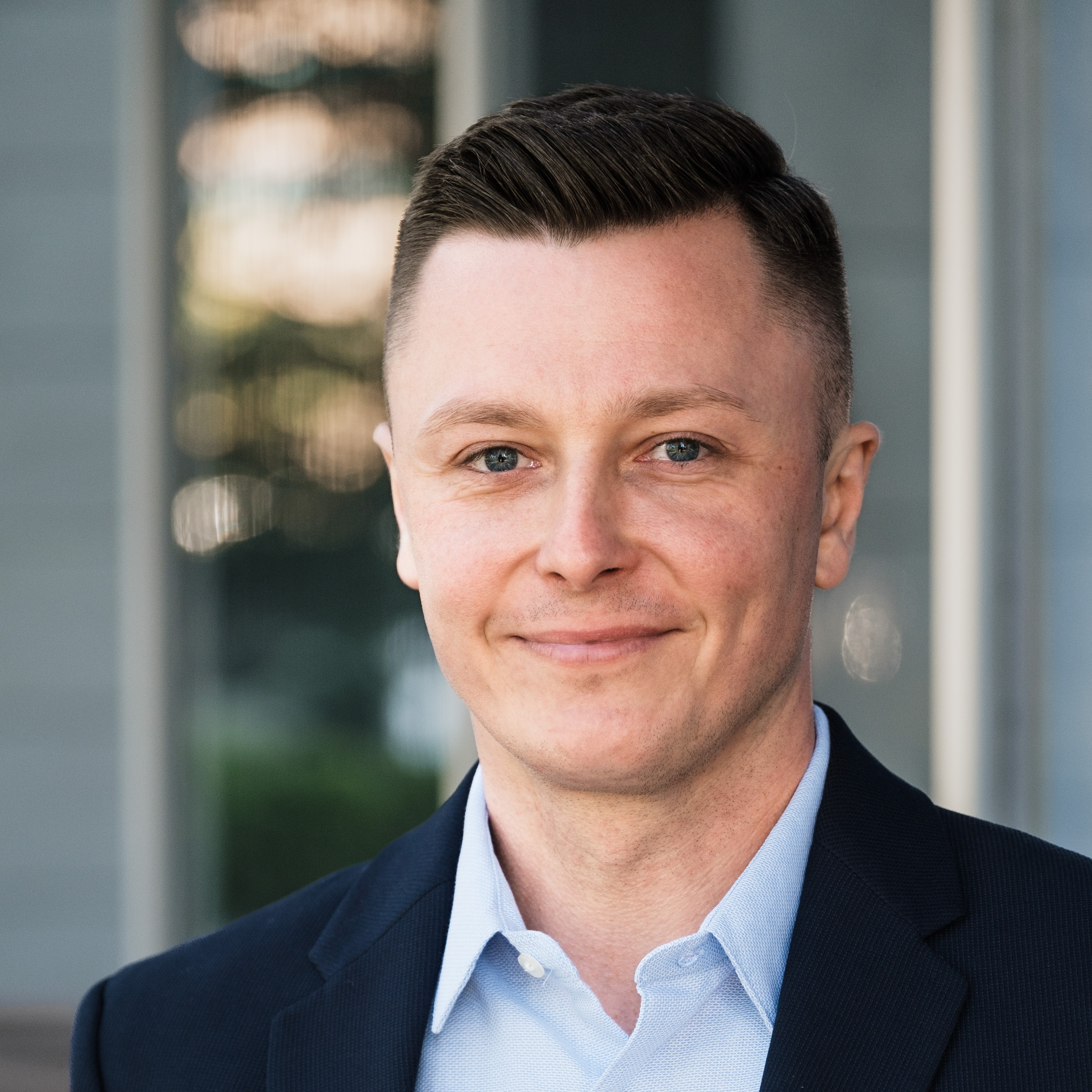
Polecane artykuły
Polecamy również inne warsztaty na terenie firm
Polecamy książki
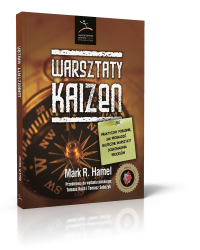
Warsztaty Kaizen
Jednym z najistotniejszych elementów know-how skutecznego wdrażania Lean są warsztaty kaizen. O ile siłą napędową każdej transformacji lean są ludzie, o tyle warsztaty kaizen są podstawową metodą angażowania w tę transformację serc i umysłów pracowników. Warsztaty kaizen uczą ludzi, jak patrzeć, myśleć i czuć zgodnie z filozofią lean i, w rezultacie, jak natychmiastowo i skutecznie wdrażać wymyślone przez nich udoskonalenia pozwalające wykorzystać szanse o dużym potencjale.
więcej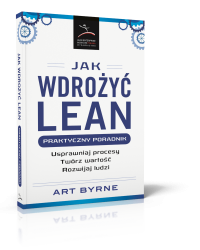
Jak wdrożyć Lean
Kompleksowo opracowane studium przypadku firmy wdrażającej Lean. Czytelnik znajdzie tu odpowiedzi na wszystkie pytania, które chciałby zadać doświadczonemu konsultantowi Lean, oraz stanie się świadkiem modelowej transformacji z udziałem całej załogi firmy.
więcej