Standaryzacja pracy: przygotowanie standardu pracy (cz. 2/3)
Przedstawiamy drugi z serii trzech artykułów poświęconych istocie standaryzacji pracy. W pierwszej części zaprezentowaliśmy czym jest standaryzacja pracy oraz jakie wynikają korzyści z jej zastosowania. W części drugiej opisujemy przygotowanie standardu pracy w podziale na dwie fazy: fazę stabilizacji oraz fazę standaryzacji procesu. Część trzecia poświęcona będzie rolom oraz zakresom odpowiedzialności pracowników i przełożonych odpowiedzialnych za utrzymanie i doskonalenie standardów i metod pracy oraz zasadom audytowania pracy standaryzowanej.
Stabilizacja i standaryzacja operacji
Przygotowanie dobrego standardu pracy wymaga obserwacji wykonywanych przez pracowników czynności, sprawdzenia ich stabilności (powtarzalności), ustalenia aktualnie najlepszej metody a następnie zapisania jej w przyjętej formie i skomunikowania wszystkim użytkownikom. W skrócie możemy podzielić ten proces na okres stabilizacji, czyli dochodzenia do aktualnie najlepszej metody i standaryzacji, czyli jej udokumentowania, jak to przedstawiono na poniższym schemacie.
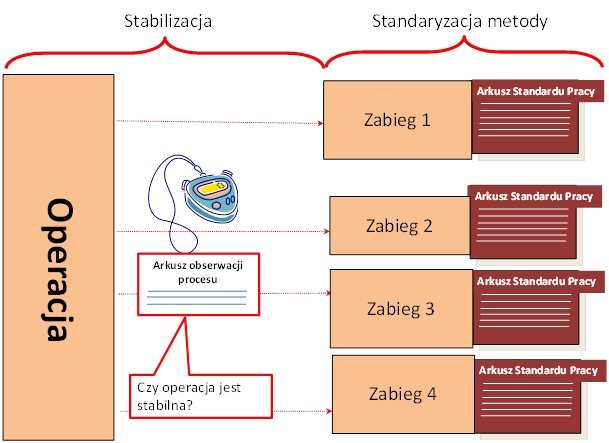
Schemat przygotowania standardu pracy
Stabilizacja operacji
Proces przygotowania standardu pracy rozpoczynamy od obserwacji całości wykonywanej przez pracownika pracy, czyli operacji. Jak to opisuje Hitoshi Takeda „aby wprowadzić pracę standaryzowaną należy obserwować aktualną sytuację i udokumentować ją jak najdokładniej się da. W rzeczywistości często jest to bardzo utrudnione, gdyż pracownicy zmieniają kolejność wykonywanych kroków, czasy osiągane przez pracowników wahają się znacznie, operatorzy zmieniają miejsca pracy lub narzędzia, czasem brakuje części lub są wadliwe itp. Dlatego też najpierw należy wprowadzić porządek do procesu, poprzez ustalenie kolejności wykonywanych zadań i ich podział na podstawowe i pomocnicze” 1.
W trakcie obserwacji procesu będziemy starali się określić trzy podstawowe fakty. Zdecydujemy:
- od czego operacja się zaczyna, na czym się kończy,
- z jakich kroków operacja się składa,
- czy kolejne cykle operacji są wykonywane w powtarzalnym czasie, a jeżeli nie, czy wahania czasów są dla nas zrozumiałe.
Przy obserwacji całości operacji możemy się posłużyć arkuszem roboczym, tzw. Arkuszem obserwacji procesu.
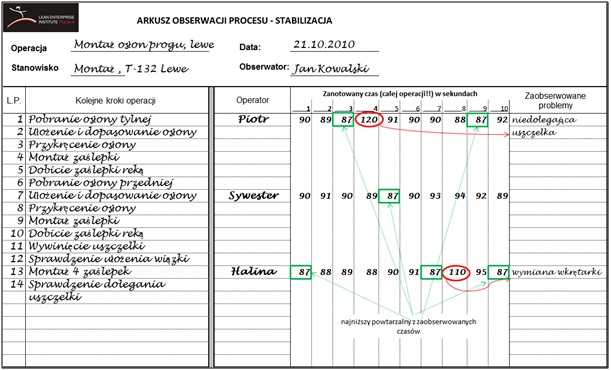
Przykład wypełnionego arkusza obserwacji procesu (na podstawie M. Rother, R. Harris, Tworzenie ciągłego przepływu, Wydawnictwo Lean Enterprise Institute Polska, Wrocław 2009).
Celem arkusza obserwacji procesu jest przekonanie się o stopniu stabilizacji procesu i uzyskanie ogólnej orientacji w kolejności kroków wykonywanych w procesie.
Jak skorzystać z arkusza:
- Określ obserwowany proces, wpisz jego nazwę w pole „operacja” a lokalizację w pole „stanowisko”.
- Zapisz datę obserwacji i nazwisko obserwatora.
- Określ operatora. Najlepsze rezultaty osiąga się przy obserwacji kilku różnych operatorów.
- Określ punkt początkowy i końcowy cyklu.
- Zmierz zaobserwowane czasy cyklu operatora/operatorów.
- Jeżeli podczas obserwacji cyklu zauważysz, że operator napotkał jakiś problem, zanotuj go w kolumnie „Napotkane problemy” (na przykład upuszczone wkręty, konieczność ponownego ułożenia części, niewłaściwe oświetlenie).
- Podczas mierzenia czasu staraj się już zanotować poszczególne kroki operatora w wykonywanej sekwencji.
Arkusz obserwacji procesu jest arkuszem roboczym – będziemy korzystać z wniosków powstałych przy jego wypełnieniu, ale nie będziemy go nigdzie wywieszać ani przechowywać.
Jako że do etapu standaryzacji możemy przejść tylko wówczas, gdy proces ocenimy jako stabilny (czyli gdy występujące wahania czasu cyklu operatorów dadzą się wytłumaczyć zaobserwowanymi zdarzeniami), w przeciwnym razie musimy podjąć działania stabilizujące, wykorzystując na przykład jedno z narzędzi programu Training Within Industry – Doskonalenia Metod Pracy 2
Standaryzacja operacji Po ustabilizowaniu procesu i wypracowaniu aktualnie najlepszej metody pora na jego zestandaryzowanie, czyli udokumentowanie w uzgodnionym formacie. Przy standaryzacji procesów będziemy posługiwać się pojęciem „zabiegu”.
Podział operacji na zabiegi
Każdą operację można podzielić na zabiegi. Zabieg definiujemy jako logiczne zgrupowanie czynności, które prowadzą do pomyślnego ukończenia pracy.
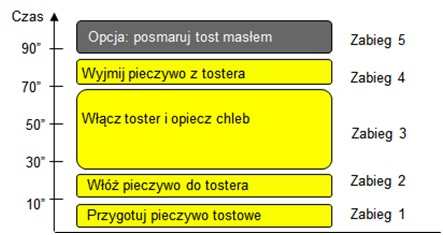
Przykład podziału czynności domowej na zabiegi (opcja: tost z masłem)
Czasami określa się też zabiegi jako klocki, z których zbudowana jest praca standaryzowana, co dobrze oddaje fakt, że zabieg powinien być takim zgrupowaniem czynności, które w pewnym sensie stanowią całość i dadzą się przesuwać z jednego procesu do drugiego. Nie istnieje jedna, „jedynie słuszna” metoda podziału operacji na zabiegi. Procesy charakteryzuje różnorodność i można je niejednokrotnie podzielić na logiczne, mniejsze części na kilka sposobów. Przy podziale możemy się jednak kierować pewnymi wskazówkami, zastanawiając się:
- Gdzie wykonywane są czynności? Czy można zgrupować je w zależności od miejsca wykonywanej pracy?
- Czy można wydzielić pracę nad konkretną częścią produktu? Innymi słowy, czy można wydzielić pracę nad przodem lub tyłem produktu, napędem, lampą itp.
- Jaki jest czas danej czynności? Pewną wskazówką może być podział czasu operacji na zabiegi, zabierające mniej więcej równe odcinki czasu. Bardzo krótkie operacje (np. kilkanaście sekund) z reguły będą w całości jednym zabiegiem.
- Czy jest to opcja wymagająca dłuższego czasu? Opcje mogą zawierać się w danym zabiegu, ale jeżeli zabierają znaczną (w porównaniu do trwania operacji) ilość czasu, warto wyłączyć je jako osobne zabiegi.
- Czy jest to podmontaż? Wyłączenie podmontażu jako jednego lub kilku zabiegów jest reguły najlepszym rozwiązaniem.
- Często pierwszym zabiegiem może być pobranie części.
- Czynności nie dodające wartości (przejście, czekanie) zazwyczaj oddzielają jeden zabieg od drugiego.
Dzięki podziałowi całości operacji na zabiegi, proces nabiera charakteru modułowego i można go dostosowywać do zmieniających się warunków, przy utrzymaniu standardowej metody wykonania, jak przedstawiono na rysunku poniżej.
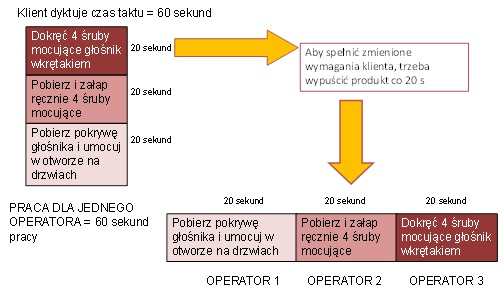
Przykład zastosowania podziału operacji na zestandaryzowane zabiegi w celu dostosowania procesu do spełnienia zmiennych wymogów klienta
W sytuacji mniejszego zapotrzebowania na produkt pracę wykonuje jeden operator, w przypadku jednak, gdy zapotrzebowanie wzrasta i trzeba przyśpieszyć linię (gniazdo), ta sama praca może być rozdzielona na trzech operatorów według wcześniej określonych zasad. W ten sposób zmienia się liczba operatorów, ale metoda wykonywania całej czynności pozostaje bez zmian i modyfikacje w poziomie zapotrzebowania nie wpływają na poziom standaryzacji pracy.
Dokumentowanie zabiegów: Arkusz Podziału Pracy
W celu udokumentowania zabiegów pracy posługujemy się Arkuszami Podziału Pracy, które stanowią narzędzie dostarczające informację o kolejności, metodzie, bezpieczeństwie i jakości wykonywanej pracy. Arkuszami Podziału Pracy dokumentują:
- metodę wykonania zabiegu (Co?, Jak?, Dlaczego?),
- czas zabiegu,
- przeprowadzone udoskonalenia,
- problemy BHP,
- problemy jakościowe,
- lokalizację zabiegu w całości procesu.
Są również narzędziem równoważenia (balansowania) linii.
Przykładowy arkusz podziału pracy przedstawiono na poniższym rysunku.
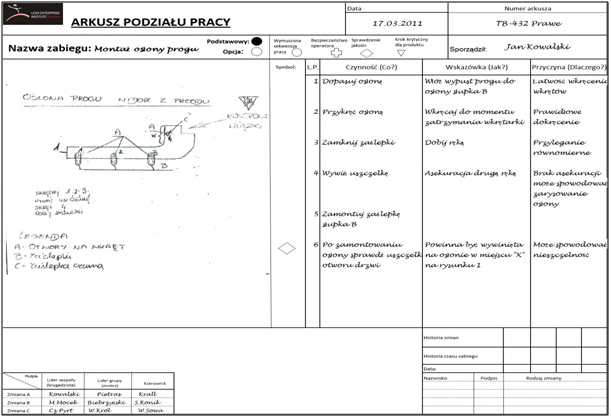
Przykład Arkusza Podziału Pracy
Wypełniając arkusz umieszczamy informacje podstawowe o nazwie, lokalizacji zabiegu, jego charakterze (czy jest to zabieg podstawowy czy opcja), operacji, w której skład wchodzi oraz autorze arkusza.
W kolumnie „Co?” zapisujemy kolejne działania, które posuwają wykonanie pracy do przodu.
W kolumnie „Jak?”zapisujemy w jaki sposób należy wykonać działanie opisane w kolumnie „Co?”, na co należy zwrócić uwagę, czy można sobie ułatwić wykonanie działania, czy należy zastosować jakieś konkretne narzędzie lub przyrząd, sposób ustawienia obrabianego przedmiotu, temperaturę, wilgotność, inne parametry itp. Wskazówki podane w kolumnie „Jak?” dotyczyć będą trzech kategorii:
- Dobre wykonanie pracy: wskazówki, od których zastosowania zależy sukces lub porażka wykonywanej pracy.
- Bezpieczeństwo : wskazówki , jak uniknąć ewentualnych zagrożeń dla zdrowia pracownika.
- Ułatwienia: wskazówki, które ułatwiają wykonanie pracy (np. na co należy zwracać uwagę, „skróty”, doświadczenie, technika, czas, wiedza specjalistyczna).
W kolumnie „Dlaczego?” wyjaśniamy dlaczego działanie należy wykonać w ten a nie inny sposób. Wpisy w tej kolumnie odpowiadają na pytanie, „dlaczego trzeba wykonać pracę w ten właśnie sposób?”, nie na pytanie „dlaczego trzeba to wykonać?”. Podawane w tej kolumnie powody powinny być konkretne, czyli „możliwość przecięcia nadgarstka” albo „silnik nie zastartuje” a nie na przykład „dla bezpieczeństwa” czy „dla jakości.”
Ostatnia – trzecia część artykułu – poświęcona będzie rolom oraz zakresom odpowiedzialności pracowników i przełożonych odpowiedzialnych za utrzymanie i doskonalenie standardów i metod pracy oraz zasadom audytowania pracy standaryzowanej.
Małgorzata Jakubik, LEI Polska
Aby dowiedzieć się więcej na temat standaryzacji pracy, przeczytaj mi.in. książkę Jima Lancastera Standaryzowana praca menedżera. Książka ukazała się nakładem Wydawnictwa Lean Enterprise Institute Polska i jest dostępna w księgarni internetowej leanbooks.pl.
Chcesz dowiedzieć się więcej i zdobyć umiejętności praktyczne? Weź udział w naszych szkoleniach:
Standaryzacja pracy z wykorzystaniem podejścia TWI Doskonalenia Metody Pracy (POZIOM 1) – zapisz się >
Doskonalenie procesów z wykorzystaniem standaryzacji pracy (POZIOM 2) – zapisz się >